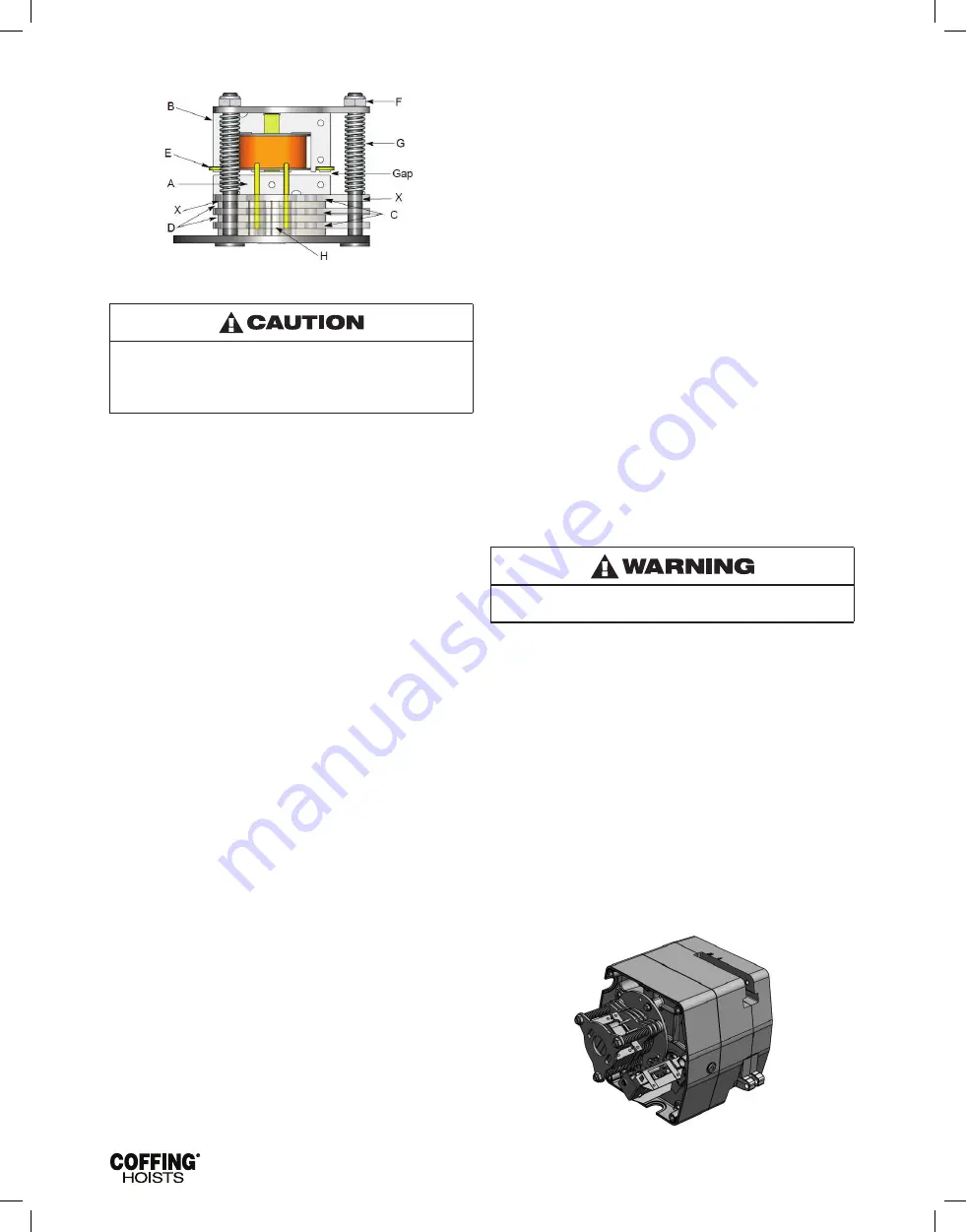
10
JLC680-2 Rev AA
April 2019
Figure 5 — Brake Assembly
Be sure the bottom of the armature "A "does not bear against
the splined adapter “H”. As adjustments are made, the built-
in clearance will be reduced. When this clearance is gone
REPLACE BRAKE DISCS. Minimum allowable disc thickness is
.162".
5-7 HOIST CONTROLS
Both the pushbutton and the reversing contactor are mechanically
interlocked to prevent shorting the circuit and causing serious
damage. As part of maintenance, always check for proper closure
of contact points as well as for burned contacts. If replacement is
necessary, see Figures 16, 17, 18, and 19 for replacement parts.
5-8 WIRING
Refer to Figures 9A, 9B, 9C & 9D.
