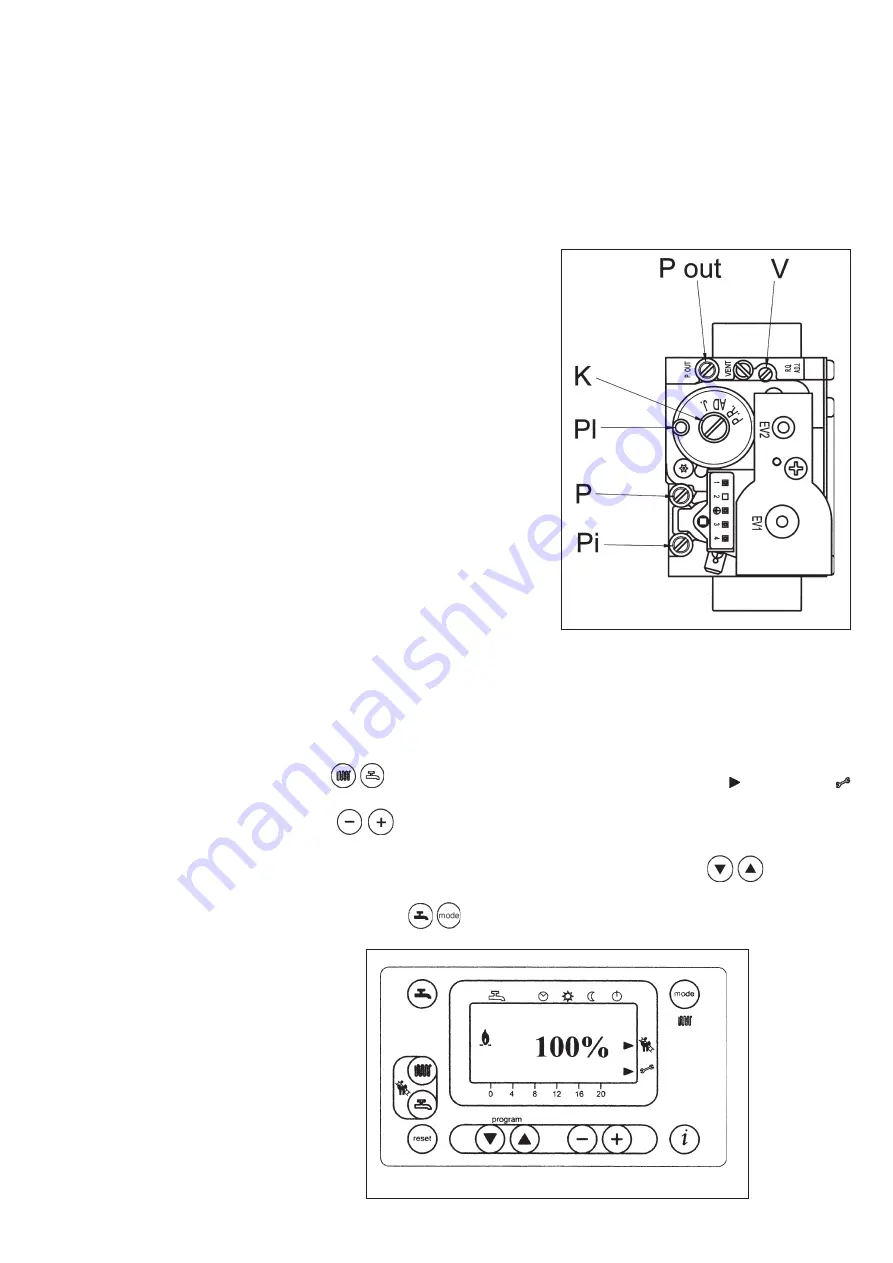
25
IMPOR
TANT:
If the appliance is being converted from natural gas to propane (LPG), the following
operations must be performed before calibrating the gas valve as instructed above.
• Turn adjuster screw (V) on the gas valve clockwise through the number of complete revolutions
specified in table 3.
To simplify calibration of the gas valve, the “calibration function” can be set directly on the boiler
control panel by proceeding as follows:
1) Press the
keys (2-3) together until the display shows the pointer “ ” alongside the
symbol (about 6 seconds).
2) Press the
keys to set the fan speed at the minimum and maximum heat output
(%PWM);
N.b - to set the
minimum
and
maximum
heat output quickly, press the
keys respecti-
vely;
3) press either of the two
keys to exit the function.
0307_2201
Figure 14
0310_01
14
Figure 13
Pi:
Gas supply pressure connection point
P out:
Gas pressure to burner connection point
P:
Pressure connection point
for measurement of the OFFSET
Pl:
Air signal input from fan
V:
Gas flow adjuster screw
K:
OFFSET adjuster screw
Carry out the following operations in the given sequence:
1)
Calibration of the maximum heat output. Check that the CO
2
measured on the flue, with the boiler
operating at the maximum heat output, is the same as that shown in table 1. Otherwise, turn the
regulation screw (V) on the gas valve. Turn the screw clockwise to reduce the concentration of
CO
2
and anticlockwise to increase it.
2)
Calibration of reduced heat output. Check that the CO
2
measured on the flue, with the boiler ope-
rating at the minimum heat output, is the same as that shown in table 1. Otherwise, turn the offset
regulation screw (K) on the gas valve. Turn the screw clockwise to increase the concentration of
CO
2
and anticlockwise to reduce it.
14. Gas valve adjustment