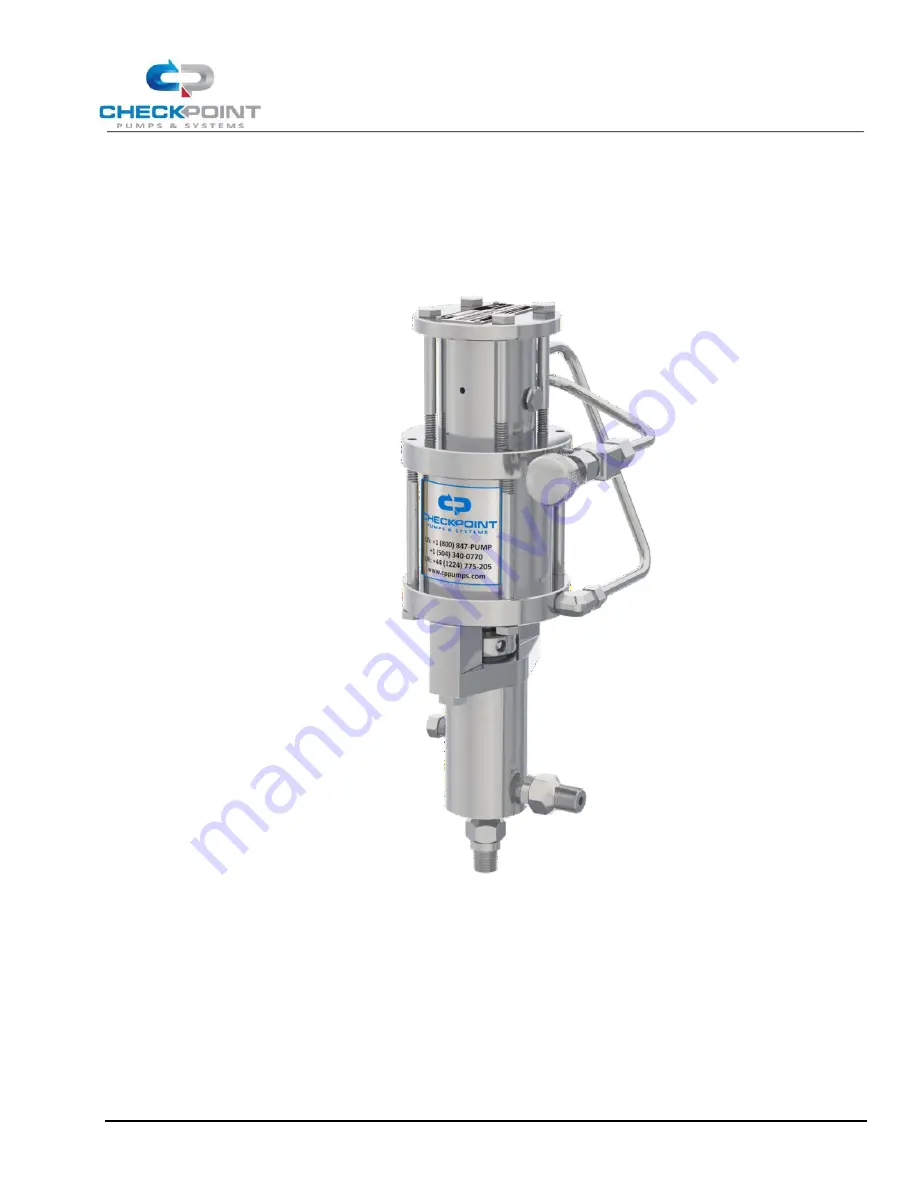
Series 1250 Pneumatic Chemical Injection Pump
Operating Manual
Page 1 of 19
Series 1250
Pneumatic Chemical Injection Pump
Operating Manual
Louisiana, US
Aberdeen, UK
21356 Marion Lane
Unit C2 Lombard Centre
Mandeville, LA 70471
Kirkhill Place, Kirkhill Industrial Estates
+1 (504) 340-0770
Dyce, Aberdeen, AB21 0GU Scotland
+44 (0) 1224 775205
CP Pumps & Systems FZE
Unit AA08, LIU 10
Jebel Ali
South | PO Box 262131
Dubai
|
UAE
+971 (4) 8806278
CheckPoint Systems Pte Ltd
21 Toh Guan Road East
#04-17 Toh Guan Centre
Singapore 608 609
+65 6261 7687
CP/MAN-PRD-015 REV. 15 EFF. DATE: 07/08/2022