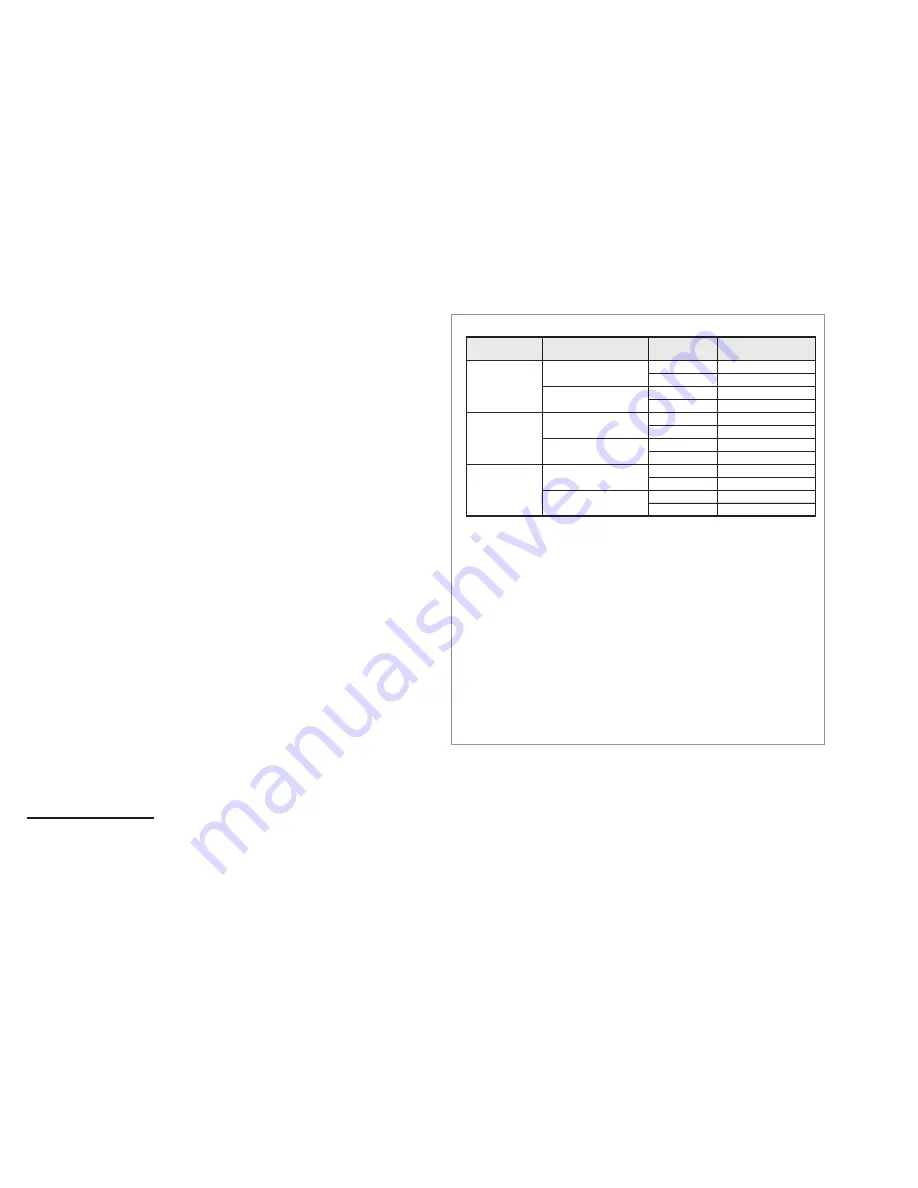
6
• Bearings should be inspected as recommended in the
Lubrication
Conditions Chart.• Inspect variable inlet
vanes for freedom of operation and excessive wear.
The vane position should agree with the position of the
control arm. As the variable inlet vanes close, the
entering air should spin in the same direction as the
wheel.
• Inspect springs and rubber isolators for deterioration
and replace as needed.
• Inspect for cleanliness. Clean exterior surfaces only.
Removing dust and grease on motor housing assures
proper motor cooling. Removing dirt from the wheel
and housing prevent imbalance and damage.
Lubrication - Fan Bearings
Greasable fan bearings are lubricated through a grease
fitting on the bearing.
For best results, lubricate the bearing while the fan is in
operation. Pump grease in slowly until a slight bead forms
around the bearing seals. Excessive grease can burst
seals thus reducing bearing life.
