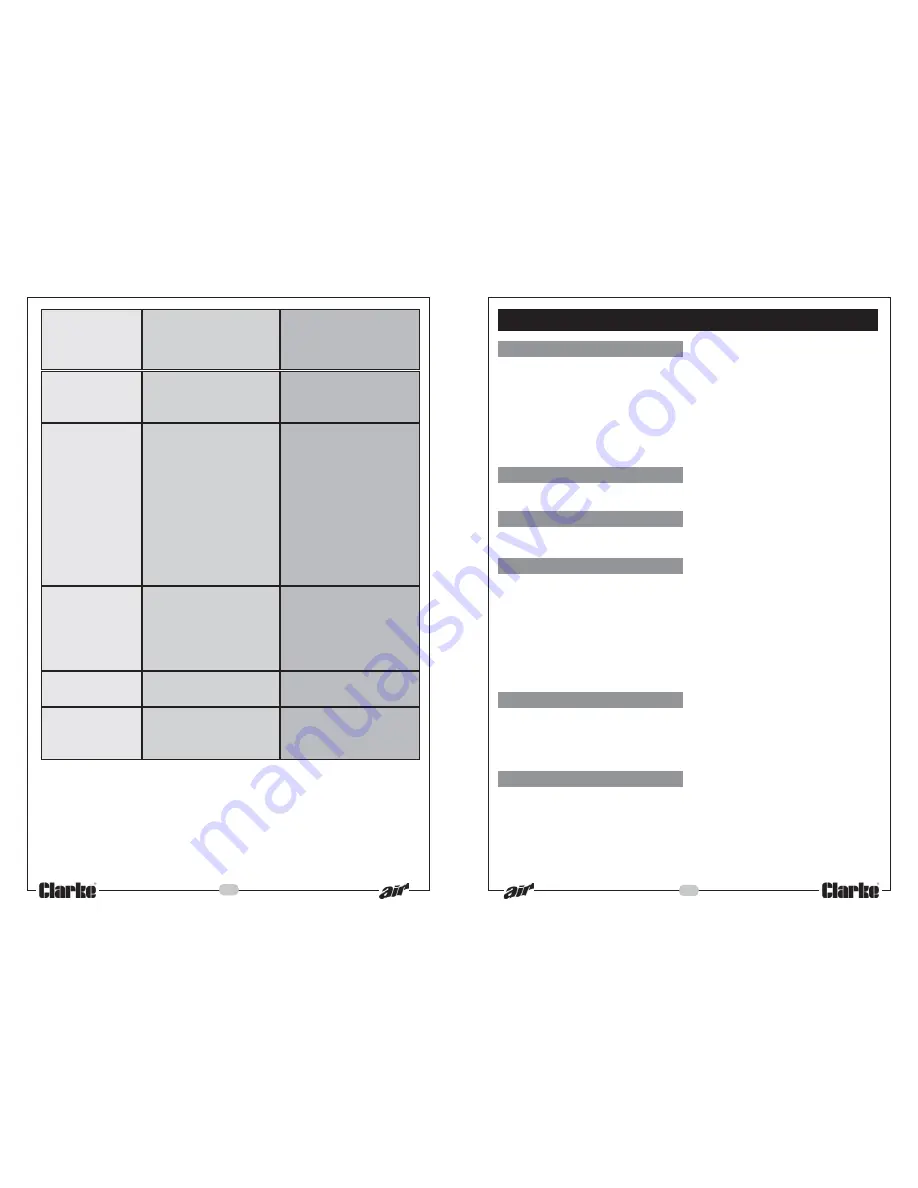
- 7 -
PREPARATION FOR USE
A.Environmental
•
Ensure the compressor is sited on a firm level surface.
•
Ensure the environment is dry and dust free.
•
Ensure there is adequate ventilation for:
a)
Air intake to compressor pump
b)
Cooling for compressor pump
c)
Engine exhaust gases.
B. Engine
Check oil and fuel levels and a visual check of components. Refer to engine service manual.
C. Pump
•
Check oil level on the Dipstick - to level marked.
D. Fueling
Fill with unleaded petrol, according to the instructions within the engine manual.
•
Ensure the fuel tap is set to the required position.
•
Ensure The fuel hose and connectors are intact, in perfectly servicable
condition and there is no leakage.
Note : Always use a funnel to fill the fuel tank so as to avoid accidental spillage of
fuel. If fuel is spilled it must be removed from the unit and surrounding area, before
attempting to start the engine.
E. Receiver
•
Drain off any condensate, by opening the drain cock (see Fig. 1). Remember
to close the cock when completed.
NOTE: This should be carried out DAILY when the compressor is in constant use.
F.
Air Hose & Air Tool
•
Attach the air hose to the outlet using an appropriate connector.
NOTE: Quick fit nuts are provided with model PP9ND
•
Attach the air tool/spray gun to the air hose...If using snap couplings, use
a whip end, available from your Clarke dealer.
z
- 14 -
Large amount of condensation in
air receiver.
Leaks in system
Compressor unit runs
on and off load more
frequently than usual.
Compressor unit runs
‘on load’ when no air is
being used.
Leaks in system.
Compressor’s oil
consumption rising.
Too much oil in compressor.
Cylinder worn.
Oil in the air delivered.
Oil level rises although
no oil has been put in.
Piping installation incorrect.
Compressor taking in air which is
too warm.
Condensation at outlet
points.
Drain off condensation Regularly
(Every day before use).
Locate leaks (by means of soapy
water) and repair.
Locate leaks (by means of
soapy water) and repair.
Intake air filter blocked.
Sump over full.
Leaks around crank case.
Working temperature of
compressor too high because of
insufficient cooling.
Cylinder worn.
Check oil level 2 or 3 minutes after
stopping.
Change seal and inspect
packing surfaces. Repair or
replace defective parts.
Increase ventilation to air
compressor.
Replace worn parts or send
compressor pump for an
overhaul.
Reduce oil to correct level.
Replace worn parts or send
compressor pump for an
overhaul.
Change air filter.
Compressor over dimensioned.
Intake air filter blocked.
Condensation in oil pump.
Consult your local dealer.
Obtain better fresh-air supply to
compressor.
Change air filter.