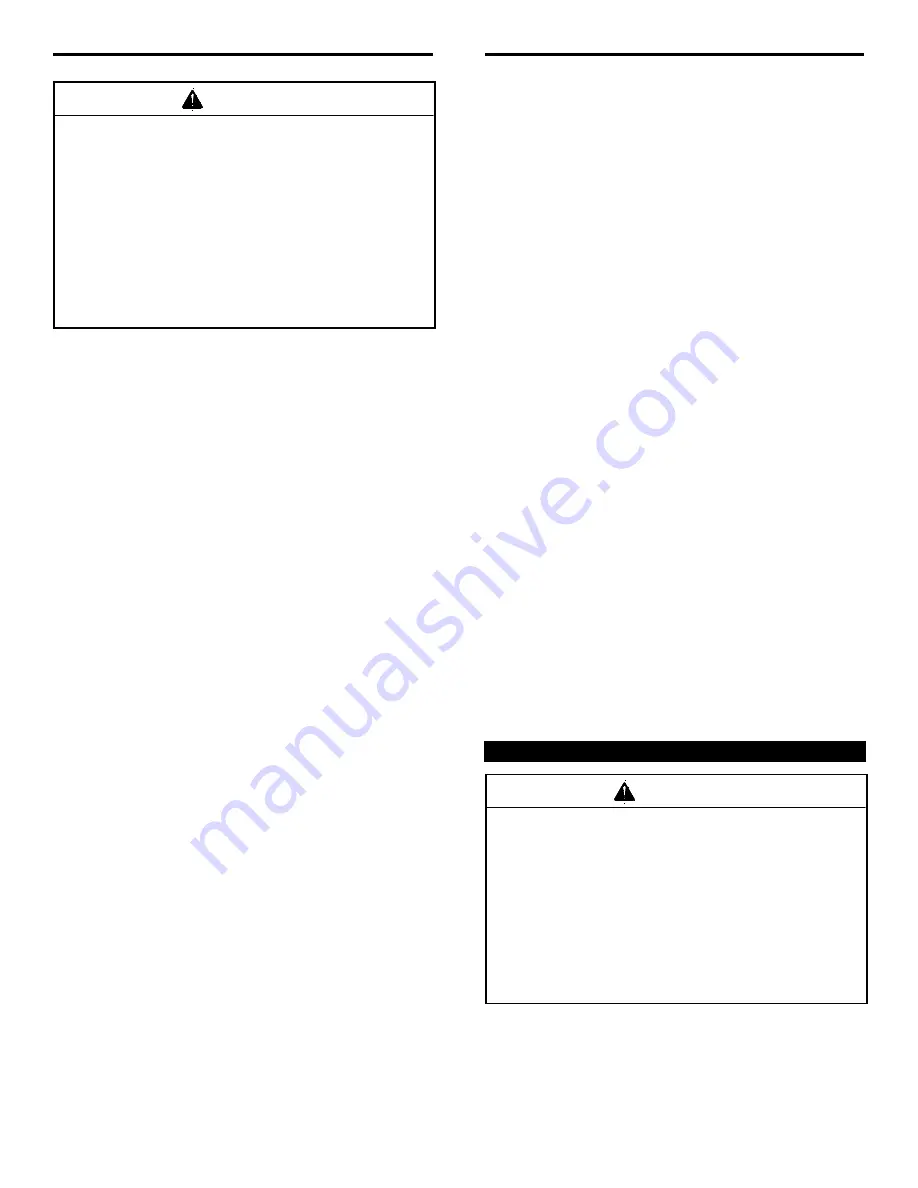
PREFACE
•
Read and follow ALL instructions before using
this equipment.
•
Failure to comply with ALL instructions can result
in serious injury or death.
•
In the event that the user, or any assistants of the
user of this equipment cannot read or cannot
completely understand the warnings and
information contained in these instructions, the
employer of the user and his assistants must
thoroughly educate and train them on the proper
operation and safety procedures of this
equipment.
NOTICE TO PURCHASERS AND USERS OF OUR
PRODUCTS AND THIS INFORMATIONAL MATERIAL
The products described in this material, and the information
relating to those products, is intended for knowledgeable,
experienced users of abrasive blasting equipment.
