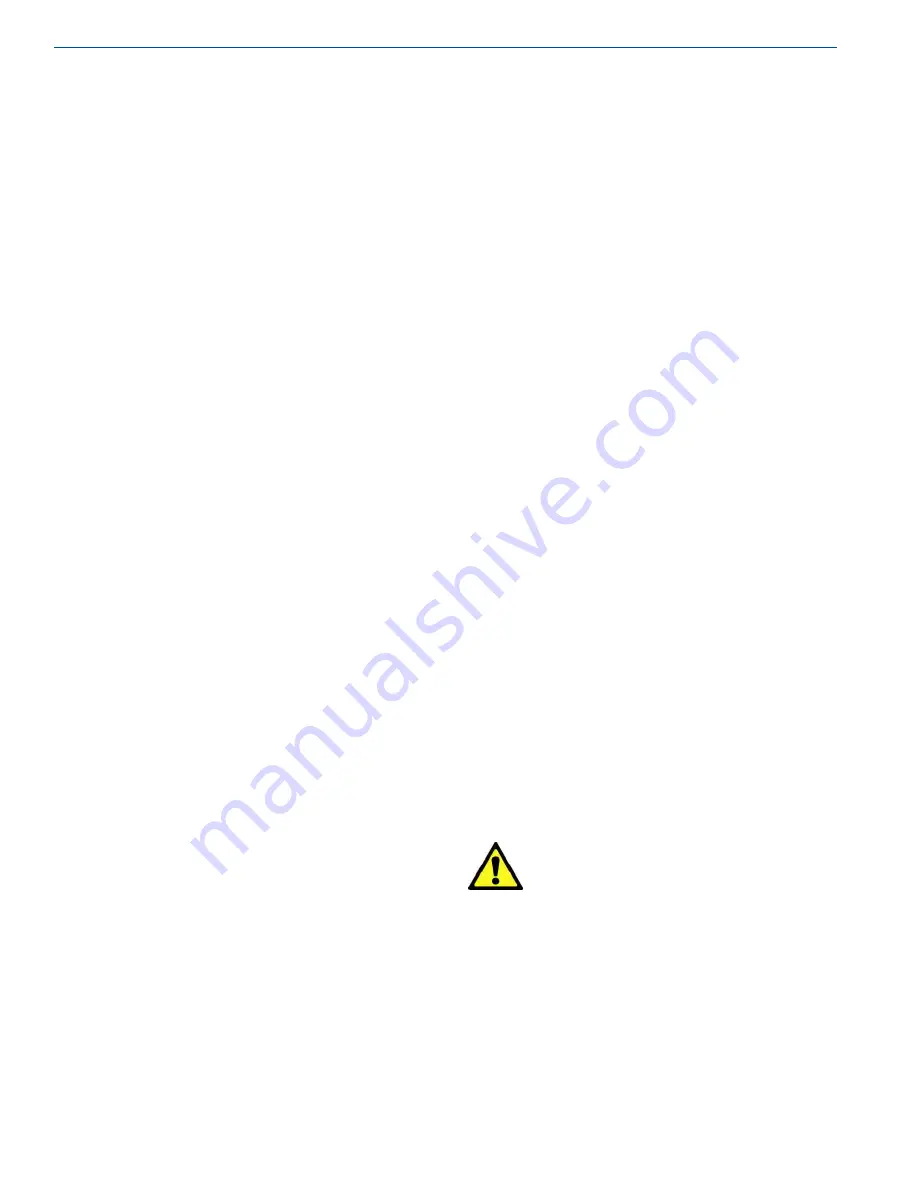
18
Operations
Product Manual - Liquid Cylinders
Filling Procedures
The Dura-Cyl
®
LCCM MP liquid cylinders are regulated by
the DOT/Transport Canada for transporting liquid oxygen,
nitrogen or argon. The filling of these liquid cylinders must
be done by product weight. This will allow enough gas space
above the liquid to keep the liquid cylinder from becoming
liquid full if its pressure rises to the relief valve setting. The
filling weight table indicates the correct product weight for
the various relief valve settings The standard relief valve
setting is 230 psig (15.9 barg). The filling procedure will
explain the proper way to use the filling weight table.
