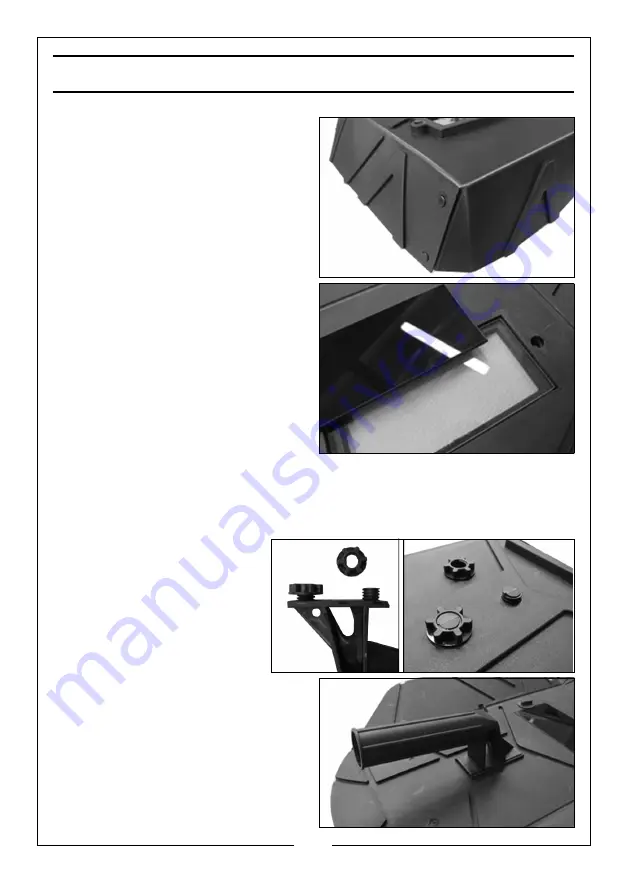
14
Parts & Service: 020 8988 7400 / E-mail: [email protected] or [email protected]
ASSEMBLING THE WELDING SHIELD
1. The welding shield shown on
page 12 is supplied flat for
shipping. Fold the sides of the
shield around and clip to the top
panel.
2. Insert both the glass lens panels
into the recess inside the shield.
• The clear glass must be fitted
first to face the outside.
3. Insert the two plastic screws and
use the plastic wingnuts to clamp
the glass panels to the shield.
•
The clear glass panel should be
replaced when it becomes badly
pitted.
4. When replacing the glass panels, only use parts supplied by Clarke
International. The dark panel is a certified, optical glass and should not be
exchanged for any other type.
5. Secure the handle in
position using the plastic
nuts provided.
•
The handle will be on the
inside of the shield.
Содержание 6015200
Страница 32: ......