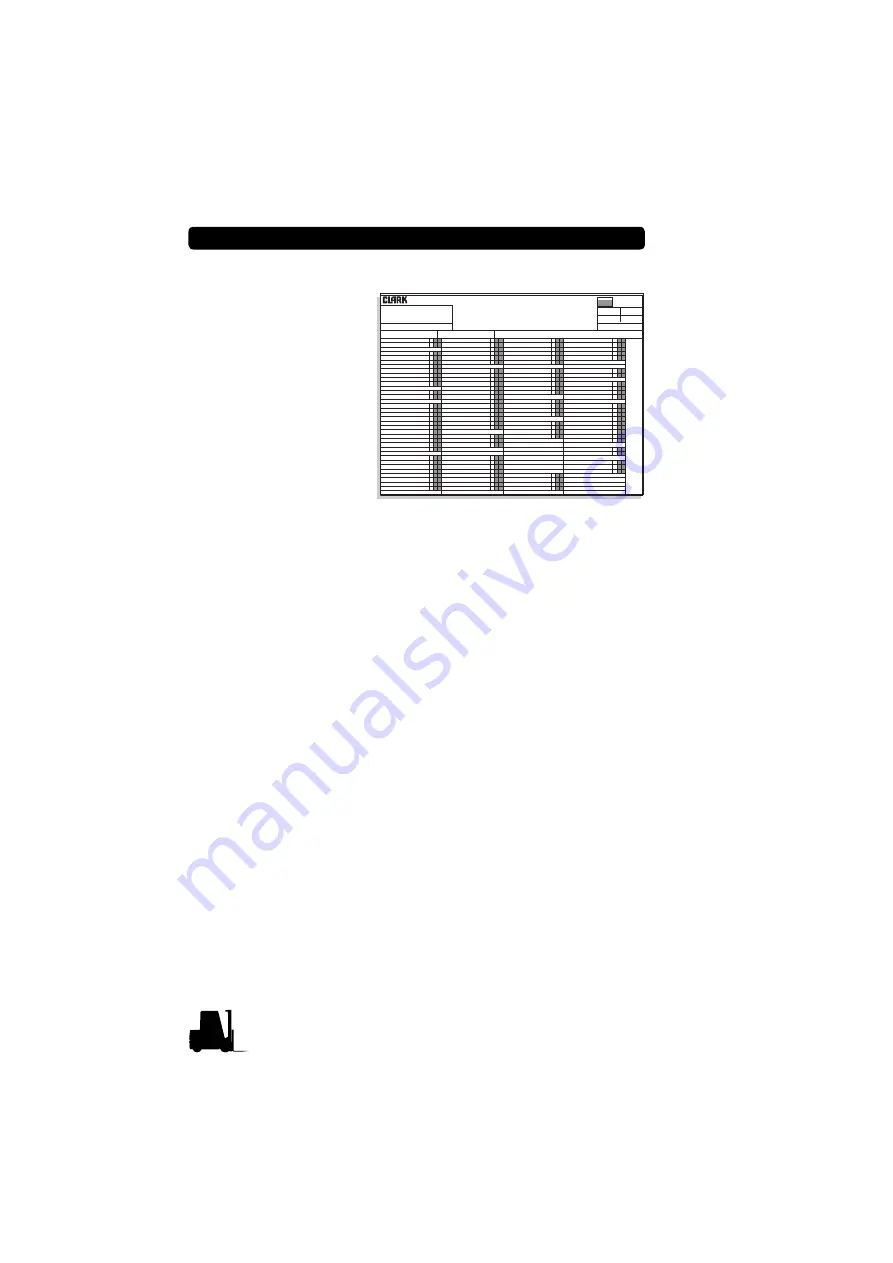
8-10
Lift truck Maintenance
PM Report Form
A planned maintenance
(PM) program of regular,
routine inspections and
lubrication is important for
long life and troublefree
operation of your lift truck.
Make and keep records of
your inspections.
Use these records to help
establish the correct PM
intervals for your appli-
cation and to indicate
maintenance required to
prevent major problems
from occurring during operation.
As an aid in performing and documenting your PM inspections,
CLARK prepared an
Electric Truck Planned Maintenance Report
Form
(PM Report Form). Copies of this form may be obtained from
your authorized CLARK dealer. We recommend that you use this
form as a checklist and a record of your inspection and truck
condition.
The maintenance procedures outlined in this manual are intended to
be used in conjunction with the PM Report Form. They are arranged
in groupings of maintenance work that are done in a logical and
efficient sequence.
You make check marks or entries on the PM Report Form when you
perform the PM. Please notice on the form a special coding system
for indicating the importance of needed repairs and/or adjustments.
When you have finished the PM inspections, be sure to give a copy
of the report to the designated authority responsible for lift truck
maintenance.
Do not make repairs or adjustments unless authorized to do so.
For safety, it is good practice to:
• Remove all jewelry (watch, rings, bracelets, etc.) before work-
ing on the truck.
• Disconnect the battery before working on electrical compo-
nents.
• Always wear safety glasses. Wear a safety (hard) hat in indus-
trial plants and in special work areas where protection is neces-
sary and required.
ELECTRIC TRUCK
PLANNED MAINTENACE REPORT
CUSTOMER
MODEL & SERIAL NO.
