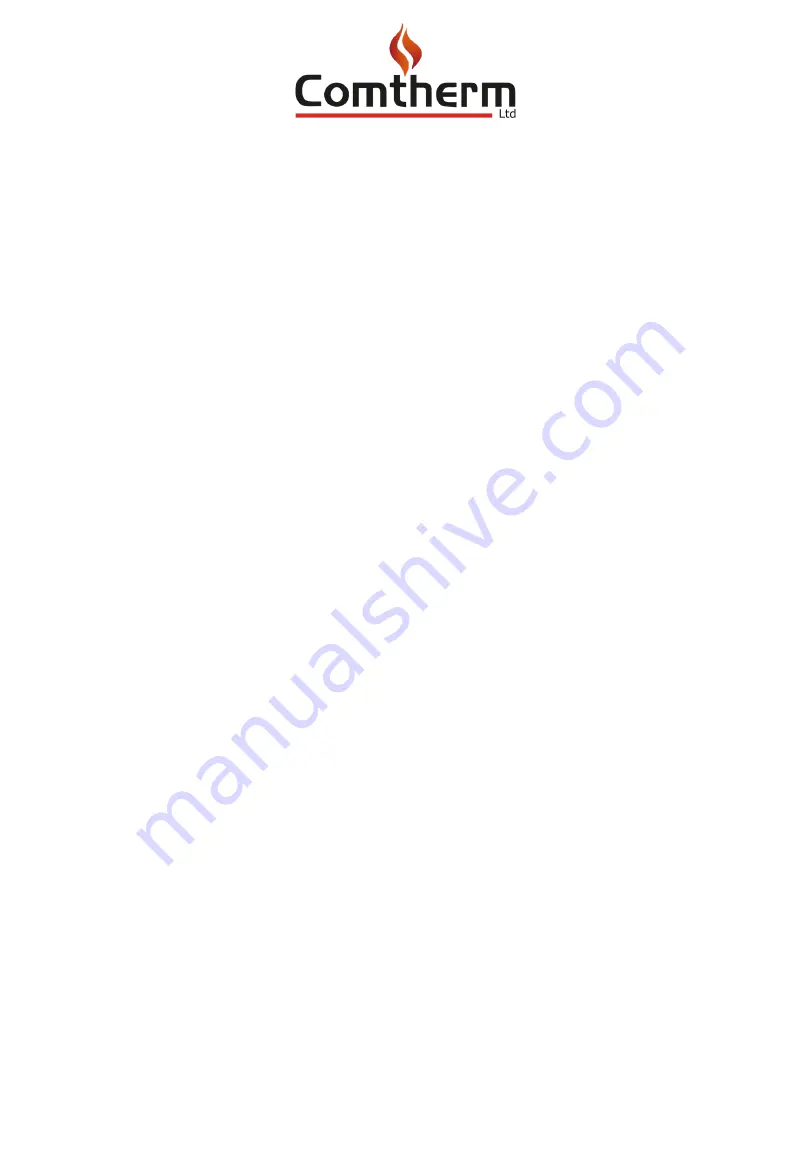
Before proceeding with the installation of the burner, inspect the burner for any physical
damage that may have occurred during transit, storage or off-loading. Any damage should
be reported immediately.
The pipe work or gas valves on the burner should not be used for lifting under any
circumstances, as this tends to pull fittings loose or damage valves, causing leaks during later
operation.
Mount the burner in the firing position, making sure that adequate space is allowed around
the burner for ventilation and that the combustion air inlet is not blocked. Ensure that an
adequate fresh air supply is available for combustion and general ventilation.
Situations where gas from valve and pipe work leaks can collect and form pockets of
combustible gas/air must be avoided.
Ensure that adequate space is allowed around the burner for easy access to all burner
components, pressure switches, control operators etc.
The burner should be securely fixed and the transmission of vibration and heat should be
minimised.
GAS SUPPLY:
Gas piping to the burner should be of sufficient size to provide the correct gas pressure at the
burner valve assembly inlet (see specification in document M1). If in any doubt concerning
the size and design of the gas supply pipe work, consult the gas supply company.
The pressure loss in the gas supply pipe work should be such that the following pipeline
velocities are not exceeded:
Unfiltered supply 20M/s (65.6ft.sec)
Filtered supply (250microns) 45M/s (148ft.sec)
The above stated velocities are based on the avoidance of excessive noise pollution and
erosion.
For low-pressure supplies up to 25 mbar (10 w.c), the pressure drop between the meter and
the burner inlet should normally not exceed 1mbar (0.4 w.c). For high-pressure supplies, this
pressure drop should not exceed 10% of the available gas pressure.
Installation
Comtherm Ltd
Installation & Maintenance Manual
Page 03
Burners, Heaters & Combustions Systems