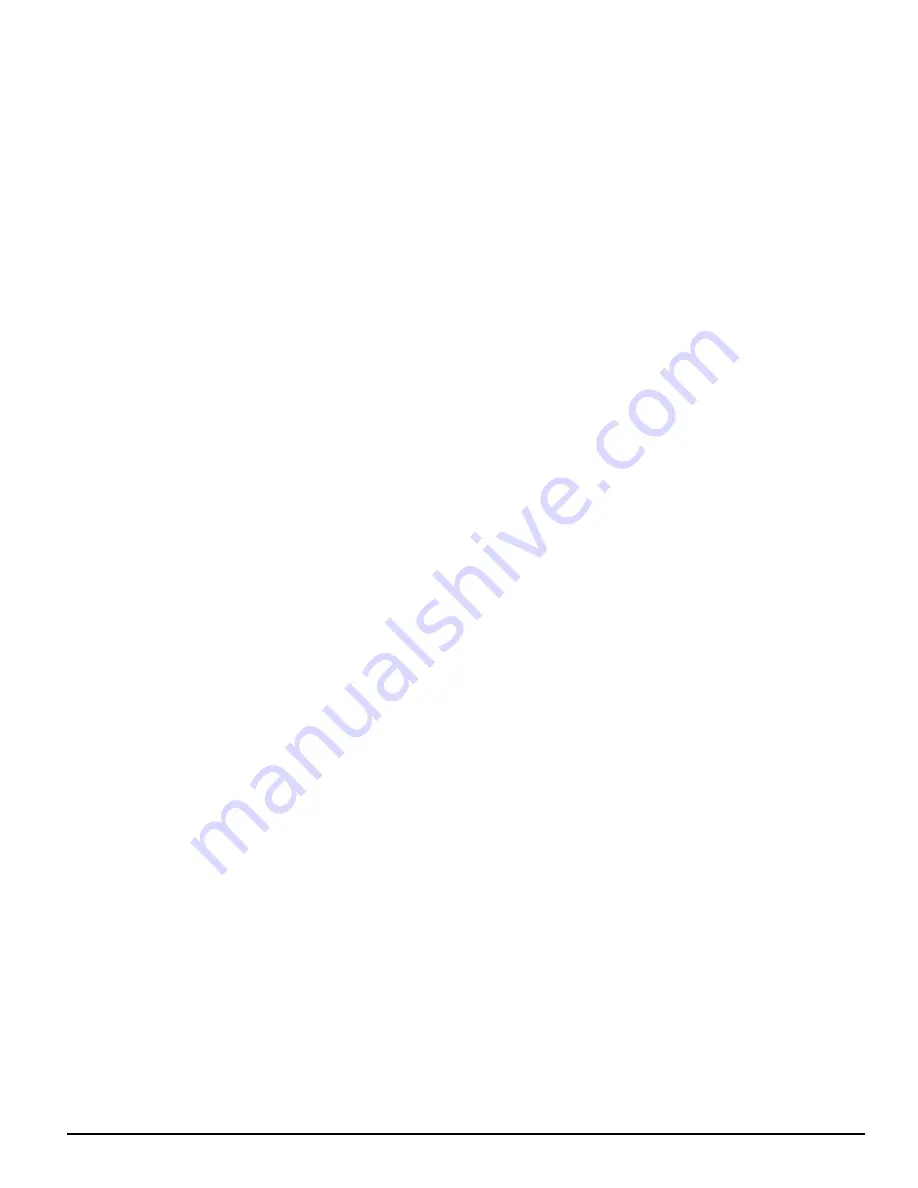
99
Tuning Procedures
The drive uses closed loop controllers to control the position and velocity Travel Limit of the attached motor. These position
and velocity controllers and the associated tuning parameters are in effect when the drive is in velocity or pulse mode and
have no effect when the drive is in Torque mode.
Many closed loop controllers require tuning using individual user-specified proportional, integral and derivative (PID) gains
which require skilled “tweaking” to optimize. The combination of these gains along with the drive gain, motor gain, and
motor inertia, define the system bandwidth. The overall system bandwidth is usually unknown at the end of the tweaking
process. The drive closes the control loops for the user using a state-space pole placement technique. Using this method, the
drive’s position control can be simply and accurately tuned. The overall system’s bandwidth can be defined by a single user-
specified value (Response).
The drive’s default settings are designed to work in applications with up to a 10:1 load to motor inertia mismatch. Most
applications can operate with this default setting.
Some applications may have performance requirements which are not attainable with the factory settings. For these
applications a set of measurable parameters can be specified which will set up the internal control functions to optimize the
drive performance. The parameters include Inertia Ratio, Friction, Response and Line Voltage. All the values needed for
optimization are “real world” values that can be determined by calculation or some method of dynamic measurement.
PID vs. State-Space
The power of the state-space control algorithm is that there is no guessing and no “fine tuning” as needed with PID methods.
PID methods work well in controlled situations but tend to be difficult to setup in applications where all the effects of the
system are not compensated for in the PID loop. The results are that the system response is compromised to avoid instability.
The drive state-space control algorithm uses a number of internally calculated gains that represent the wide variety of effects
present in a servo system. This method gives a more accurate representation of the system and maximizes the performance
by minimizing the compromises.
You need only to setup the system and enter three parameters to describe the load and the application needs. Once the entries
are made the tuning is complete - no guessing and no “tweaking”. The drive uses these entries plus motor and amplifier
information to setup the internal digital gain values. These values are used in the control loops to accurately set up a stable,
repeatable and highly responsive system.
Tuning Procedure
Once the initial setup has been completed, you can run the system to determine if the level of tuning is adequate for the
application. A drive can be tuned basically to four levels.
• No Tuning
• Basic Level
• Intermediate Level
• Fully Optimized Level
Each level is slightly more involved than the previous one requiring you to enter more information. If your system needs
optimization, we recommend that you start with the Basic Level, then determine if further tuning is needed based on axis
performance.
The setup procedures explained here assume that you are using PowerTools Pro software or an FM-P.
Initial Settings
S
et the drive tuning parameters as follows:
• Inertia Ratio = 0
• Friction = 0
• Response = 50
• High Performance Gains = Enabled
• Feedforwards = Disabled
Epsilon EP-I Indexing Drive and FM-2 Indexing Module
Reference Manual
Содержание Epsilon EP-I
Страница 2: ......
Страница 49: ...39 Setting Up Parameters Figure 30 Graphical Plot ...
Страница 50: ...40 Epsilon EP I Indexing Drive and FM 2 Indexing Module Reference Manual ...
Страница 108: ...98 Epsilon EP I Indexing Drive and FM 2 Indexing Module Reference Manual ...
Страница 118: ...108 Epsilon EP I Indexing Drive and FM 2 Indexing Module Reference Manual ...
Страница 124: ...114 Epsilon EP I Indexing Drive and FM 2 Indexing Module Reference Manual Figure 101 Diagnostic Cable DGNE Diagram ...
Страница 146: ...136 Epsilon EP I Indexing Drive and FM 2 Indexing Module Reference Manual ...
Страница 155: ...145 Specifications FM 2 Dimensions and Clearances Figure 120 FM 2 Module Dimensions ...
Страница 168: ...158 Epsilon EP I Indexing Drive and FM 2 Indexing Module Reference Manual ...
Страница 175: ......