ATTACHMENT NO.
AUTHORIZED SIGNATURE
A. TEST DRIVE MACHINE
16 MOTORS
23 BRAKE SYSTEM
26 STEER AXLE
26 STEERING SYSTEM
34 UPRIGHT - CARRIAGE
34 LOAD BACK REST
35 LIFT LINKAGE (POW)
38 SHEET METAL & CWT
39 OVERHEAD GUARD
53 ATTACHMENTS
29/30 HYDRAULIC SYSTEM
32 TILT CYLINDER
19 ELECTRICAL TESTS
20 DRIVE AXLE
23 WHEELS AND TIRES
01. CLEANING & LUBRICATION
12. BATTERY AND CABLES
13. GAUGES -LIGHTS-INDICATORS
a. Drive Train Noise
b. Steering Operation
c. Service Brake Operation
a. Drive Train Noise
Steering Operation
Steering Operation
c. Service Brake Operation
c. Service Brake Operation
d. Speed Control
a. Drive Train Noise
b. Steering Operation
c. Service Brake Operation
d. Speed Control
e. Drive Train Noise
f. Steering Operation
g. Service Brake Operation
h. Speed Control
i. Drive Train Noise
j. Steering Operation
k. Service Brake Operation
a. Drive Train Noise
b. Steering Operation
c. Service Brake Operation
d. Drive Train Noise
e. Steering Operation
f. Service Brake Operation
g. Drive Train Noise
h. Steering Operation
e. Plugging & Direction Control
f. Return to Neutral
g. Hydraulic System Operation
e. Plugging & Direction Control
a. Drive Train Noise
b. Steering Operation
c. Service Brake Operation
a. Drive Train Noise
b. Steering Operation
c. Service Brake Operation
d. Speed Control
e. Plugging & Direction Control
f. Return to Neutral
f. Return to Neutral
g. Hydraulic System Operation
a. Drive Train Noise
b. Steering Operation
c. Service Brake Operation
d. Speed Control
e. Plugging & Direction Control
a. Drive Train Noise
b. Steering Operation
c. Service Brake Operation
d. Speed Control
b. Steering Operation
c. Service Brake Operation
a. Drive Train Noise
b. Steering Operation
c. Service Brake Operation
a. Drive Train Noise
b. Steering Operation
c. Service Brake Operation
d. Speed Control
e. Plugging & Direction Control
a. Drive Train Noise
b. Steering Operation
c. Service Brake Operation
d. Speed Control
e. Plugging & Direction Control
f. Return to Neutral
g. Hydraulic System Operation
h. Plugging & Direction Control
a. Security of Mounting
b. Roller Condition/Clearance
e. Chain Adjustment
g. Latch and Stop Condition
a. Conditon
a. Check for Leakage
b. Fluid Level - Condition
c. Clean/Replace Breather
d. Replace Filter
a. Check for Leakage
b. Cylinder Rod Condidtion
a. Check for Leakage
b. Cylinder Rod Condidtion
c. Mounting Security/Torque
a. Check for Leakage
b. Cylinder Rod Condidtion
c. Mounting Security/Torque
d. Tilt Cylinder Adjustment (Racking)
e. Linkage Adjustment
f. Hose Condition
g. Lift Speed (in/Sec)
h. Drift Test (in/mIn)
Full Load
Lift Cylinder
Tilt Cylinder
a. Check for Leakage
b. Fluid Level - Condition
c. Clean/Replace Breather
d. Replace Filter
e. Linkage Adjustment
f. Hose Condition
g. Lift Speed (in/Sec)
h. Drift Test (in/mIn)
Full Load
e. Plugging & Direction Control
a. Air Clean Truck
b. Air Clean Electrical Truck
Air Clean Truck
Air Clean Electrical Truck
Creep Speed
1A Operation
Creep Speed
1A Operation
INSPECTOR
SPECIAL INSTRUCTIONS
DATE
DATE LUST P.M.
HOUR METER
HRS. LAST P.M.
CUST. P.O. NO.
/ = O.K
x = Adjust (Not P.M.)
r = Repair or replace
s = Requires shop year
C
O
D
E
COMMENTS
O.K.
POTENTIAL
URGENT
Содержание GEX 40
Страница 2: ......
Страница 6: ...iv...
Страница 16: ...1 4 Seat Belts Seat Belts ALWAYS BUCKLE UP Seat beltscan reduce injuries...
Страница 17: ...Section 1 General Safety Rules No Riders 1 5 No Riders...
Страница 37: ...Section 3 Common Truck Contents 3 1 Common Truck Contents Truck Description 3 2 Operator Controls 3 3...
Страница 46: ...3 10...
Страница 78: ...6 6...
Страница 79: ...Section 7 Emergency Towing Contents 7 1 Emergency Towing Contents Towing Precautions 7 2 Towing Procedures 7 3...
Страница 83: ...Section 8 Planned Maintenance Contents 8 1 Planned Maintenance Contents Lift truck Maintenance 8 2...
Страница 111: ...Section 9 Specifications Contents 9 1 Specifications Contents GEX40 50 9 2...
Страница 114: ...9 4...
Страница 117: ......
Страница 118: ......
Страница 119: ......