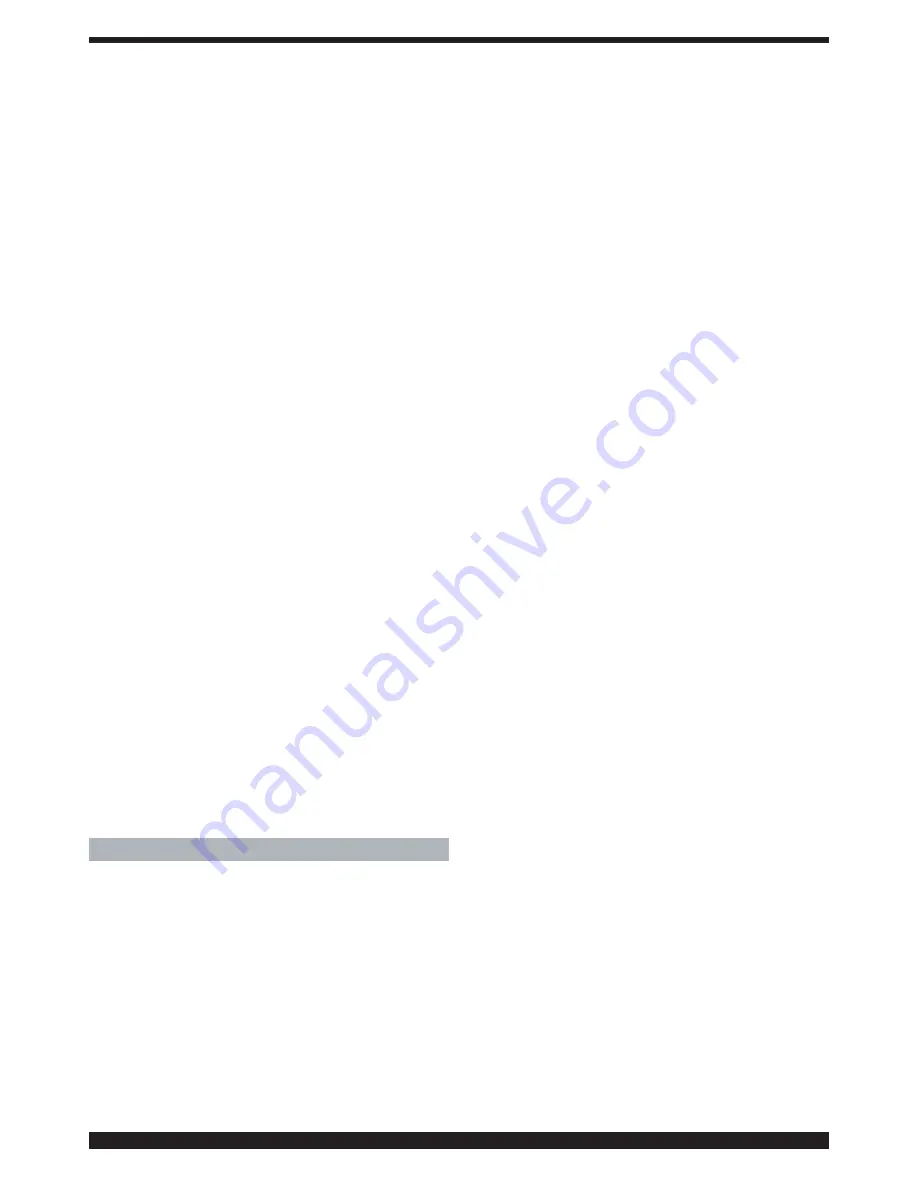
13
• Press the torch trigger to move the wire forward until it
comes out of the torch.
Caution: keep your face away from the gun tube assem-
bly while the wire is coming out.
• Screw the contact tip back on, making sure that the
hole diameter is the same as that of the wire used.
• Assemble the gas nozzle.
• Open the cylinder
4.3 W
WELDING C
CARBON S
STEEL
In order to weld these materials you must:
• Use a welding gas with a binary composition, usually
ARGON + CO2 with percentages of Argon ranging from
75% upward. With this blend, the welding bead will be
well jointed and attractive.
