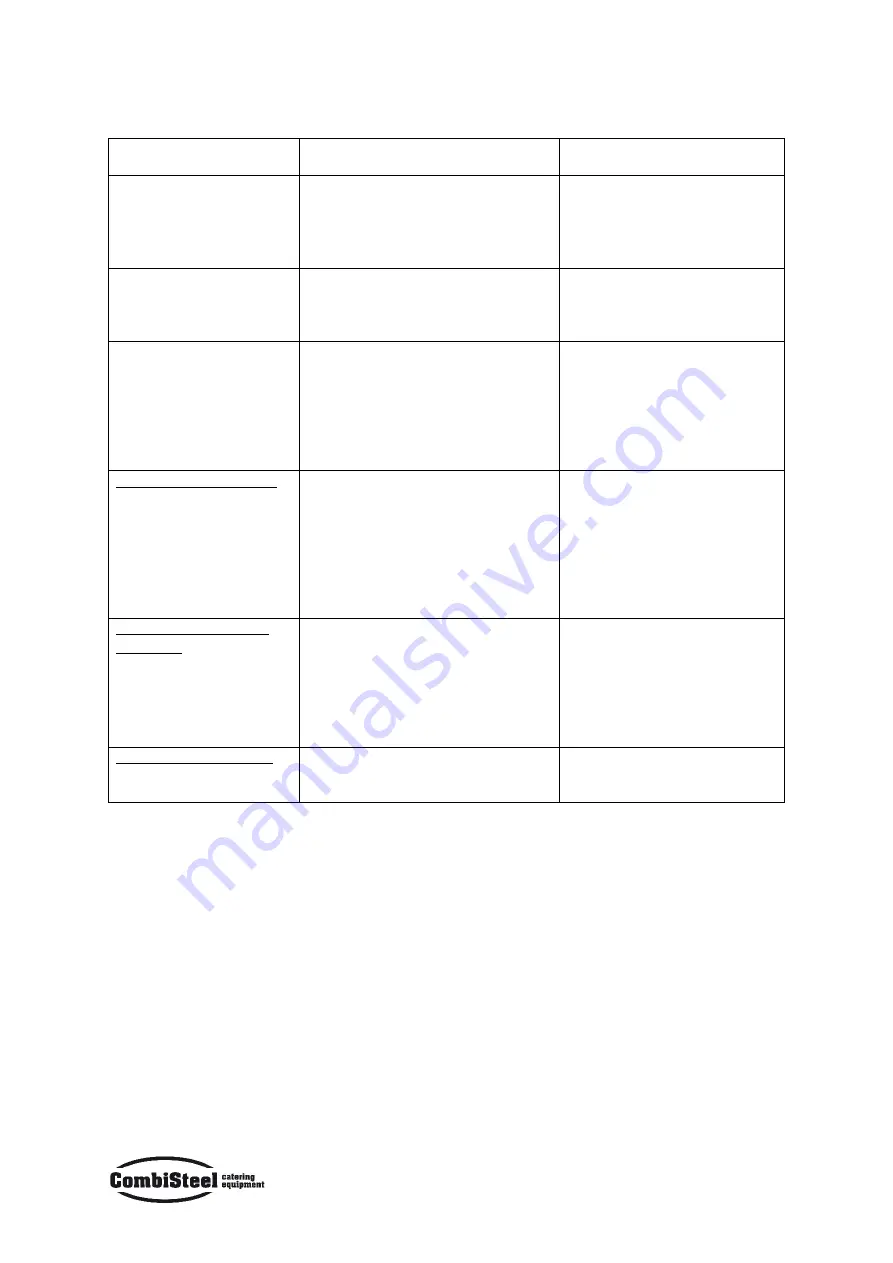
12
www.combisteel.com
Troubleshooting
PROBLEM
CAUSE
SOLUTION
The dispenser is not working 1. The dispenser may not be connected
to electricity.
2. The fuse may be blown.
3. Thermal protector may be off.
4. Thermostats may be off.
1. Connect the dispenser to the
mains.
2. Check the fuse
3. Wait some time.
4. Turn on the thermostat.
The dispenser does not cool
1. The condenser may be very
contaminated.
2. Air circulation may not be sufficient
around the dispenser.
1. Clean the condenser with a
brush.
2. Make sure that there is enough
air flow around the machine.
The tap constantly drips
1. The tap nozzle may be contaminated.
2. The tap hose o-ring may be torn.
3. The tap hose may not be securely
placed.
4. The tap spring may be hardened.
1. Clean the nozzle.
2. Check the o-ring of the faucet
hose.
3. Be sure that the faucet hose is
securely placed.
4. Check the tap spring and if
needed replace with a new one.
Valid for SPRAY Dispensers:
There is no SPRAY function
(7065.0015)
1. The snail magnet may be inserted
upside down.
2. The pump magnet can be covered
with sugar.
3. Fruit particles may be stuck under
the magnet.
4. The magnet washer may not be in
place.
1. Remove the pump and clean.
2. Remove the magnet and clean
3. Press down the pump pin.
4. Put the washer in place.
Valid for MIXER and KAM
Dispensers:
There is no Mixing
(7065.0020)
1. Oil may have accumulated on the
pallet.
2. The mixer pallet magnet might have
been fitted upside down.
3. The pallet may not be installed in
place.
1. Remove the palette and clean it
with lukewarm water.
2. Re-place the magnet by making
sure that the magnet is facing
down.
3. Re-place the palette.
Valid for KAM Dispensers:
Liquid flows from the tap
nozzle
The gaskets of the foaming apparatus
may be deformed or not fully fitted.
Ensure that all gaskets of the
foaming apparatus are in place
and not deformed.