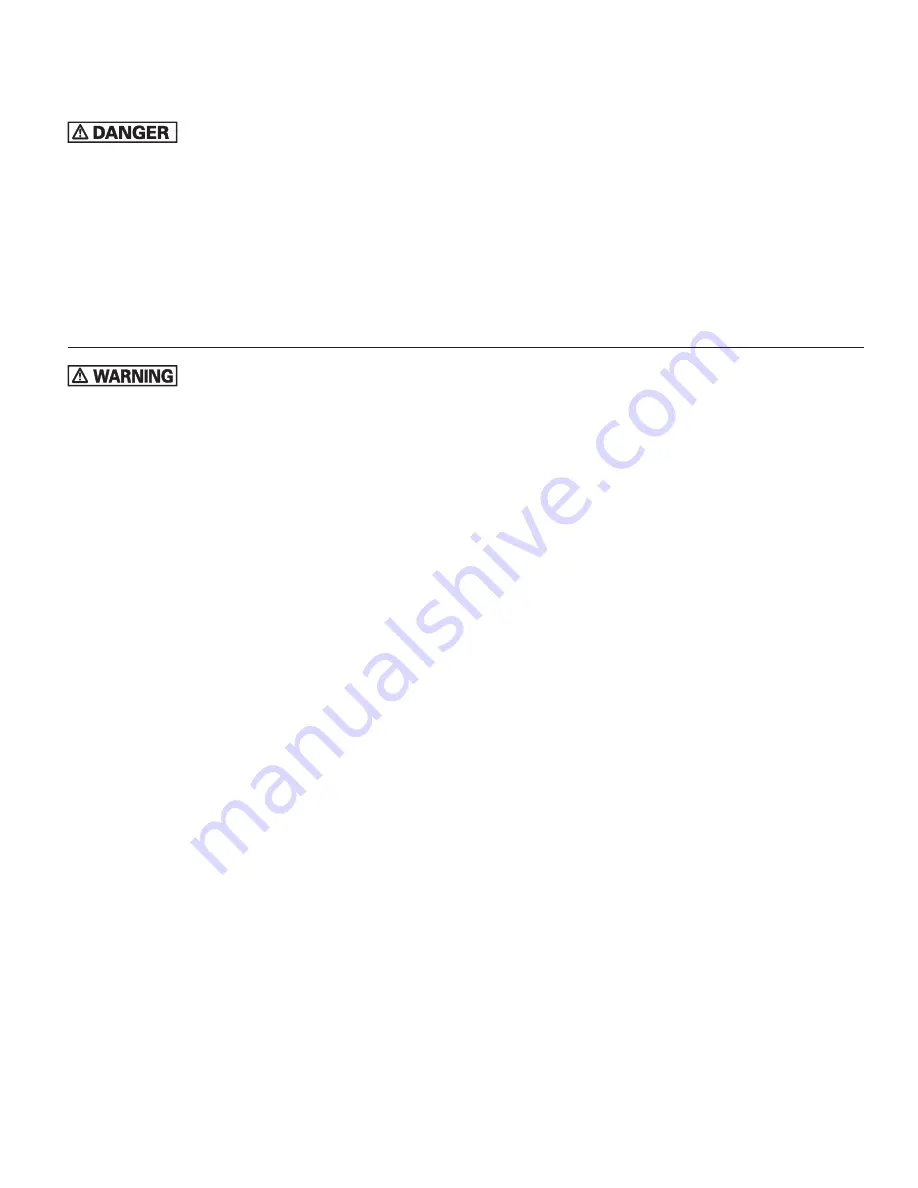
SERVICE MANUAL | 25 Frame Plunger Pumps
3
(763) 780-5440 | [email protected] | www.catpumps.com
General Safety Information
A. FLAMMABLE OR EXPLOSIVE LIQUID HAZARD
Do not operate pump with flammable or explosive liquids unless extraordinary safety precautions are observed. Leaks of flammable or explosive
liquids, if exposed to elevated temperatures, static electricity, sparks or other hazards, will result in flame or possible explosion, causing serious
personal injury, death or property damage.
1. Before operating pump with flammable or explosive liquids, ensure proper maintenance has been performed.
2. Do not operate pump with flammable or explosive liquids if leaks are detected.
3. Only pump flammable or explosive liquids that are compatible with pump component materials.
4. Do not operate pump with flammable or explosive liquids without safeguards or safety systems to detect leaks, elevated temperatures,
spark prevention or any other hazards defined by the NFPA systems.
5. Do not remove Flammable Liquids Product Suitability Hang Tag to assure proper safety.
6. Follow ATEX guidelines for potentially-explosive atmospheres.
A. ELECTRICAL SHOCK HAZARD
Do not service pump or electrical equipment while energized. Electricity can cause personal injury, death or property damage.
1. Adhere to “Lock Out” and “Tag Out” procedures for electrical equipment.
2. Before commencing pump service, turn power supply off.
3. Keep water away from electrical outlets and electrical devices.
4. Electrical components must be installed by a qualified electrician to avoid risk of electrocution.
B. ROTATING PARTS HAZARD
Do not service pump while energized. Moving, rotating or reciprocating parts can crush and cut, causing personal injury, death
or property damage.
1. Adhere to “Lock Out” and “Tag Out” procedures for electrical equipment.
2. Before commencing pump service, turn power supply off, turn water supply off, squeeze trigger on gun to relieve system pressure.
3. For mobile equipment, be sure engines and hydraulics are turned off and secured to avoid accidental start.
4. Do not operate with safety guards removed.
5. Always use safety guards on all belt drives, couplings and shafts.
C. HOT SURFACE HAZARD
Do not touch pump, accessories or drive system while operating and until cool down is complete. Touching hot surface areas of the pump,
accessories or drive system can cause severe burns or personal injury.
D. SKIN PUNCTURE HAZARD
Do not allow spray to contact any part of the body or animals. Pumped liquids under high pressure can pierce skin and underlying tissue
or can deflect debris leading to serious personal injury or death.
1. Relieve all line pressure in the inlet line to the pump and discharge line from the pump before performing any maintenance on the pump.
2. When a high-pressure gun is not in use, set safety trigger lock (safety latch) to avoid accidental high-pressure operation and personal injury
or property damage.
3. Do not check for leaks with hand. Use a piece of cardboard to check for leaks.
4. Review cleaning procedures to minimize heavy back blasting.
5. Wear adequate safety equipment and clothing when operating a high-pressure
sprayer. Never use high-pressure spray with bare feet or exposed skin, and always wear safety glasses.
E. PUMPING LIQUIDS HAZARD
Do not operate pump with hot water, chemicals or other hazardous liquids unless extraordinary safety precautions are observed.
Pumping hot water, chemicals or other hazardous liquids can expose personnel to serious injury.
1. Provide guards or shields around equipment to protect personnel.
2. Wear mask, goggles or eye protection while operating high-pressure equipment.
3. Obtain a Safety Data Sheet (SDS) and take appropriate safety measures for the liquid being handled.