The liquid cylinder is equipped with liquid and vent valves
that are used during the filling procedure. The liquid valve is
equipped with a dip tube that extends into the inner vessel of
the cylinder and reaches to the bottom The vent valve has a
dip tube attached to it that also extends into the inner vessel
of the cylinder. This vent tube is designed to spray the liquid
into the top of the vessel so that pump filling through the
vent valve will keep head pressure down in the cylinder.
Filling can be accomplished by either pressure transfer or
pump fill. Follow these steps for filling Dura-Cyl LCCM MP
liquid cylinders:
1
Sample the residual gas that is in the cylinder. Purge the
cylinder if necessary to ensure the proper purity.
2
Place the cylinder on the filling scale. Record the
weight. Compare this weight to the registered tare
weight on the data plate. The difference is the weight of
the residual gas
3
Connect the transfer hose to the liquid valve Record the
new weight The difference between this weight and the
initial weight is the weight of the transfer hose
4
To determine the total filling weight add the tare weight
of the cylinder, the hose weight and the proper filling
weight from the filling table (i.e. Dura-Cyl 160 MP for
oxygen at 230 psi/16 bar has a product weight of 379
lbs/172 kg).
5
Open the cylinder vent and liquid valves. Open the
transfer line shut-off valve to begin the flow of product.
6
When the scale reads the calculated total filling weight
turn off the liquid valve on the cylinder Close the vent
valve
7
Close the transfer line shut-off valve and relieve the
pressure in the transfer line. Remove the transfer line.
Remove the cylinder from the scale
Operating Pressure
The liquid cylinder will automatically maintain a normal
operating pressure between the pressure building portion of
the LCCM (125 psi/8.6 bar) and the economizer portion of
the LCCM (140 psi/9.7 bar). The operating pressure can be
set up or down by simply adjusting the LCCM control knob
while watching the pressure gauge. The adjustment range of
the regulators is between 40 and 160 psi (2.8 and 11.0 bar).
The gas delivery pressure should not be confused with the
vessel operating pressure. The delivery pressure should be
adjusted with a separate regulator that is attached to the gas
withdrawal fitting.
Gas Withdrawal
The liquid cylinder will deliver gas at various flow rates
and temperatures for different applications. The flow rate
is controlled by the equipment that is being supplied from
the liquid cylinder. The continuous flow rate indicates the
flow rate that will normally provide gas at a reasonable
temperature and should not be exceeded. Higher flow rates
may provide very cold gas that could damage the equipment
attached to them
To supply gaseous product follow this procedure:
1
Connect the proper fill line regulator to the liquid
cylinder’s gas use outlet.
2
Connect the proper hose between the final line regulator
and the receiving equipment.
3
Open the pressure building valve.
4
Allow pressure to build to the operating pressure (125
psi / 8.6 bar).
5
Open the gas use valve.
6
Adjust the gas use regulator for the proper delivery
pressure.
7
When the gas delivery is completed, close all liquid
cylinder valves
Caution! The liquid and vent valves on
an empty liquid cylinder should
always be kept closed to protect
the inner vessel and plumbing
from being contaminated.
Service and Maintenance
Refer to the Maintenance section of this manual to
troubleshoot problems and service these liquid cylinders.
Содержание Cryo-Cyl80HP
Страница 2: ......
Страница 6: ......
Страница 12: ......
Страница 32: ......
Страница 50: ...44 Specifications Product Manual Liquid Cylinders MCR Plumbing Configuration...
Страница 52: ...46 Specifications Product Manual Liquid Cylinders LCCM Plumbing Configuration...
Страница 54: ......
Страница 56: ......
Страница 57: ...51 Product Manual Liquid Cylinders Appendix 1 Troubleshooting Guides Cutaway Explanation...
Страница 62: ...56 Appendix 1 Product Manual Liquid Cylinders Troubleshooting Flow Chart 3...