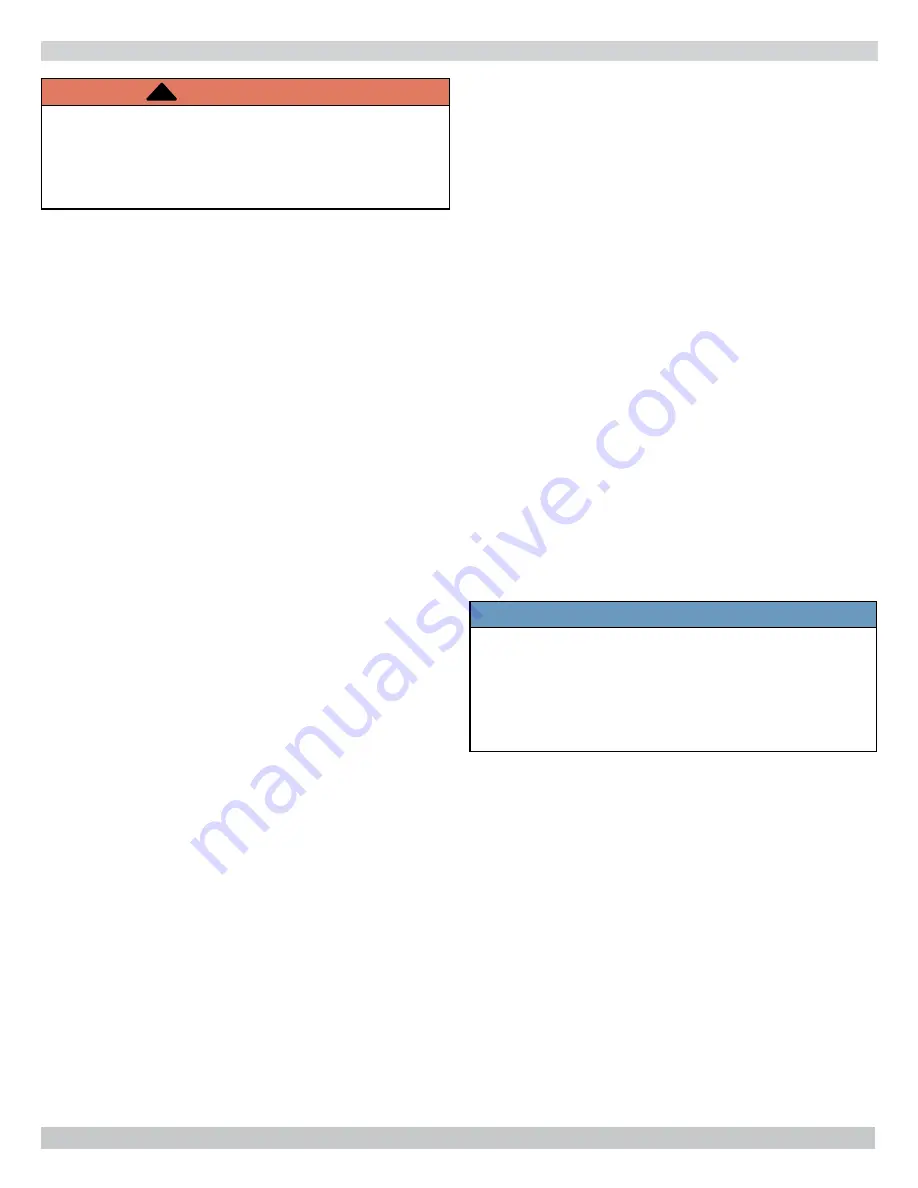
12
CHIMNEY AND VENT PIPE CONNECTION
WARNING
Installing or venting a boiler or any other gas
appliance with improper methods or materials could
result in death or serious injury due to
fi
re or to
asphyxiation from poisonous gases such as carbon
monoxide which is odorless and invisible.
!
Boiler and venting installations shall be performed
in accordance with "Venting of Equipment", of the
National Fuel Gas Code, ANSI Z223.1/NFPA 54, or
applicable provisions of the local building codes.
Chimney Inspection
Chimney must be clean, right size, properly constructed
and in good condition.
Installation must conform to requirements of the authority
having jurisdiction or, in absence of such requirements, to
the National Fuel Gas Code, ANSI Z223.1/NFPA 54. See
Figure 8, page 13
Connecting Vent Damper and Vent Connector
Vent or vent connector shall be Type B or metal pipe
having resistance to heat and corrosion not less than that
of galvanized sheet steel not less than No. 26 gauge. See
Table 1 for size of vent (
fl
ue opening).
1.
Position furnished vent damper on top of
fl
ue outlet
collar. Fasten damper securely to
fl
ue outlet collar with
sheet metal screws.
• Verify 1/2 square inch (approximately 3/4" diameter)
hole in damper blade is plugged using plug supplied
with vent damper.
• Verify damper blade has clearance to operate inside
of diverter.
• Do not modify draft diverter or vent damper.
2.
Install vent damper to service only single boiler for
which it is intended.
• Damper position indicator shall be in visible location
following installation.
• Locate damper so it is accessible for servicing.
Optional -
damper may be installed in horizontal or
vertical position as close to
fl
ue outlet as possible.
• Horizontal installations. See Figure 9, page 14.
• Alternate installations
see steps below. See Figure 10
page 14.
A. Do not install vent damper on vent pipe curve.
B. Do not run wires near high temperature surfaces.
Use stand-off brackets
if necessary.
3.
Damper must be in open position when appliance main
burners are operating.
4.
Boiler is equipped with factory wired harness that plugs
into vent damper. Connect thermostat to orange and
white wires marked 24 volt thermostat on boiler.
5.
Vent pipe must be same size as
fl
ue outlet collar.
6.
Slope pipe up from boiler to chimney not less than 1/4”
per foot.
7.
Run pipe as directly as possible with as few elbows as
possible.
8.
Do not connect to
fi
replace
fl
ue.
9.
End of vent pipe must be
fl
ush with inside face of
chimney
fl
ue.
10.
Horizontal run should not be longer than 3/4 the
chimney height (HT).
See Figure 8 page 13.
Vent Pipe
• Fasten sections of vent pipe with 3 sheet metal screws
at each joint to make piping rigid.
• Support horizontal portions of vent system to prevent
sagging.
• Use stovepipe wires or metal strapping every 5’ to
support pipe from above.
• Vent pipe through crawl space, use double wall vent
pipe.
• Vent pipe passing through combustible wall or partition,
use ventilated metal thimble. Thimble should be 4"
larger in diameter than vent pipe.
NOTICE
Minimum Vent Pipe Clearance - Wood and other
combustible materials must not be closer than 6”
from any surface of single wall metal vent pipe.
Listed Type B vent pipe or other listed venting
systems shall be installed in accordance with their
listing.
Removing Existing Boiler from Common Venting
System
When an existing boiler is removed from a common
venting system, the common venting system is likely to be
too large for proper venting of the appliances remaining
connected to it.
At the time of removal of an existing boiler, the following
steps shall be followed with each appliance remaining
connected to the common venting system placed in
operation, while the other appliances remaining connected
to the common venting system are not in operation.
1.
Seal any unused openings in the common venting
system.
2.
Visually inspect the venting system for proper size and
horizontal pitch and determine there is no blockage or
restriction, leakage, corrosion and other de
fi
ciencies
which could cause an unsafe condition.