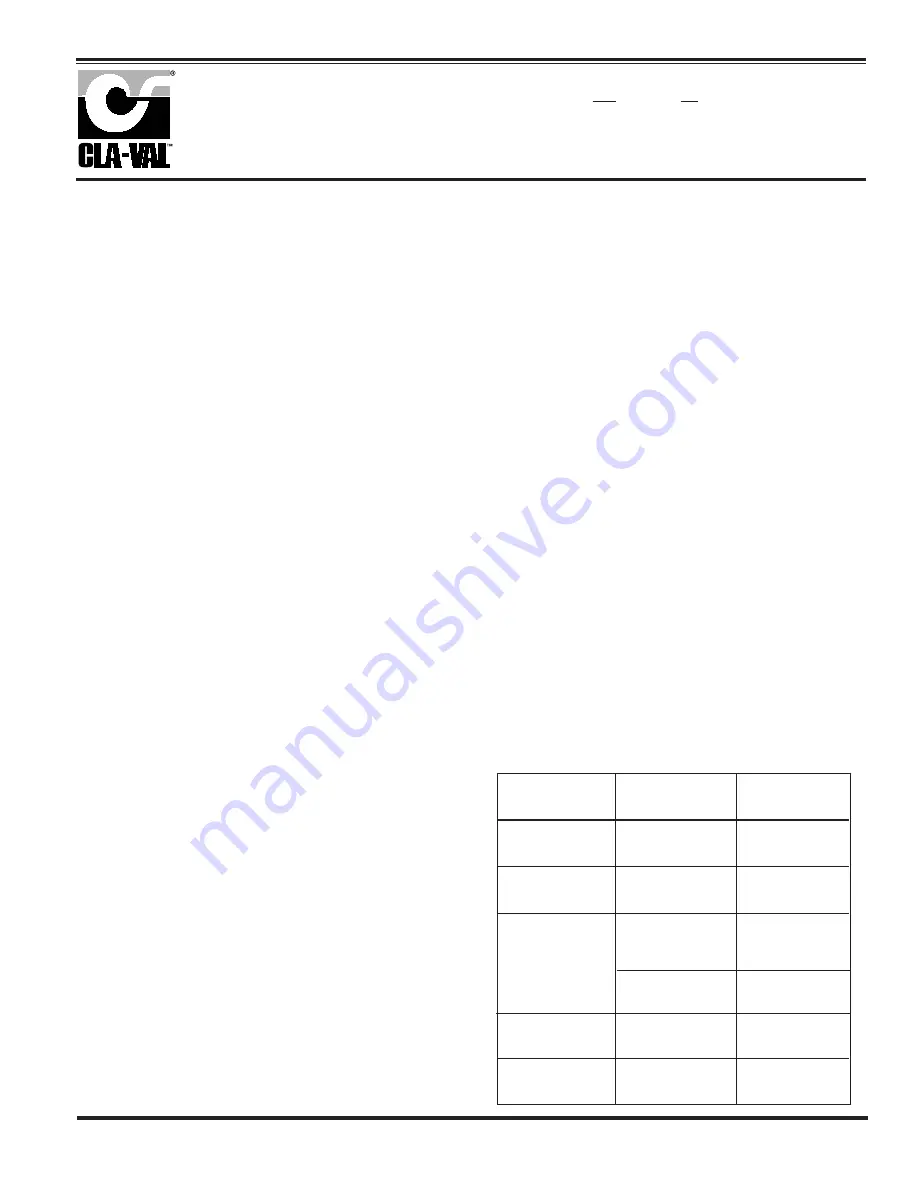
PRESSURE RELIEF CONTROL
CRL5A
MODEL
INSTALLATION / OPERATION / MAINTENANCE
CLA
-
VAL
Copyright Cla-Val 2011 Printed in USA Specifications subject to change without notice.
P.O. Box 1325
•
Newport Beach, CA 92659-0325
•
Phone: 949-722-4800
•
Fax: 949-548-5441
•
E-mail: [email protected]
•
Website cla-val.com
©
N-CRL5A (R-3/2011)
DESCRIPTION
The CRL5A Pressure Relief Control is a direct-acting, spring-loaded, di-
aphragm-type relief valve. It may be used as a self-contained valve or as a
pilot control for Cla-Val valves. It opens and closes within very close pres-
sure limits.
INSTALLATION
The CRL5A Pressure Relief Control may be installed in any position.
CRL5A body (7) has one inlet and one outlet ports with two smaller side
ports. Side ports are for control connections or gauge installation. A flow
direction indicator is cast into body. Control pressure sensing is through
small side port in powerunit (6).
OPERATION
The CRL5A Pressure Relief Control is normally held closed by compres-
sion spring force above diaphragm, and controlling pressure is applied
under diaphragm. When controlling pressure exceeds spring setting, con-
trol disc is lifted off its seat permitting flow through the control. When con-
trolling pressure drops below spring setting, spring returns control to
normally closed position.
ADJUSTMENT PROCEDURE
The CRL5A Pressure Relief Control can be adjusted to provide relief set-
ting at any pressure within the range found on nameplate. Provision
should be made for pressure gauge at CRL5A sensing point.
