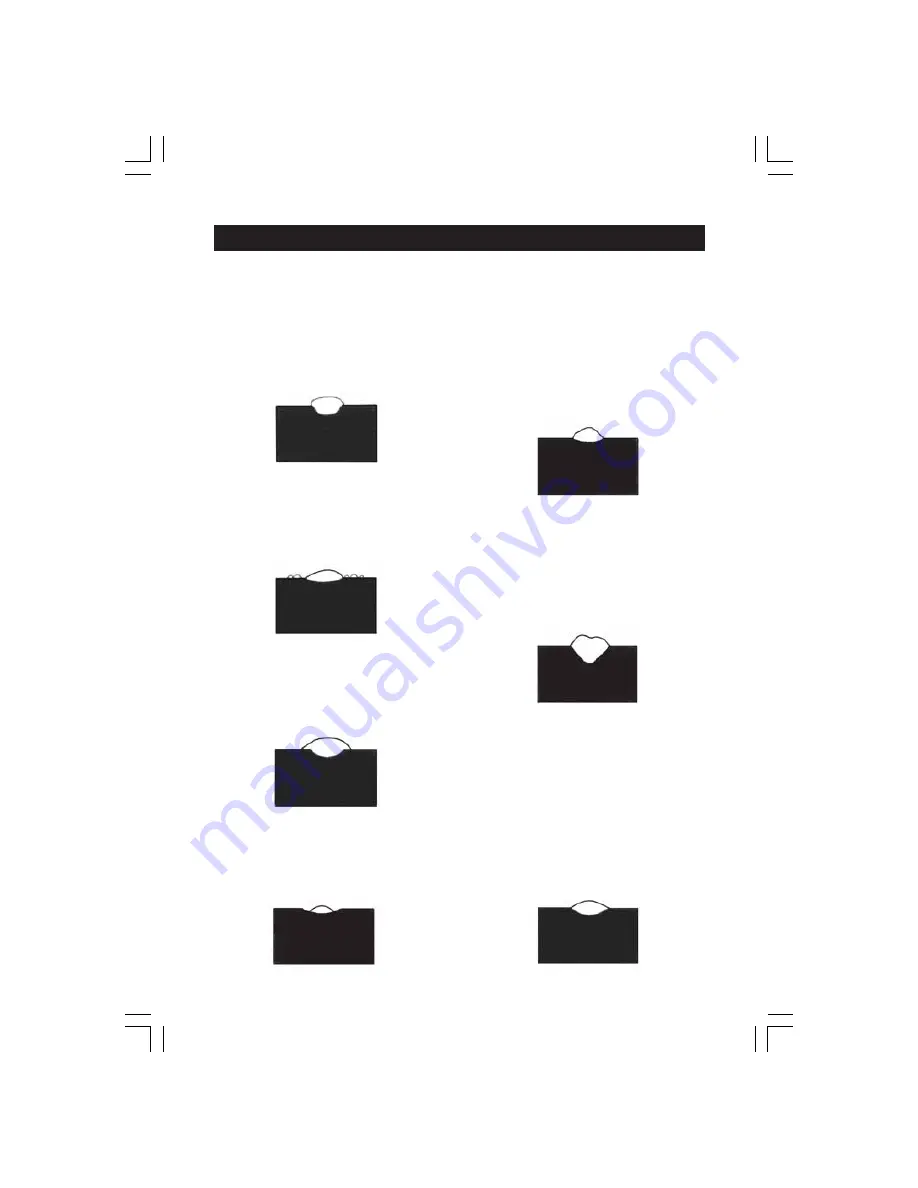
18
WELDING PITFALLS
The arc welding technique is an acquired skill and requires considerable practice
before perfect results are obtained. The diagrams below will help to explain the
pitfalls in your technique and how to overcome them.
1. Arc too short
This causes irregular masses of weld to
be deposited, with slag contamination
on an uneven surface.
2. Arc too long
This causes poor penetration resulting in
a weak weld with excessive spatter and
porosity. Surface of the weld is rough
and the arc makes a hissing sound
3. Electrode moved too slowly
This causes a very wide and heavy
deposit which overlaps at the sides. It is
wasteful both in terms of time and
electrode use.
4. Electrode moved too quickly
T
his causes poor penetration with a
‘stringy’ and incomplete weld deposit. Slag
is very hard to remove.
5. Current too low
This causes poor penetration and
causes the electrode to stick to the
workpiece too readily. Also results in a
very irregular and high weld deposit.
Slag is very hard to remove.
6. Current too high
This causes excessive penetration with
spatter and deep pointed crater. It may
also cause holes to be burned in the
workpiece.
Burns electrodes very quickly.
7. The perfect weld
With the correct combination of arc
length, current regulation, inclination
and speed of the electrode, you will,
with practice produce the per fect
weld.
This should be regular with uniform
ripples and no slag contamination.
The arc will make a steady, even
crackling sound.
Содержание 230TE
Страница 1: ...OPERATING MAINTENANCE INSTRUCTIONS ARC WELDERS 0807 ARC WELDERS ...
Страница 19: ...20 ...