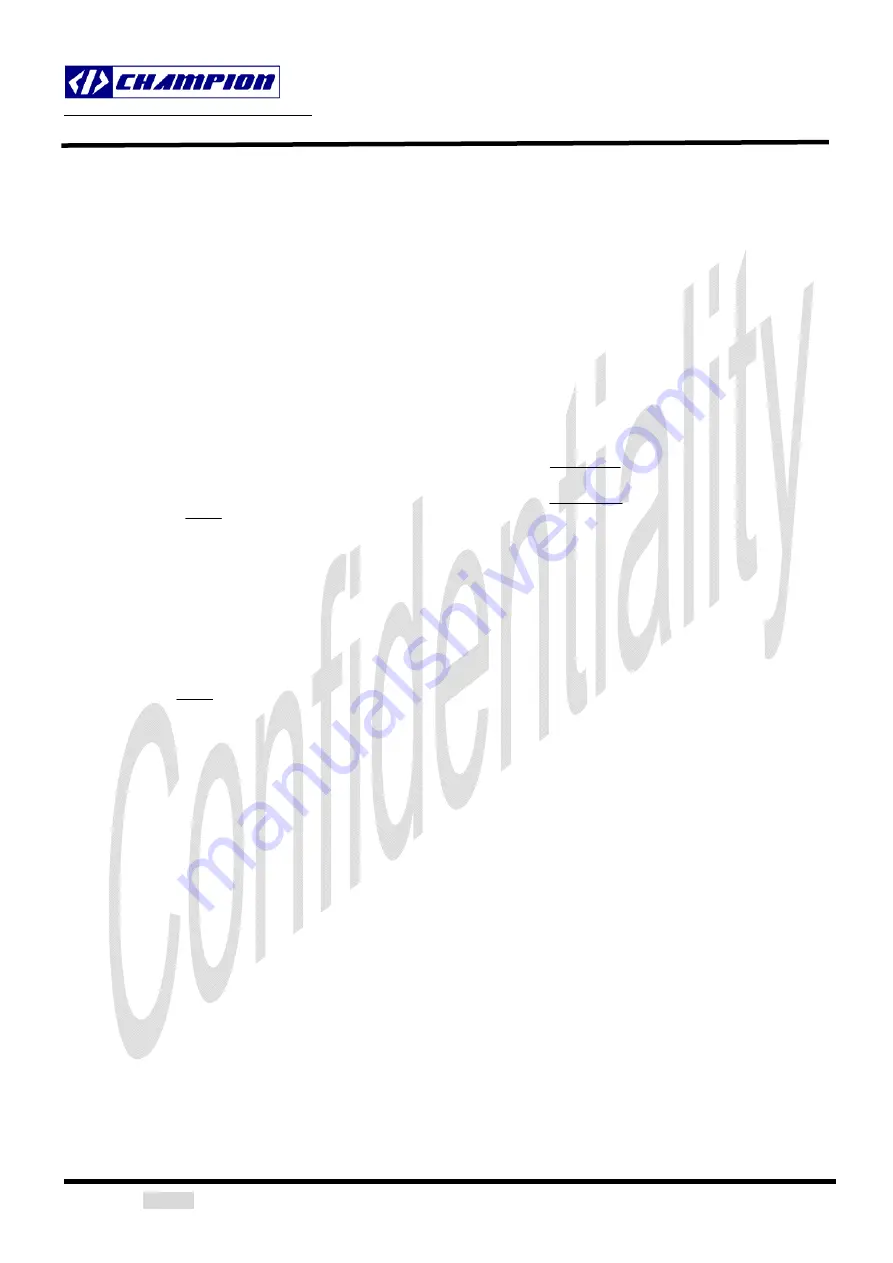
CM6800T
(Turbo-Speed PFC+Green PWM)
http://www.championmicro.com.tw
EPA/85+
PFC+PWM COMBO CONTROLLER
Design for High Efficient Power Supply
2010/08/03
Rev. 1.2
Champion Microelectronic Corporation
20
PWM Control (RAMP2)
When the PWM section is used in current mode, RAMP2 is
generally used as the sampling point for a voltage
representing the current on the primary of the PWM’s output
transformer, derived either by a current sensing resistor or a
current transformer. In voltage mode, it is the input for a ramp
voltage generated by a second set of timing components
(R
RAMP2
, C
RAMP2
),that will have a minimum value of zero volts
and should have a peak value of approximately 5V. In voltage
mode operation, feed-forward from the PFC output buss is an
excellent way to derive the timing ramp for the PWM stage.
Soft Start (SS)
Start-up of the PWM is controlled by the selection of the
external capacitor at SS. A current source of 10
μ
A supplies
the charging current for the capacitor, and start-up of the
PWM begins at SS~1.8V. Start-up delay can be programmed
by the following equation:
C
SS
= t
DELAY
x
1.8V
A
10
μ
where C
SS
is the required soft start capacitance, and the t
DEALY
is the desired start-up delay.
It is important that the time constant of the PWM soft-start
allow the PFC time to generate sufficient output power for the
PWM section. The PWM start-up delay should be at least
5ms.
Solving for the minimum value of C
SS
:
C
SS
= 5ms x
1.8V
A
10
μ
≒
27nF
Caution should be exercised when using this minimum soft
start capacitance value because premature charging of the
SS capacitor and activation of the PWM section can result if
VFB is in the hysteresis band of the 380V-OK comparator at
start-up. The magnitude of V
FB
at start-up is related both to
line voltage and nominal PFC output voltage. Typically, a
0.05
μ
F soft start capacitor will allow time for V
FB
and PFC
out to reach their nominal values prior to activation of the
PWM section at line voltages between 90Vrms and 265Vrms.
Generating V
CC
After turning on CM6800T at 13V, the operating voltage can
vary from 10V to 17.9V. That’s the two ways to generate VCC.
One way is to use auxiliary power supply around 15V, and the
other way is to use bootstrap winding to self-bias CM6800T
system. The bootstrap winding can be either taped from PFC
boost choke or from the transformer of the DC to DC stage.
The ratio of winding transformer for the bootstrap should be
set between 18V and 15V.
A filter network is recommended between VCC (pin 13) and
bootstrap winding. The resistor of the filter can be set as
following.
R
FILTER
x I
VCC
~ 2V, I
VCC
= I
OP
+ (Q
PFCFET
+ Q
PWMFET
) x fsw
I
OP
= 3mA (typ.)
EXAMPLE:
With a wanting voltage called, V
BIAS
,of 18V, a VCC of 15V
and the CM6800T driving a total gate charge of 90nC at
100kHz (e.g. 1 IRF840 MOSFET and 2 IRF820 MOSFET), the
gate driver current required is:
I
GATEDRIVE
= 100kHz x 90nC = 9mA
R
BIAS
=
G
CC
CC
BIAS
I
I
V
V
+
−
R
BIAS
=
9mA
5mA
15V
18V
+
−
Choose R
BIAS
= 214
Ω
The CM6800T should be locally bypassed with a 1.0
μ
F
ceramic capacitor. In most applications, an electrolytic
capacitor of between 47
μ
F and 220
μ
F is also required
across the part, both for filtering and as part of the start-up
bootstrap circuitry.
Leading/Trailing Modulation
Conventional Pulse Width Modulation (PWM) techniques
employ trailing edge modulation in which the switch will turn on
right after the trailing edge of the system clock. The error
amplifier output is then compared with the modulating ramp up.
The effective duty cycle of the trailing edge modulation is
determined during the ON time of the switch. Figure 4 shows a
typical trailing edge control scheme.