No representation is intended or made as to the suitability of
the products described herein for any particular purpose or
application. No representations are intended or made as to the
efficiency, production rate, or the useful life of the products
described herein. Any estimate regarding production rates or
production finishes are the responsibility of the user and must
be derived solely from the user’s experience and expertise,
and must not be based on information in this material.
The products described in this material may be combined by
the user in a variety of ways for purposes determined solely by
the user. No representations are intended or made as to the
suitability or engineering balance of the combination of
products determined by the user in his selection, nor as to the
compliance with regulations or standard practice of such
combinations of components or products.
Abrasive Blast Equipment is only a component of the range of
equipment used in an abrasive blasting job. Other products
may include an air compressor, abrasive, scaffolding, hydraulic
work platforms or booms, paint spray equipment,
dehumidification equipment, air filters and receivers, lights,
ventilation equipment, parts handling equipment, specialized
respirators, or equipment that while offered by Clemco may
have been supplied by others. Each manufacturer and supplier
of the other products used in the abrasive blasting job must be
contacted for information, training, instruction and warnings
with regard to the proper and safe use of their equipment in the
particular application for which the equipment is being used.
The information provided by Clemco is intended to provide
instruction only on Clemco products. All operators must be
trained in the proper, safe, use of this equipment. It is the
responsibility of the users to familiarize themselves with, and
comply with, all appropriate laws, regulations, and safe
practices that apply to the use of these products. Consult with
your employer about training programs and materials that are
available.
Our company is proud to provide a variety of products to the
abrasive blasting industry, and we have confidence that the
professionals in our industry will utilize their knowledge and
expertise in the safe efficient use of these products.
GENERAL INSTRUCTIONS
Described herein are some, BUT NOT ALL, of the major
requirements for safe and productive use of blast
machines, remote control systems, operator respirator
assemblies, and related accessories. Completely read ALL
instruction manuals prior to using equipment.
The user's work environment may include certain
HAZARDS related to the abrasive blasting operation.
Proper protection for the blaster, as well as anyone else
that may be EXPOSED to the hazards generated by the
blasting process, is the responsibility of the user and/or
the employer. Operators MUST consult with their employer
about what hazards may be present in the work
environment including, but not limited to, exposure to dust
that may contain TOXIC MATERIALS due to the presence
of silica, cyanide, arsenic or other toxins in the abrasive,
or materials present in the surface to be blasted such as
lead or heavy metals in coatings. The environment may
also include fumes that may be present from adjacent
coatings application, contaminated water, engine exhaust,
chemicals, and asbestos. The work area may include
PHYSICAL HAZARDS such as an uneven work surface,
poor visibility, excess noise, and electrical hazards. The
operator MUST consult with his employer on the
identification of potential hazards, and the appropriate
measures that MUST be taken to protect the blaster and
others that might be exposed to these hazards.
ALL machines, components and accessories MUST be
installed, tested, operated and maintained only by trained,
knowledgeable, experienced users.
DO NOT modify or substitute any Clemco parts with other
types or brands of equipment. Unauthorized modification
and parts substitution on supplied air respirators is a
violation of OSHA regulations and voids the NIOSH
approval.
OPERATIONAL INSTRUCTIONS
OPERATOR SAFETY EQUIPMENT
•
Blast operators and others working in the vicinity of
abrasive blasting must always wear properly-
maintained, NIOSH-approved, respiratory protection
appropriate for the job site hazards.
•
DO NOT USE abrasives containing more than one
percent crystalline (free) silica. Ref. NIOSH Alert
#92-102
•
Inhalation of toxic dust (crystalline silica, asbestos,
lead paint and other toxins) can lead to serious or
fatal disease (silicosis, asbestosis, lead or other
poisoning).
•
ALWAYS wear NIOSH-approved supplied-air respirators
as required by OSHA, in the presence of any dust including,
but not limited to, handling or loading abrasive; blasting or
working in the vicinity of blast jobs; and cleanup of expended
abrasive. Prior to removing respirator, an air monitoring
WARNING
WARNING
I