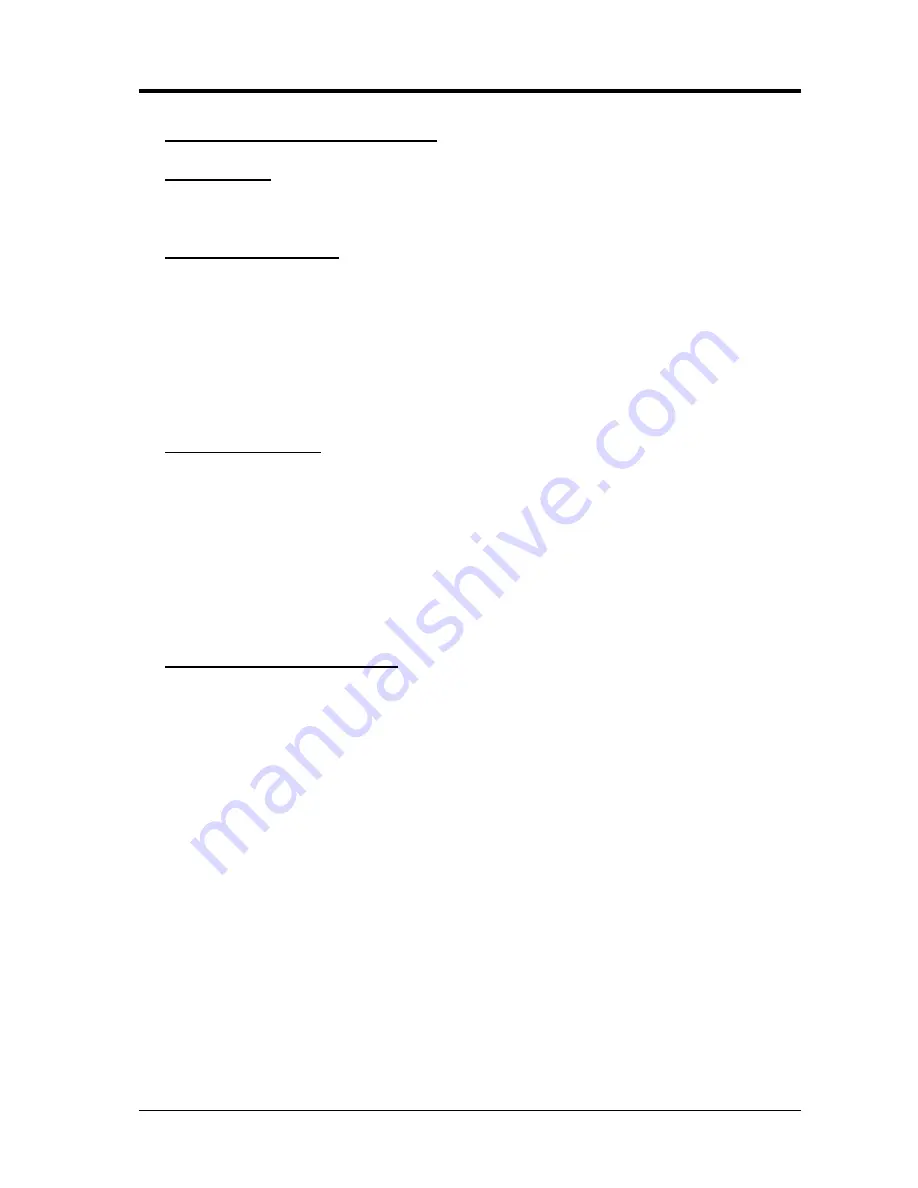
CEBORA S.p.A.
3
1
- GENERAL INFORMATIONS
1.1
- Introduction.
The purpose of this manual is to train personnel assigned to carry out maintenance on the
power source art. 283 for MIG/MAG, TIG-DC and MMA welding systems.
1.2
- General service policy.
It is the responsibility of the customer and/or operator to use the equipment appropriately, in
accordance with the instructions in the Instruction Manual, as well as to maintain the equipment
and related accessories in good working condition, in compliance with the instructions provided
in the Service Manual.
Any internal inspection or repairs must be carried out by qualified personnel who are
responsible for any intervention on the equipment.
It is forbidden to attempt to repair damaged electronic boards or modules; replace them with
original Cebora spare parts.
1.3
- Safety informations.
The safety notes provided in this manual are an integral part of those given in the Instruction
Manual. Therefore, before working on the machine, please read the paragraph on safety
instructions in the aforementioned manual.
Always disconnect the power cord from the mains, and wait for the internal capacitors to
discharge (2 minutes), before accessing the interior of the equipment.
Some internal parts, such as terminals and dissipaters, may be connected to mains or
otherwise hazardous potentials. It is therefore forbidden to work with the safety guards removed
from the machine unless strictly necessary. In this case, take special precautions such as wearing
insulating gloves and footwear, and working in a perfectly dry environment with dry clothing.
1.4
- Electromagnetic compatibility.
Please read and observe the instructions provided in the paragraph “Electromagnetic
compatibility” of the Instruction Manual.
3.302.233
22/09/2008
Содержание TRI STAR MIG 1635/M
Страница 1: ...CEBORA S p A 1 TRI STAR MIG 1635 M POWER SOURCE art 283 SERVICE MANUAL 3 302 233 22 09 2008...
Страница 23: ...14 Art 283...
Страница 25: ......