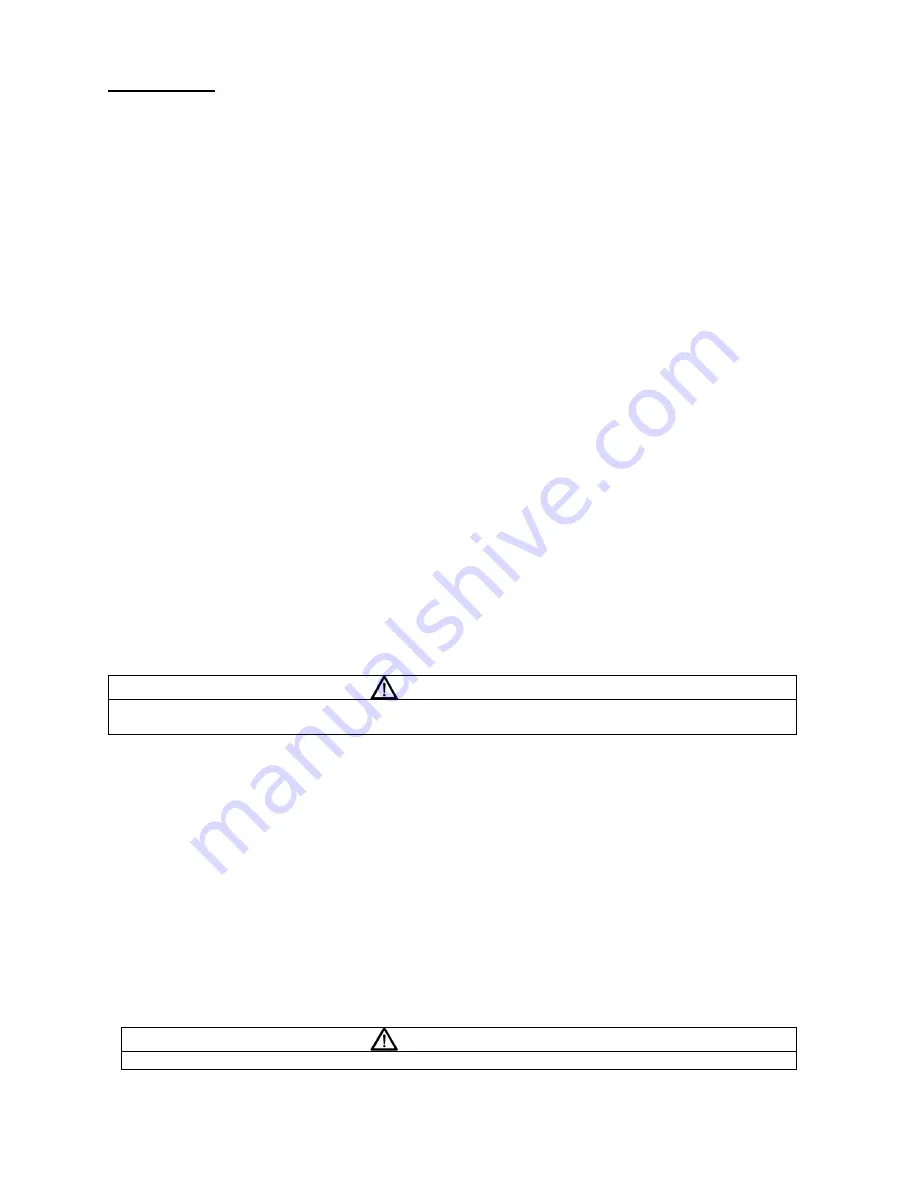
11
OPERATION
This compressor has been inspected, thoroughly tested and approved at the factory. For this unit to give
long satisfactory service it must be installed and operated properly. This compressor has been designed
for a 80%/ON – 20%/OFF duty cycle.
Simplex units have a pressure switch that senses changes in receiver pressure and automatically starts
and stops the compressor at preset pressure limits. If the receiver pressure falls below the cut-in
pressure setting of the pressure switch the compressor will run until the cut-out pressure setting of the
pressure switch has been reached.
Duplex units have lead and lag pressure switches and an automatic alternating system to evenly
distribute the load between the two compressors. The pressure switches sense changes in receiver
pressure and automatically start and stop the compressor at preset pressure levels. If the receiver
pressure falls below the cut-in pressure setting of the lead pressure switch but remains above the cut-in
pressure setting of the lag pressure switch, only one compressor will run until receiver pressure reaches
the cut-out pressure of the lead pressure switch. The next time the pressure in the receiver drops, the
system automatically starts the compressor that was idle. If the receiver pressure falls below the cut-in
pressure setting of the lag pressure switch, both compressors run until receiver pressure reaches the cut-
out pressure setting of the lead pressure switch.
Units furnished with head unloaders are equipped with a needle valve, pilot valve and head unloaders to
provide continuous run capabilities. The pilot valve acts as an automatic air switch allowing air to flow
from the receiver to the head unloader mechanism, thus actuating it. To operate unit in continuous run,
open needle valve located next to pilot valve. The pilot valve is now able to sense receiver pressure.
When the receiver pressure reaches the cut-out pressure setting of the pilot valve, the pilot valve opens
and air is released to the unloader mechanism. The compressor stops compressing air and runs
unloaded until the cut-in pressure setting of the pilot valve has been reached. At this time air released
from the unloader mechanism and the compressor starts compressing again. Continuous run is
recommended if motor starts exceed 8 starts/hour.
Initial Start Up
1.
Inspect unit for any visible signs of damage that would have occurred in shipment or during
installation.
2.
Pull main disconnect switch to unit to assure that no power is coming into the unit. “Lock Out” or
“Tag Out” switch. Connect power leads to start.
WARNING
Do not attempt to operate compressor on voltage other than that specified on order or on
compressor motor.
3.
Check compressor oil level. Add oil as required. See “Compressor Oil Specifications” Section.
NOTE
: Do not mix oil type, weights or brands.
4.
Activate main disconnect switch.
5. “Jog” motor and check for proper rotation by direction arrow. If rotation is wrong, reverse input
connections on the magnetic starter.
6.
Close receiver outlet hand valve and start.
7.
With receiver hand valve closed, let machine pump up to operating pressure. At this stage the
automatic controls will take over. Check for proper cycling operation.
8.
Check for proper operation of any options. Refer to individual option instruction sheet.
9.
When the initial run period has shown no operating problems, shut unit down and recheck oil level.
10. Open receiver hand valve. The air compressor unit is now ready for use.
WARNING
This unit can start automatically without warning.
Содержание HRA20-12
Страница 22: ...22 COMPRESSOR REPAIR PARTS ILLUSTRATION Models R70A C308 B Ref Drawing ...
Страница 28: ...28 UNIT HAZARD DECALS ...
Страница 29: ...29 PUMP HAZARD DECALS F ...