Single-phase units (115/230V) are shipped wired for 115V and
the 1-speed, 230/460V-3 phase units are wired for 460V unless
otherwise specified when ordered. Hoists wired for other voltages
and 2-speed units are single voltage only. Conversion of dual-
voltage hoists to either the higher or lower voltage can be done
simply and quickly as follows:
1. DISCONNECT HOIST FROM POWER SUPPLY and remove the
electrical cover.
2. Each dual-voltage hoist has a terminal block assembly for the
interconnection of the electrical components of the hoist. To
convert the voltage, reconnect the leads to the terminal blocks
according to the wiring diagram located inside the electrical
cover or Figures 9A, 9B, 9C and 9D.
DO NOT move any wires or make any changes to the
electrical circuit except at the terminal block assembly.
Tug on wires to ensure they are securely connected.
3. After converting the voltage, recheck phasing and limit switch
operation (See INSTALLATION 3-c & 5, page 5).
IMPORTANT:
Always refer to the wiring diagram located on the
inside of the electrical cover or Figures 9A, 9B, 9C and 9D when
performing electrical repairs. Make sure all connections are secure
and check for damaged insulation. It is also imperative that the
power circuit has conductors of adequate size (See Table 5).
5-9 LUBRICATION
Refer to Figure 11.
Proper lubrication is necessary for a long and relatively trouble-free
hoist operation. Refer to the following and the RECOMMENDED
LUBRICATION SCHEDULE for lubrication points, type of lubricant,
and frequency of lubrication.
LOAD CHAIN
Clean the load chain with acid-free solvent and coat with SAE 90 Wt.
gear oil. Wipe excess oil to prevent dripping. Never apply grease to
the chain.
GEARING
The gear case of this hoist is filled at assembly with approximately
2 pints of SAE 90 Wt. EP gear oil. Check oil level by removing the
oil level fill plug from the side of the hoist. With the hoist hanging
level, gear oil should be even with the hole. Change oil periodically
depending on the severity of the application and the environmental
conditions (at least every 200 hours of run time).
BEARINGS
All bearings except hook and idler sheave bearings are lubricated
at the factory and should not require additional lubrication. Noisy or
worn bearings should be replaced.
LIMIT SWITCH SHAFT
Remove any dirt accumulation and spray with a general purpose
lubricant.
HOOK BEARING
Apply a few drops of SAE 30 Wt. gear or motor oil around the edge
of the bearing.
IDLER SHEAVE BEARING (BUSHING)
Disassemble load block and apply a light coat of NLGI #2 grease, or
equivalent, inside of bearing.
5-10 HOIST REPAIRS
1. For major repairs or when the hoist is to be sectioned in the
suspension area, it will be necessary to move the hoist to a
workbench or table.
2. For repairs which can be done by removing the electrical cover
only, the hoist need not be moved. Lowering the hoist to a
convenient working level is desirable.
NOTE:
If you do not have an experienced mechanic to do your
repair work, we recommend that you send your hoist to an approved
service station for repairs. Use authorized repair parts only.
Remove load and disconnect hoist from power supply before
starting to do any repairs or to take any sections apart.
The following repair instructions will help you in understanding repair
procedures, when related to the Replacement Parts List starting on
page 21. For clarity these are broken down into areas.
ELECTRICAL PARTS AND BRAKE
1. Refer to Figures 15, 16 and 17. Remove the cover to access
the controls. Single-phase models also have a starting switch
and capacitor mounted on the panel as shown in Figure 16.
The terminal blocks and end clamps snap off of the rails on the
panel plate using a small screwdriver. DO NOT SLIDE THE END
CLAMPS. The reversing contactor can be slid off the rail, but it
must be snapped on. Where the contactor fits the rail, one side
has springs or pads that apply pressure against the edge of the
rail. By pressing against that side at the base of the contactor,
you can snap the part on or off using a rotating action. Note the
numbers that label the terminals on the contactor and orient the
part as shown in Figures 9A-9D. Single-phase contactors have
a small jumper that is not present on the 3-phase (note the 3
and 5 terminals on the reversing contactor in Figure 9A).
2. Remove the electrical panel by removing the stand-off screws
(See Figures 16 & 17). The limit switch and brake are now
accessible as shown in Figure 6.
Figure 6 — Electrical Panel Removed
Содержание Coffing JLC Series
Страница 35: ...33 JLC680 2 Rev AA April 2019 FIGURE 23 TRANSMISSION...
Страница 37: ...35 JLC680 2 Rev AA April 2019 FIGURE 24 CHAINING PARTS...
Страница 39: ...37 JLC680 2 Rev AA April 2019 NOTES...