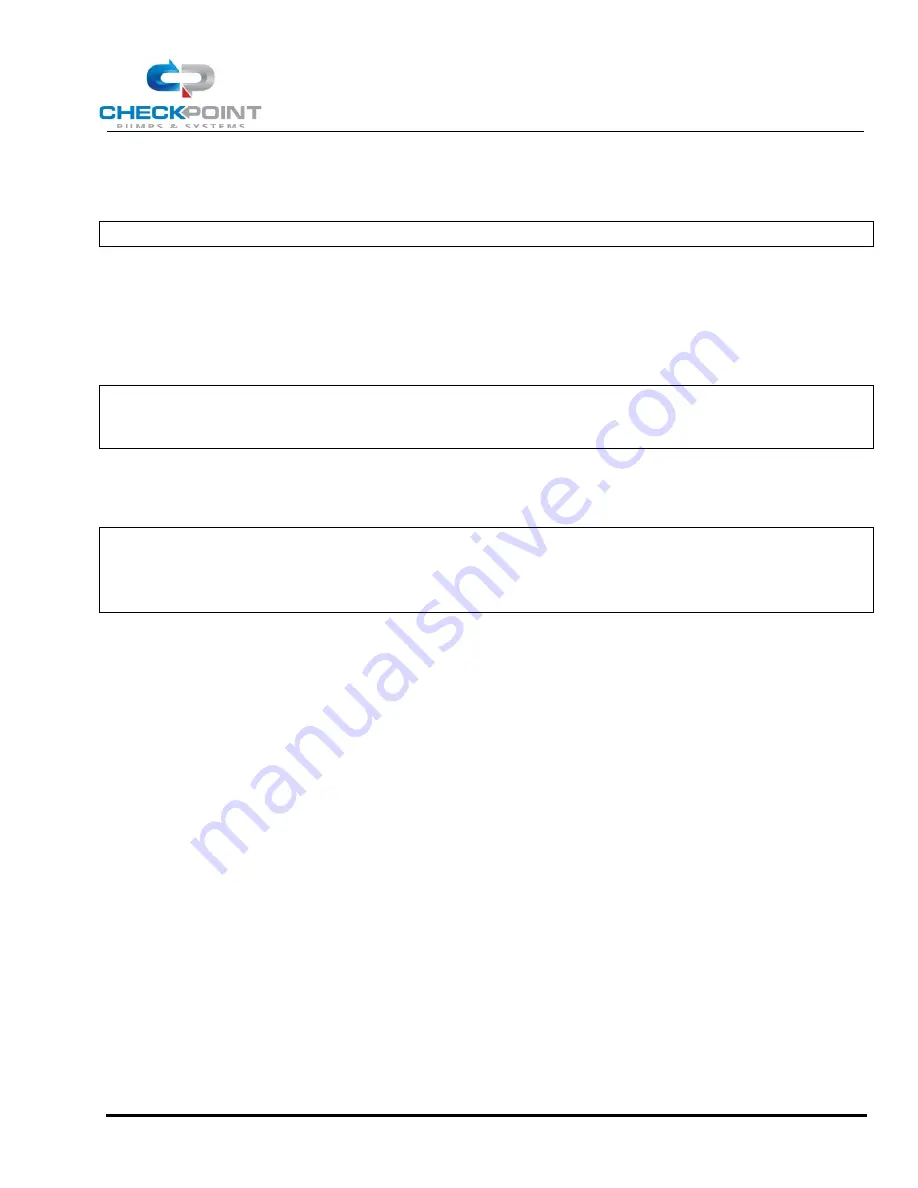
Series GX15 Pneumatic Chemical Injection Pump
Operating Manual
CP-MAN-PRD-GX15
REV06
EFF. DATE 07/23/2019
Page 4 of 12
components, please contact CheckPoint for assistance. Representatives are on staff & available to answer your
process questions. Checkpoint Engineers are also available to assist in system design. The CP Engineered Solutions
Department can be utilized for custom design and build options.
NOTE:
In Figure 1, the secondary chemical filter is optional under certain conditions but highly recommended.
1.1.3
CheckPoint recommends vertical mounting for its pumps where possible. This allows gravity to assist the
suction check valve during closing. You may mount the pump in other orientations, subject to the condition the
chemical head is no higher than level with the motor. If mounting other than vertical, you must order your pump
with a spring-loaded suction check, or order and install the appropriate suction check spring prior to installation.
CheckPoint recommends using a mounting bracket designed specifically for the Series GX15 pump when attaching
to any surface.
CAUTION:
Under no conditions should the pump be oriented with the suction check valve above the
centerline of the motor. Doing so may cause chemical leakage to collect in the motor, breach
the motor seals, and be atomized into the environment.
1.1.4
CheckPoint recommends use of a calibration gauge for assurance of proper pump function and chemical
delivery rate. Please read section 2.2
on page 8 for more information. The proper position
of the calibration gauge (labeled #5) is shown in Figure 1.
NOTE:
It is necessary to attach a vent tube to the top of all calibration gauges, chemical tanks, and tank level
gauges. The height of the top of each vent tube should always be greater than the highest possible
liquid level in the system. Proper vent tubes should have a means to prevent water entry, such as a 180
degree bend.
1.1.5
ALL COMPONENTS AND PIPEWORK BETWEEN THE CHEMICAL TANK AND THE SUCTION CHECK VALVE OF
THE PUMP MUST BE 100% BUBBLE-TIGHT AND FULLY COMPATIBLE WITH THE CHEMICAL AND WITH EACH OTHER.
FAILURE TO ADHERE STRICTLY TO THIS DIRECTIVE WILL LEAD TO LOSS OF PRIME AND DAMAGE TO THE PLUNGER
AND PLUNGER SEAL.
1.1.5.1
All fittings and screw-on joints
without Teflon™ tape or other
equivalent sealant may allow air at
atmospheric pressure to enter the suction tubing, even when no chemical leakage is visible.
1.1.5.2
Dissimilar metals in the suction side of the injection system may react with each other, creating gas
bubbles that will be carried into the pump head. All suction components; tubing, pipe, fittings, and valves must be
composed of similar or compatible materials. Please note that CheckPoint offers wetted parts comprised of 316
SS, Hastelloy C, PVC, Titanium and Alloy 20.
1.1.6
The pump may be mounted to a skid or other surface in a number of ways; however, clamping around the
outside of the pump can permanently affect the cylindricity of the injection head or motor thereby voiding the
product warranty. Proper mounting techniques increase accessibility during maintenance and troubleshooting.
1.1.7
Always check to ensure that all process block valves (labeled Nos. 1, 7 & 13 in Figure 1) are closed prior to
disconnecting or re-installing any chemical injection pump. There should always be a block valve placed between
the pump and the process flow, the gas supply, and the chemical supply. Conversely, while the pump is running, all
such block valves should always be open.
1.1.8
The pump suction line should be sized appropriately to the flow rate to avoid cavitatation. A general rule of
thumb is to size the suction line such that instantaneous flow velocity through the line does not exceed 2 feet per
second at any point. Additional allowances may be needed for multiple pump installations, extremely viscous
chemicals and for chemicals with high vapor pressures; contact CheckPoint or your Authorized CheckPoint
Distributor for design assistance.