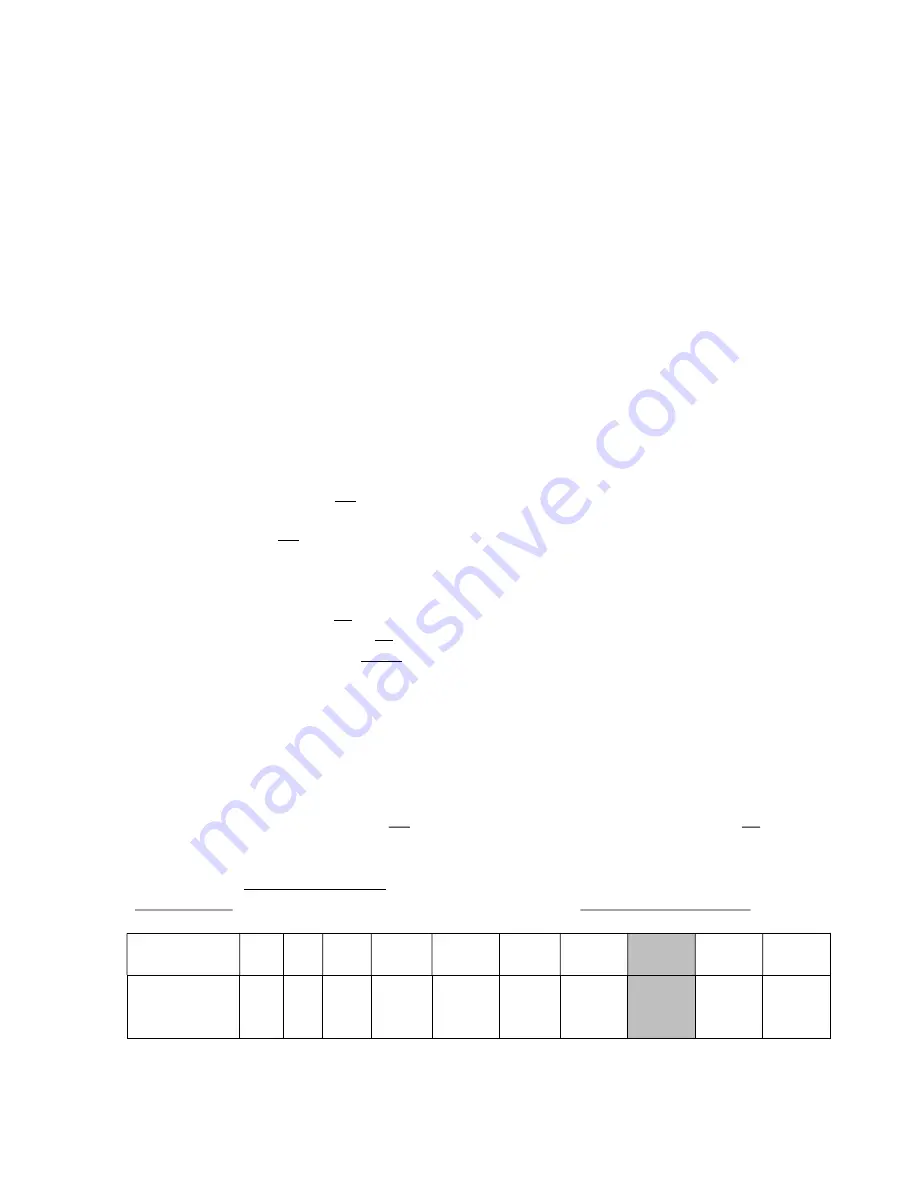
Rev G
Page 7
5/9/2017
Copyright © 2017 by Certified Cirus Control Systems. All Rights Reserved. No part of this material may
be reproduced in any form without the express written permission of Certified Cirus Control Systems
Valve Power
This is a static 12V output, which supplies 12 volts to the valve when the PWM port is
turned on.
PWM Output Signal
The PWM output produces a linear output PWM signal to a hydraulic coil which is
dependent on the Trigger, Engage, Min/Max calibration, and the Set Point dial. The
output is labeled ‘PWM’ on the back of the control panel and should be connected to the
valve with the SF-1005 cable. The full range of the Set Point dial (0-10) is used to vary
the signal.
Calibration
The
SCMC
TM
stores the minimum voltage, maximum voltage and frequency response for
various types of hydraulic setups. All 3 of these values are field configurable to provide
optimum user performance. To modify and/or change these values follow the below
process:
1.)Turn the engage switch “off” (Red part of the switch is NOT showing)
2.)Turn the power “off” on the
SCMC
TM
3.) Rotate the set point dial to number 10
4.) Turn the power switch “on”
a.) Within 1 seconds turn on the “ENGAGE” switch (red bar of switch showing)
b.) Within in 1 seconds rotate the set point dial to “0”
5.) The red LED on the front of the controller should now be blinking slowly
(approximately 10 times per second). If it’s not, start over at step 1.
6.) Turn the set point dial to 10 if you are using a 24 volt system, and to 0 for a 12 volt
system.
7.) Click the engage switch to the “off” position (non-red bar) and then back to the “on”
position. This saves the 24/12 volt supply voltage value.
8.) Choose the preferred frequency of the coil that the controller is attached to. Rotate the
set point dial to the desired number based on the table below.
Default is set to 200 hz.
Set Point
Dial Value
<1
2
3
4
5
6
7
8
9
10
PWM
Output
Frequency
40 60
80
100
120
150
175
200
250
300