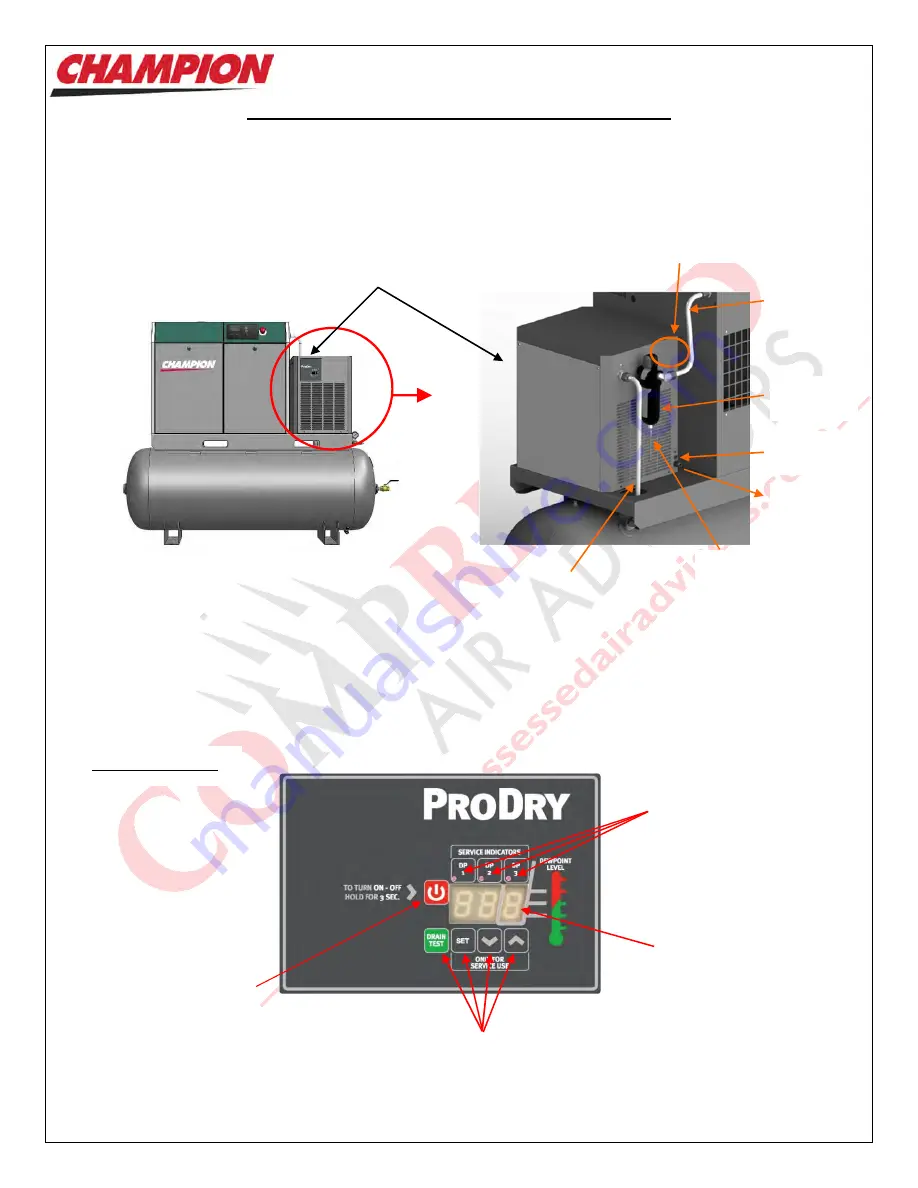
D10.D15.DRS15-MANS
Apr ‘19
- 37 -
Separator Filter and Refrigerated Air Dryer
Your Unit may be equipped with a Separator Filter and an ‘ASD Series’ Refrigerated Air Dryer Unit as indicated
below. These items are located in the compressed air lines after the air is compressed but before it enters the Air
Receiver. This allows for what is termed a ‘dry’ Tank.
*Drains will discharge automatically under pressure. It is recommended that pneumatic drain tubes be anchored
and filtered as per your local municipality regulations.
More detailed information concerning the Dryer Unit is included in the Dryer manual. The information contained in
this manual is a ‘quick reference’ only.
To Air
Receiver
On/Off
Button
LED’s for
Compressor,
Drain, and Fan
Test/Programming
Buttons
Dryer Controls
From Air
End
Unit Model and
Serial Numbers
Refrigerated
Air Dryer
Readout
Power Cord
115V
Pressurized
Moisture Drain*
Pressurized
Moisture Drain*
Separator
Filter
Содержание D10
Страница 34: ...D10 D15 DRS15 MANS Apr 19 34 Variable Speed Drive cont d Menu Button Navigation Chart ...
Страница 46: ......
Страница 48: ......
Страница 50: ......