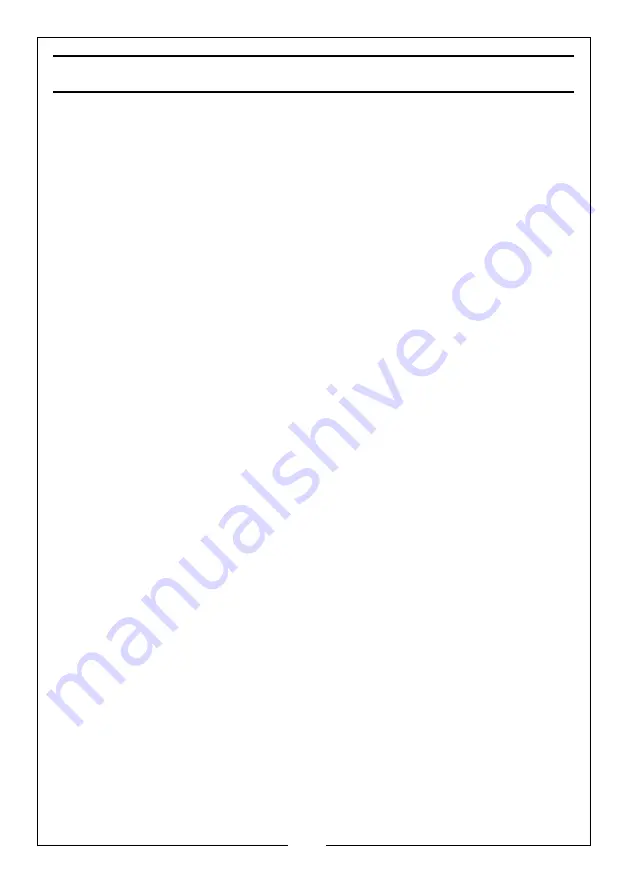
9
Parts & Service: 020 8988 7400 / E-mail: [email protected] or [email protected]
OPERATION
1. Open any valves in the pipeline.
2. If operating the pump for the first time, prime the pump as described. on
page 8.
NOTE: Refilling (re-priming) is only necessary if the pump has been
drained.
3. Connect to the power supply and switch on.
• When water starts to flow through the system check for leaks and
correct as necessary.
• If the motor fails to start or the pump does not deliver water, refer to
TROUBLESHOOTING.
• Never operate the pump when not primed with water or if the inlet is
blocked which would allow the pump to run dry, causing damage.
NOTE: Filling the suction pipe with water will speed up the priming
process, and it is essential that a non-return valve be fitted to the
end of the suction pipe.
4. Stop the pump by switching off the power supply.
CARE DURING USE
1. Do not allow the pump to run dry, otherwise the seal between the pump
and motor may be damaged. If a leak occurs at this point, allowing water
to pass from the pump to the motor, take the pump to your Clarke dealer
for overhaul.
2. In the event of a blockage, where debris has entered the pump, it can be
cleaned out as described under MAINTENANCE.
3. DO NOT USE for pumping chemicals or other corrosive liquids. Should
contaminants enter the pump, flush through with water as soon as possible
to prevent damage.
4. If the pump is being used to drain a pool, ensure there is adequate
drainage and there is no risk of damage to property as a result of water
being discharged. If a flexible hose must be laid across a roadway, protect
it with wooden planking.
Содержание 7120400
Страница 16: ......