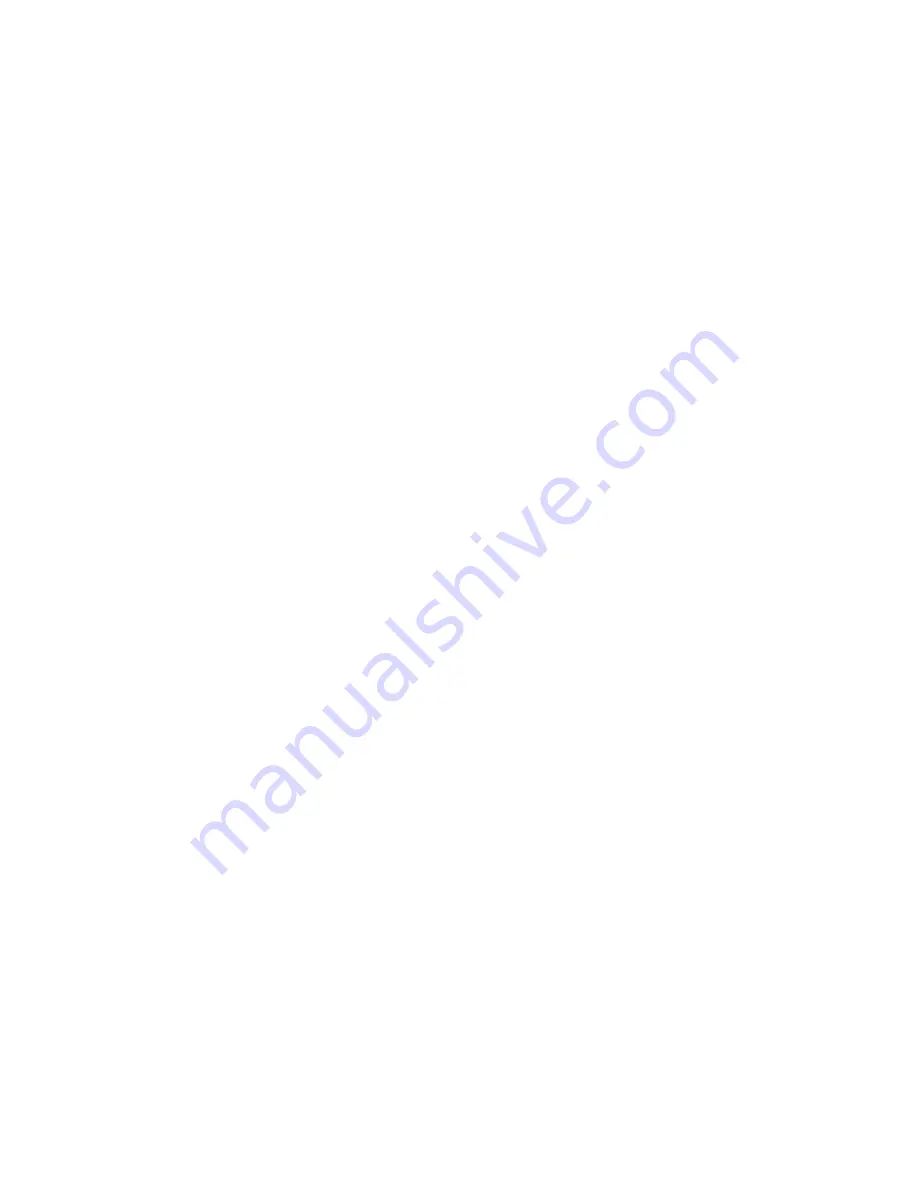
40
INITIAL START UP AND OPERATING SEQUENCE
1. Check secondary air settings as described in section #3 on page 41. Place the 3-position toggle switch on
the Burner to “OFF.” Energize the boiler circuit with electricity. The amber and red lights on the slide gun
will come on. Flip the 3-position toggle switch on the Burner to “PRIME.” The pump will start. Open the
bleed valve on the pump to relieve air, have a shop towel ready, after a few minutes there will be oil and air
sputtering from the bleeder. Close the bleeder when oil runs free of air. Oil will now start filling the line
to the burner.
2. Since the oil line is not attached to the burner yet have a bucket ready to catch oil, but be patient. It may
take 5-10 minutes to prime the pump and get oil to the burner. Minimize wear on pump and time involved
by filling oil lines and filters with oil before running pump.
3. Once the line is filled you will start catching the contaminated oil at the burner in your bucket. When the
oil is free of air and debris run another few gallons more and close the purge valve or connect the oil line to
burner. Flip the 3-position toggle switch on the Burner to “RUN.”
4.
By now the red light indicating preheating of the oil may have gone off. If it has, turn the operating
aquastat to a setting higher than boiler water temperature. The burner will start.
5. The fuel pump starts and the air solenoid valve opens to allow air into the air tank and air proving switch.
When air pressure of 20 psi is achieved in the tank, the air proving switch closes providing power to burner
motor and oil solenoid valve. The burner will attempt to fire and the green light comes on indicating the
burner is firing.
6. Adjust B-5 burner oil pressure to 2-5 psi or B-10 burner 3-7 psi oil pressure. Fine tune pressure setting
based on the instructions on the following page.
7. Adjust air pressure regulator on burner to approximately 12-14 psi on a B-5 single nozzle burner and 15-17
psi on a B-10 dual nozzle burner. The preheated oil and air are mixed at the nozzle and the fuel is
atomized as the electrodes arc for ignition. The red light will cycle on/off to automatically maintain air/oil
temperature.
8. Adjust oil flow for proper flame size. Gauge pressure is only an indicator; used oil will have a nozzle
pressure that depends on oil type and temperature. Look at fire and adjust if needed. A proper flame size
should extend 3/4 of the way into the boiler fire chamber. When oil pressure is set, tighten the locking nut
at the base of the adjustment screw.
9. If a consistent flame is not established during the initial 30 seconds the primary control will reset and wait
approximately 45-60 seconds before attempting restart. DO NOT try to service the burner or electrodes w/o
disconnecting the power. The burner will lock out if the cad cell does not detect any flame initially, a
consistent flame after 30 seconds, or after retrying 3 times. To force an ignition after lock out, wait 45
seconds, hold the red reset down for 5 seconds and release. DO NOT attempt to restart the control until the
boiler has time to cool down and any unburned oil mist has exited the chamber. Forcing a quick restart can
put hot oil on the hot surfaces of the heat exchanger and may cause an explosion or fire hazard.
10. When the aquastat is satisfied, the power to the ignition system will be interrupted thus causing the burner
to shut down. However, the burner block heaters will continue to cycle and the burner lights will remain on.
The heater light will cycle with the heating element.
Содержание L-24
Страница 2: ......
Страница 12: ...11 Brick Lining Location In WL 60 ...
Страница 14: ...13 ...
Страница 15: ...14 ...
Страница 16: ...15 ...
Страница 17: ...16 ...
Страница 18: ...17 Notes ...
Страница 19: ...18 ...
Страница 20: ...19 PRESSURE GAUGE AQUASTATS LWC SENSOR ELEC BOX ...
Страница 34: ...33 ...
Страница 36: ...35 ...
Страница 37: ...36 ...
Страница 38: ...37 ...
Страница 39: ...38 B10 DUAL NOZZLE BURNER INTERNAL WIRING ...
Страница 40: ...39 ...
Страница 46: ...45 ...
Страница 48: ...47 ...
Страница 49: ...48 ...
Страница 53: ...52 ...
Страница 58: ...57 Notes ...
Страница 59: ......
Страница 60: ...CC 6532 01 08 250 ...