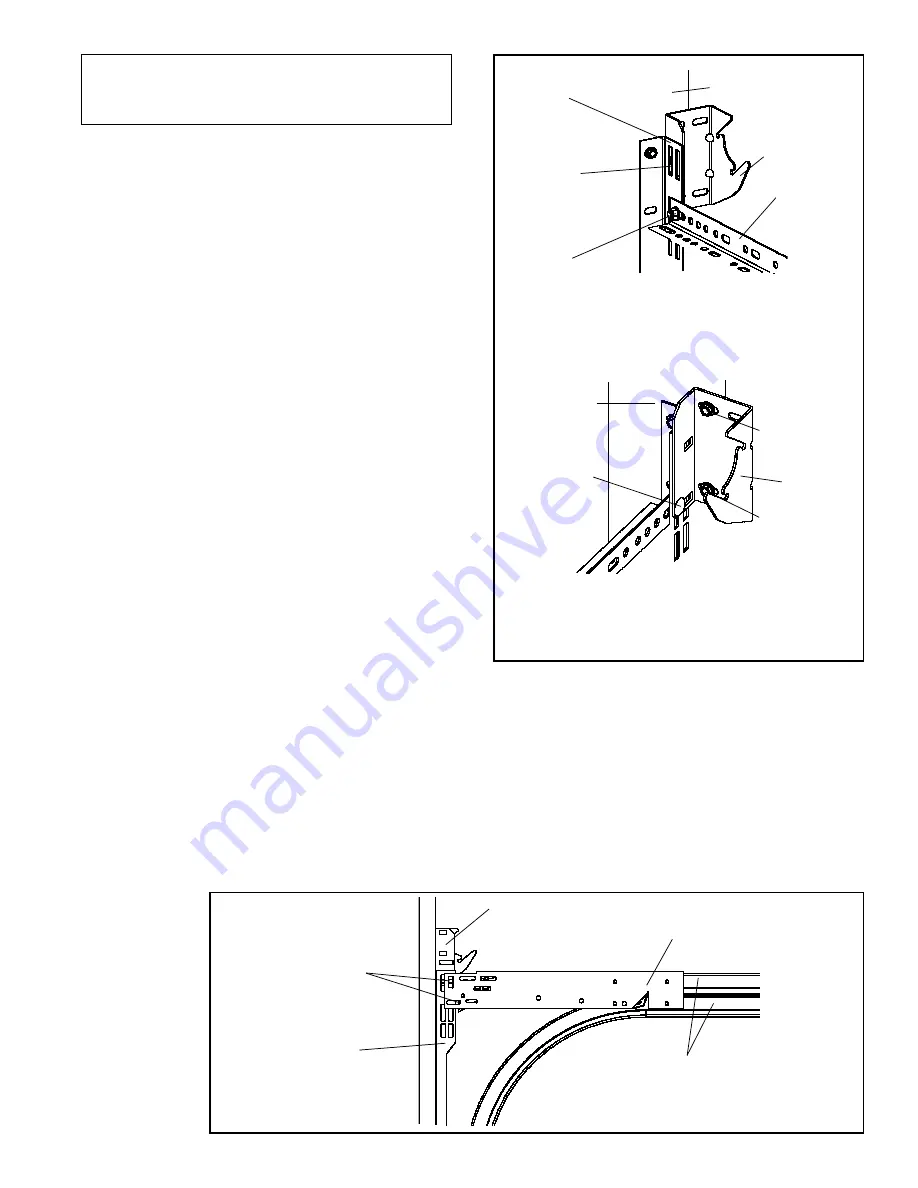
3
Installing The EZ-SET
®
Torsion Spring System
Step 1
Attach the bracket to the flag bracket and the
horizontal angle with a
3
/
8
"-16 x
3
/
4
" carriage bolt
and
3
/
8
" flange nut. (FIG. 1, VIEW A) Be sure to
orient the carriage bolt and flange nut as shown in
Figure 1, Views A and B. Remove and reattach the
existing
3
/
8
"-16 carriage bolt as required. The bracket
should be up against the jamb and the flag bracket.
If your door is " thick the carriage bolt should be
fastened through the slot in the flag bracket furthest
from the jamb. If your door is 1
3
/
8
" thick the carriage
bolt should be fastened in the slot closest to the
jamb. If you have double track low headroom, see
Figure for carriage bolt mounting locations. Do
this for both the left and right sides.
NOTE: Before installing
5
/
16
" lag screws, it is
important to drill
3
/
16
" pilot holes where the lag
screws are to be attached.
Use two
5
/
16
" x 1
5
/
8
" lag screws to connect the brack-
ets securely to the jamb or the header.
(FIG. 1, VIEW B) Install the lag screws in the
slots closest to the flag bracket if possible.
before proceeding to Step , make sure the
carriage bolt(s) and the lag screws are fastened
securely and the bracket is seated against the
jamb and the flag bracket. Do this for both the left
and right sides. Solid attachment is critical since
these brackets will be under strong spring tension.
NOTE: If your torsion tube is one full-length
piece skip to Step 3.
fig. 1
flag
Bracket
Jamb
Bracket
horizontal
Angle
VIEW A
2" ThICk dOOR (lEfT SIdE ShOWN)
12" RAdIUS TRACk, USING SlOTS 1 ANd 4
15” RAdIUS TRACk, USES TOP TWO SlOTS
VIEW B
2" ThICk dOOR (lEfT SIdE ShOWN)
12" RAdIUS TRACk, USING SlOT 1
Existing
3
/
8
" flange
Nut
3
/
8
" – 16 x
3
/
4
"
Carriage
Bolt
Bracket
lag Screw
Jamb
lag Screw
fig. 2
low headroom
Starter Angle
horizontal
Tracks
Bracket
Insert carriage bolts from
opposite side similar
to figure 1B
flag
Bracket
dOUBlE TRACk lOW hEAd ROOm
(lEfT SIdE ShOWN)
15" Radius
Track Slots
Содержание EZ-SET
Страница 12: ...12 2000 CBPC P N 0130555 Rev 11 6 04 ...