Pressure adjustment is made by first loosening jam nut (10) and turning
adjustment screw (9) to vary spring pressure on diaphragm. Turning ad-
justment screw clockwise increases pressure required to open control.
Counterclockwise decreases pressure required to open control.
When pressure adjustments are complete tighten jam nut (10) and replace
protective cap (1). If there is a problem of tampering, lock wire holes are
provided in cap and cover. Wire cap to cover and secure with lead seal.
DISASSEMBLY
The CRL5A Pressure Relief Control does not need to be removed from
pipeline for disassembly and service. Make sure that CRL5A system pres-
sure is shut down and bleed off before beginning disassembly. If CRL5A is
removed from pipeline for disassembly, be sure to use a soft jawed vise to
hold body (7) during work.
Refer to Parts List Drawing for Item Numbers.
1. Remove cap (1), loosen jam nut (10) and turn adjusting screw (9)
counterclockwise until spring tension is relieved.
2. Remove eight screws (4) holding cover (3), and powerunit (6) to
body (7). Note orientation of powerunit sensing port and cover
relative to control body for correct reassembly. Hold cover (3) and
powerunit together, remove from body (7) and place on suitable work
surface.
3. Remove cover (3) from powerunit (6). Remove spring (12) and two
spring guides (11) from cover (3). Thinner spring guide should be on
spring top.
4. Carefully unthread upper diaphragm washer (15) from stem (19) and
remove. Remove diaphragm (16), lower diaphragm washer (17), and
upper stem O-ring (5).
5. Pull stem (19) with lower disc assembly attached through bottom of
powerunit. .
6. 6.
Unscrew and carefully remove large hex disc retainer (21) and
remove disc assembly (23) from bottom of stem. Use soft jaw pliers
or vise to hold stem. The polished surface of stem must not be
scored or scratched, because o-ring leaks will occur.
7. The seat (22) need not be removed unless it is damaged. If removal
is necessary use proper size socket wrench and turn counterclock-
wise. NOTE: some models have integral seat in body.
INSPECTION
Inspect all parts for damage, or evidence of cross threading or leaking.
Check all rubber parts for tears, abrasions or other damage. Check all
metal parts for damage, corrosion, or excessive wear.
REPAIR AND REPLACEMENT
Minor nicks and scratches on metal parts may be polished out using water
and 400 grit (or finer) wet or dry sandpaper. CRL5A Repair kit p/n 20666E
consists of all rubber parts should be installed. When ordering replace-
ment metal parts or repair kits, be sure to include all nameplate data and to
specify desired item description and item number.
Refer to Parts List for Item Numbers.
REASSEMBLY
In general, reassembly is reverse of disassembly steps. However, follow-
ing steps should be followed.
1. Check that all parts are clean and in good condition before reassembly.
2. Before installing O-rings, lubricate them with waterproof grease (Dow
Corning 44 medium grade or equal).
3. Use grease very sparingly and install stem seal O-ring (18) in powerunit
(6).
4. Use soft jaw pliers or vise to hold stem (19) with large bottom end
facing up. Place disc assembly (23) with rubber facing up, on stem
bottom. Thread large hex disc retainer (21) onto stem (19) to hold disc
assembly (23) in place. Tighten large hex disc retainer (21) until snug
and rubber disc (23) remains flat. Do not overtighten.
5. Use grease very sparingly and install upper stem O-ring (5) on stem.
Install stem (19) from below through powerunit. Use a rotating motion
with slight pressure to let stem pass through O-ring without damage.
Do not cut O-ring with stem.
6. With stem (19) all the way up, place lower diaphragm washer (17) on
stem with serrated side up. Place diaphragm (16) on stem, then upper
diaphragm washer (15). Tighten upper diaphragm washer (15) onto
stem (19) until snug.
7. Position powerunit (6) with stem assembly on body (7). Locate
powerunit (6) sensing port as shown on parts list drawing.
8. Continue reassembly in reverse of disassembly steps 1, 2, and 3.
Note:
Before 1985, high-pressure design CRL5A controls used different
spring and spring guides that created a pre-load on assembly. During dis-
assembly, four regular screws were removed first. Then four longer screws
were used to “push” assembly apart. During reassembly, four longer
screws were used to “pull” assembly together. Then remaining four regular
screws were installed. Now with new spring and spring guides, eight regu-
lar screws (4) are used and control does not have pre-load to overcome.
SYMPTOM
PROBABLE CAUSE
REMEDY
Fails to open.
Controlling pressure
too low.
Back off adjusting
screw until valve
opens.
Fails to open with
spring compression
removed.
Mechanical obstruc-
tion, corrosion, scale
build-up on stem.
Disassemble, lo-
cate,and remove ob-
struction, scale.
Leakage from cover
vent hole when con-
trolling pressure is ap-
plied.
Diaphragm Damage
Disassembly replace
damaged di-
aphragm.
Fails to close with
spring compressed.
Mechanical obstruc-
tion.
Disassemble, locate
and remove ob-
struction.
Fails to close.
No spring compres-
sion.
Re-set pressure ad-
justment.
Loose diaphragm as-
sembly.
Tighten upper di-
aphragm washer.
Содержание 750B-4KG1
Страница 1: ...750B 4KG1...