Using pure CO2 as a protection gas will produce narrow
beads, with greater penetration but a considerably
increase in splatters.
• Use a welding wire of the same quality as the steel to
be welded. It is best to always use good quality wires,
avoiding welding with rusted wires that could cause
welding defects.
• Avoid welding rusted parts, or those with oil or grease
stains.
4.4 W
WELDING S
STAINLESS S
STEEL
Series 300 stainless steels must be welded using a pro-
tection gas with a high Argon content, containing a small
percentage of O2 or carbon dioxide CO2 (approximately
2%) to stabilize the arc.
Do not touch the wire with your hands. It is important to
keep the welding area clean at all times, to avoid conta-
minating the joint to be welded.
4.5 W
WELDING A
ALUMINUM
In order to weld aluminum you must use:
• Pure Argon as the protection gas.
• A welding wire with a composition suitable for the base
material to be welded.
• Use mills and brushing machines specifically designed
for aluminum, and never use them for other materials.
• For welding aluminum you must use the torch: PULL
2003 Art. 2003.
5 S
SERVICE FFUNCTIONS
The abbreviations of these functions are shown on the
display G.
From within this menu, the operator may customize the
machine according to his needs.
To enter these functions press the key R and, while hold-
ing it down, briefly press and release the key O; release
the key R when the message "dSp" appears.
The same movement is used to exit these functions and
return to the welding programs.
Press the torch trigger to switch from one function to
another.
Exiting the service functions confirms the changes made.
CAUTION. Welding is not possible from within the service
functions.
5.1 D
DESCRIPTION O
OF TTHE FFUNCTIONS
• dSp ((display)
Active oonly iin p
pulsed ssynergic w
welding p
programs.
The display Q reads "A," which means that the display G
in normal conditions displays the Amperes. Pressing the
key O causes display Q to show SP (speed). This selec-
tion, in welding conditions, will make display G show the
wire speed in meters per minute.
NOTE: The speed will be shown before welding, because
after welding the display G shows the current used and
LED A remains lit.
• Job
Active iin aall w
welding p
programs.
The display Q reads "0", LED L is lit, and the machine is
ready for continuous welding.
Pressing the key O causes LED L to shut off, and display
Q reads "1"; LEDs C and M light, and the machine is
ready for dash welding.
Pressing the key O again makes the display Q read "2";
LED M shuts off and LED C remains lit, indicating that the
machine is ready for spot-welding.
• 2 - 44 ((manual-aautomatic)
The display Q shows the number 2 = two-stage = manu-
al welding
If the key O is pressed, display Q shows the number 4 =
4-stage = Automatic.
• (HSA) A
Automatic H
Hot S
Start
Active oonly iin p
pulsed ssynergic w
welding p
programs .
Caution: IIf tthe ffunction H
HSA iis aactivated, tthe ffunction 33L
is aautomatically nnot iincluded.
Display Q shows the message OF =OFF = Off
Pressing the key O causes the display Q to show the
message On = Active.
If this function is activated, pressing the torch trigger
causes the following messages to appear in sequence:
-S
SC ((Start ccurrent)
Range 1-20 (10-200%) of the wire speed corre-
sponding to the welding current set using knob B in
the welding programs. Manufacturer setting 13
(130%). Changed using keys O and R.
-LLen ((Duration)
This is the duration, expressed in seconds, of the pre-
viously displayed start current.
Range 0.1-10 sec., manufacturer setting 0.7.
Changed using keys O and R.
-S
Slo ((Slope)
Range 0.1-10 sec., manufacturer setting 0.5.
Changed using keys O and R.
Defines the interface time between the first current
(SC) and the welding current set using knob B in the
welding programs.
How iit w
works iin p
practice:
Welding takes place in manual mode (two stages).
The operator begins welding with the current corre-
sponding to the percentage greater than or less than
the wire speed set in SC (in this specific instance,
30% higher). This current will have a duration, in sec-
onds, corresponding to the time set in Len (in this
specific instance, 0.7 sec), after which the current will