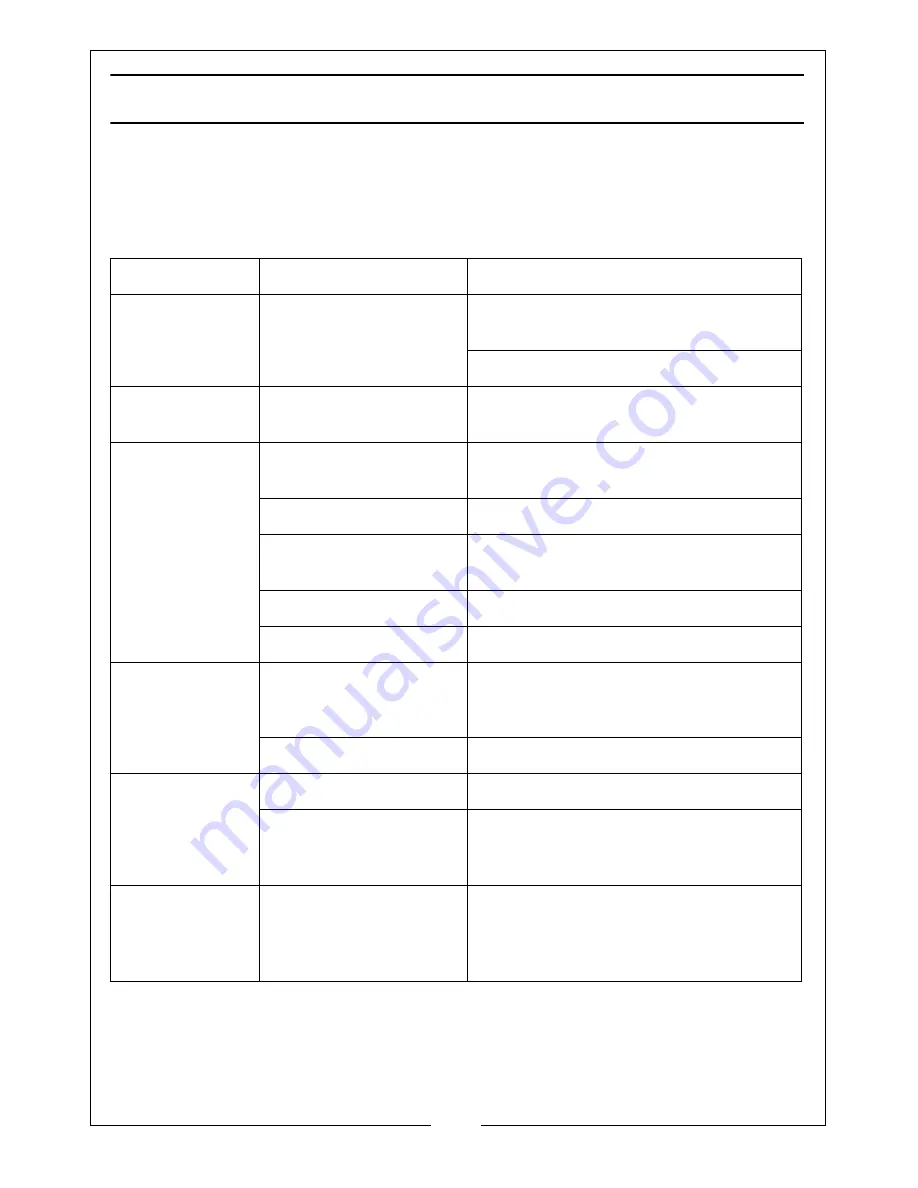
20
Parts & Service: 020 8988 7400 / E-mail: [email protected] or [email protected]
TROUBLESHOOTING
Your CLARKE MIG Welder has been designed to give long and trouble free
service. If, however, having followed the instructions in this booklet carefully,
you still encounter problems, the following points should help identify and
resolve them.
PROBLEM
CAUSE
SOLUTION
No response from
welder
Check fuses and mains
lead
Replace fuses as necessary, If problem
persists return welder to your local dealer
Check fuse size
Welder does not
feed wire
Feed motor has malfunc-
tioned.
Return welder to your local dealer
Feed motor run-
ning but no wire
being fed from
welder tip
Insufficient Feed Roller
pressure
Increase roller pressure
Burr on end of wire
Re-cut wire square with no burr
Liner blocked or dam-
aged
Clean with compressed air or replace
liner.
Inferior wire
Use only good “clean” wire
Roller worn out
Replace roller
Wire welds itself
to tip
Wire feed speed too low
Unscrew tip, cut wire and fit new tip
Increase wire speed before operating
again
Wrong size tip
Fit correct size tip
Wire feeds into
‘birds nest’ tan-
gle
Wire welded to tip
As above plus reduce feed roller pressure
Wire liner damaged pre-
venting smooth opera-
tion
Renew wire liner
Loose coils of
wire tangle
around wire drum
inside machine
Locking knob too slack
Tighten Locking Knob slightly. Do not
over-tighten
Содержание MIG102NG
Страница 24: ......