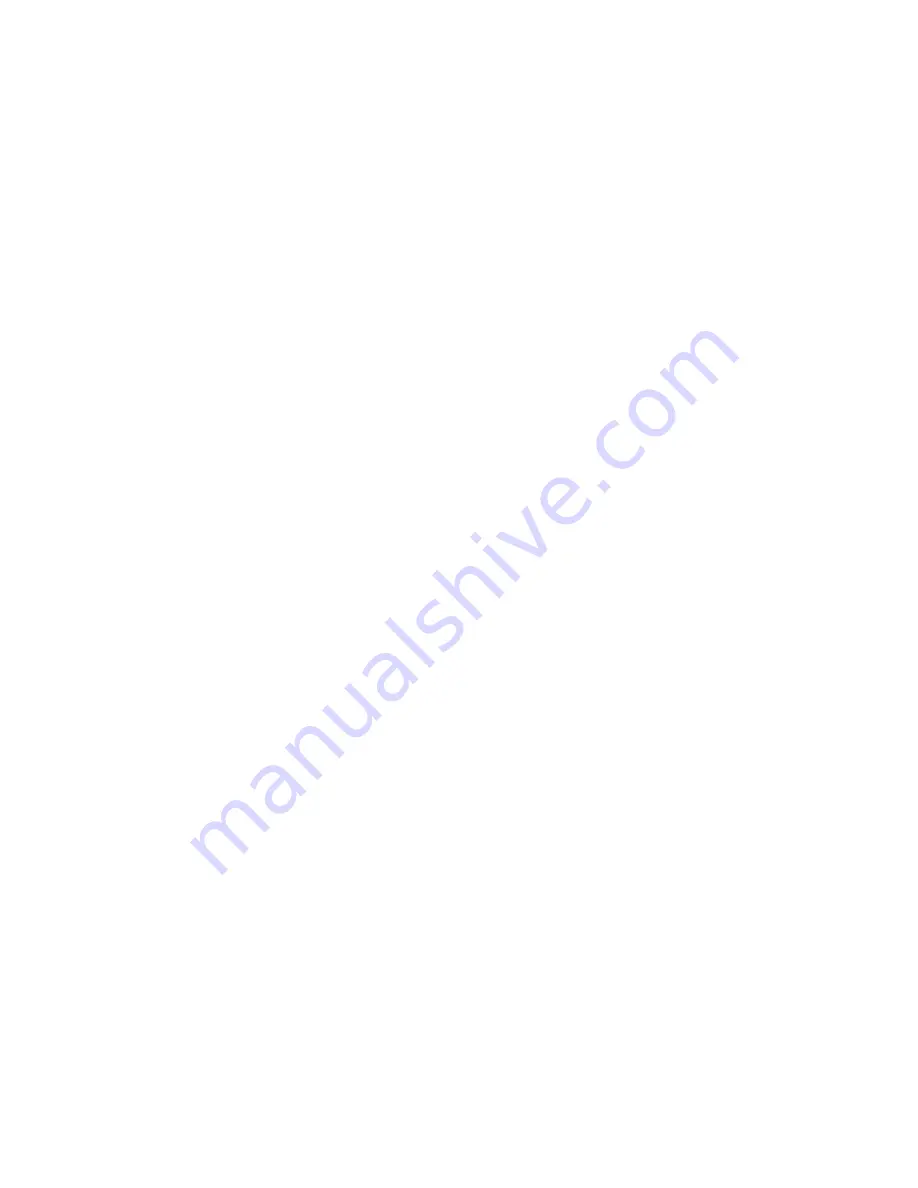
MPH COLUMBIA BOILER COMPANY
20
A Warrick 26C1D1C
“Probe” type LWCO is used only as a Secondary low water cut-off device.
Its primary function is to protect the boiler against low water situations where the primary LWCO
fails to break the control circuit. The probe mounts in the top head of the boiler and has a rod
length lower than that of the primary LWCO. This relay must be manually reset if power is inter-
rupted to the control circuit for any reason. During operation, if the water level falls below the
probe rod, the energized circuit breaks, causing the relay to open, disconnecting power to the
burner. Restore the water level to the normal operating level, then manually reset the control to
resume operation.
For additional information on the appropriate Low Water Cut-Off, see the LWCO cut sheets fol-
lowing this booklet.
Safety Valve
Safety valves shall be piped so that any discharge cannot cause injury to people or damage to
property. The discharge piping must be supported so that the weight of the piping is not trans-
mitted to the safety valve body. The weight supported by the valve outlet should not exceed that
of a drip pan elbow. Installations requiring long discharge piping should not be connected direct-
ly to the safety valve. Refer to Drawing PL-049 in the Appendix.
Always maintain a proper operating gap between the set pressure of the safety valve and the
maximum operating pressure of the boiler.
If the valve discharges on its own, contact a qualified service technician to determine the cause.
This may be an indication of equipment or system malfunction.