Before lubricating, the grease nipple and immediate
vicinity should be thoroughly cleaned without the use of
high pressure equipment. The grease should be supplied
slowly as the bearing rotates until fresh grease slips past
the seal. Excessive pressure should be avoided to prevent
seal damage.
In the event the bearing cannot be seen, use no more
than three injections with a hand-operated grease gun.
NOTICE! Loren Cook Company uses petroleum
lubricant in a lithium base. Other types of grease
should not be used unless the bearings and lines have
been flushed clean. If another type of grease is used, it
should be a lithium-based grease conforming to NLGI
grade 2 consistency. A NLGI grade 2 grease is a light
viscosity, low-torque, rust-inhibiting lubricant that is
water resistant. Its temperature range is from -30
F to
Exceptions to the greasing interval chart:
1. Periodic Applications (any break of one week or
more): it is recommended that full lubrication be
performed prior to each break in operation.
2. Higher Temperature:
it is recommended to
halve the intervals for every 30
F increase in
operating temperature above 120
F not to
exceed 230
F for standard bearings; High Tem-
perature bearings (optional) can operate up to
400
F.
3. Vertical Shaft: it is recommended that the inter-
vals should be halved.
Lubrication Conditions Chart
Fan Class
Fan Status
Shaft Size
Maximum Interval
(operational hrs)
Centrifugal
Blower
Class I
Normal Conditions
(Clean, Dry & Smooth)
> 1-1/2”
10,000
< 1-1/2”
2,000
Extreme Conditions
(Dirty/Wet/Rough)
> 1-1/2”
2,000
< 1-1/2”
400
Centrifugal
Blower
Class II
Normal Conditions
(Clean, Dry & Smooth)
> 2”
7,500
< 2”
1,000
Extreme Conditions
(Dirty/Wet/Rough)
> 2”
1,500
< 2”
200
Centrifugal
Blower
Class III
Normal Conditions
(Clean, Dry & Smooth)
> 2”
3,000
< 2”
500
Extreme Conditions
(Dirty/Wet/Rough)
> 2”
500
< 2”
100
Use of Variable Frequency Drives
Motors
Motors that are to be operated using a Variable
Frequency Drive (VFD) must be VFD compatible. At a
minimum, this must be a Premium Efficiency motor with
Class F insulation. Motors that are not supplied by Loren
Cook Company should have the recommendation of the
motor manufacturer for use with a VFD.
Grounding
The fan frame, motor and VFD must be connected to a
common earth ground to prevent transient voltages from
damaging rotating elements.
Wiring
Line reactors may be required to reduce over-voltage
spikes in the motors. The motor manufacturer should be
consulted for recommended line impedence and usage of
line reactors or filters, if the lead length between the VFD
and the motor exceeds 10 feet (3m).
Fan
It is the responsibility of the installing body to perform
coast-down tests and identify any resonant frequencies
after the equipment is fully installed. These resonant
frequencies are to be removed from the operating range of
the fan by using the “skip frequency” function in the VFD
programming. Failure to remove resonant frequencies
from the operating range will decrease the operating life of
the fan and void the warranty.
Inspection
Inspection of the fan should be conducted at the first
30
minute, 8 hour and 24
hour
intervals of satisfactory
operation. During the inspections, stop the fan and inspect
as per the Conditions Chart.
30 Minute Interval
Inspect bolts, setscrews, and motor mounting bolts.
Adjust and tighten as necessary.
8 Hour Interval
Inspect belt alignment and tension. Adjust and tighten as
necessary.
24 Hour Interval
(belt drive) Inspect belt tension, bolts, setscrews, and
motor mounting bolts. Adjust and tighten as necessary.
Maintenance
Establish a schedule for inspecting all parts of the fan.
The frequency of inspection depends on the operating
conditions and location of the fan.
Inspect fans exhausting corrosive or contaminated air
within the first month of operation. Fans exhausting
contaminated air (airborne abrasives) should be inspected
every three months.
Regular inspections are recommended for fans
exhausting non-contaminated air.
It is recommended the following inspection be conducted
twice per year.
• Inspect bolts and setscrews for tightness. Tighten as
necessary. Worn setscrews should be replaced
immediately.
• Inspect belt wear and alignment. Replace worn belts
with new belts and adjust alignment as needed. See
the Belt and Pulley Installation.
Содержание CA DWDI
Страница 15: ...15...