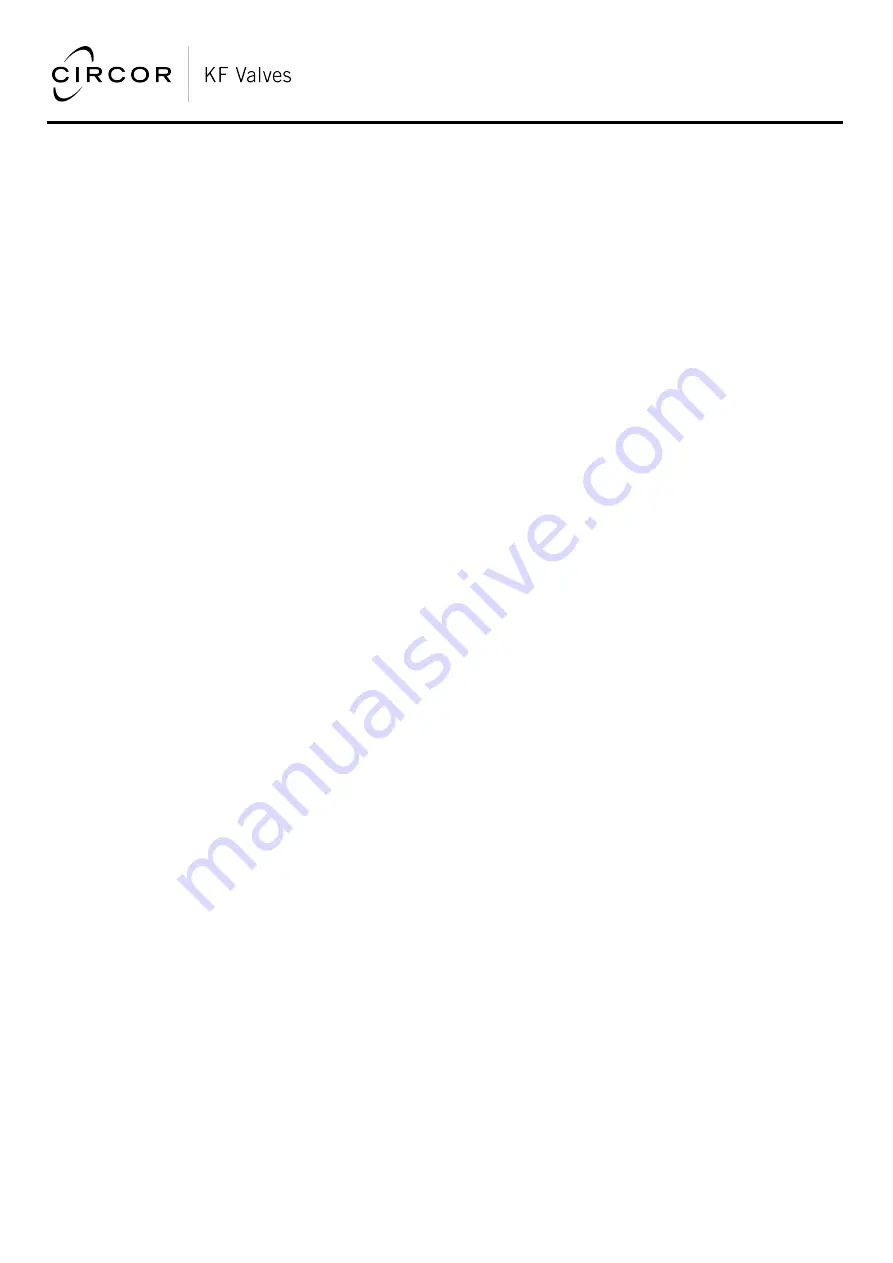
Installation, Operation and Maintenance Manual
SERIES T/TE/TW/TWE
ONE-PIECE TOP ENTRY
TRUNNION BALL VALVE
Page:
7
of
12
Document Name: IOM-T
Revision:
15333
Release Date: 06/26/2015
6) REASSEMBLY
Use new replacement parts, as required.
Install O-ring and back-up rings in their proper
locations and orient as follows:
Stem seal back-up rings (6) belong on the side
of the Stem O-ring (5) away from the ball and
with the concave face toward the O-ring. The
seat back-up ring (9) belongs on the side of the
seat O-ring (8) closest to the ball and with the
concave face toward the O-rings.
Use a liberal amount of general purpose
grease on seals and machined mating surfaces.
Fill the reliefs between stem O-rings with grease.
Install new trunnion bearings utilizing a
wooden block and hammer to drive them into
position.
Install seat assemblies and wave springs as far
as possible, by hand, into seat pockets of the
body. Take care to assure that O-ring seals are
not pinched during assembly. Seat assembly
must be placed deep enough into seat pocket so
that the conical point of the seat retraction
tools will contact the angled metal seat surface
when they are screwed into the threaded
retraction ports of the body. Using the box end
wrenches, screw the two seat retraction tools
inward, simultaneously.
Note:
It is important not to overstress the seats
by threading the seat retraction tools in too deep.
Therefore, after both seats are installed and
mechanical retraction is begun, continue to
check ball clearance so that you do not exceed
approximately 1/16" space per side to provide
for ball/stem installation.
Install ball/stem between retracted seats and
pilot lower stem through trunnion bearing and
into stem journal. Remove seat retraction tools,
allowing seats to engage with the ball surface.
Next, place a new bonnet seal in the recessed
diameter on body face. Install bonnet, noting
proper orientation with bonnet alignment pin
(22). Tighten bonnet cap screws until bonnet is
made up “metal-to-metal” with face of body.
Complete assembly by reinstalling retraction
port screws and seals, stem bearing, stop plate
and retainer or gear operator assembly.
Clean the parts and inspect them for damage,
wear and corrosion. Observe seat pocket bores,
stem seal bore and bonnet seal area for rust pits
and scale. If necessary, use fine emery for
removal of deposits on machined surfaces. Fine
emery may also be used very lightly on the ball's
spherical sealing surfaces.
Scratches or cuts on the sealing insert surface
of the seats are cause for replacement. Flush
lube and sealant injection fittings and channels
with two or three pumps of grease while valve is
disassembled. Replace seals and other parts, as
required.
Reassemble in reverse order. Use a liberal
amount of general purpose grease (such as
Mystic JT-6) on all seals and machined mating
surfaces. Fill the relief area between the stem
and lower trunnion O-ring grooves with grease.
Finally, assemble the Bonnet to the body and
uniformly tighten the Bonnet nuts.
7) VALVE SERVICING INTERVALS
Valve shall be inspected regularly during
operation
and
subjected
to
scheduled
maintenance. The operator is responsible for
servicing the valve at regular intervals. The
service intervals are determined by media in line,
temperature, pressure and number of cycles
during the operations. High pressure accelerates
the loss of lubricants.
8) VALVE MAINTENANCE GUIDE LINES
In order to guarantee efficient valve operation,
the valve shall be inspected on regular basis
during the operation and subject to scheduled
maintenance. All maintenance work shall be