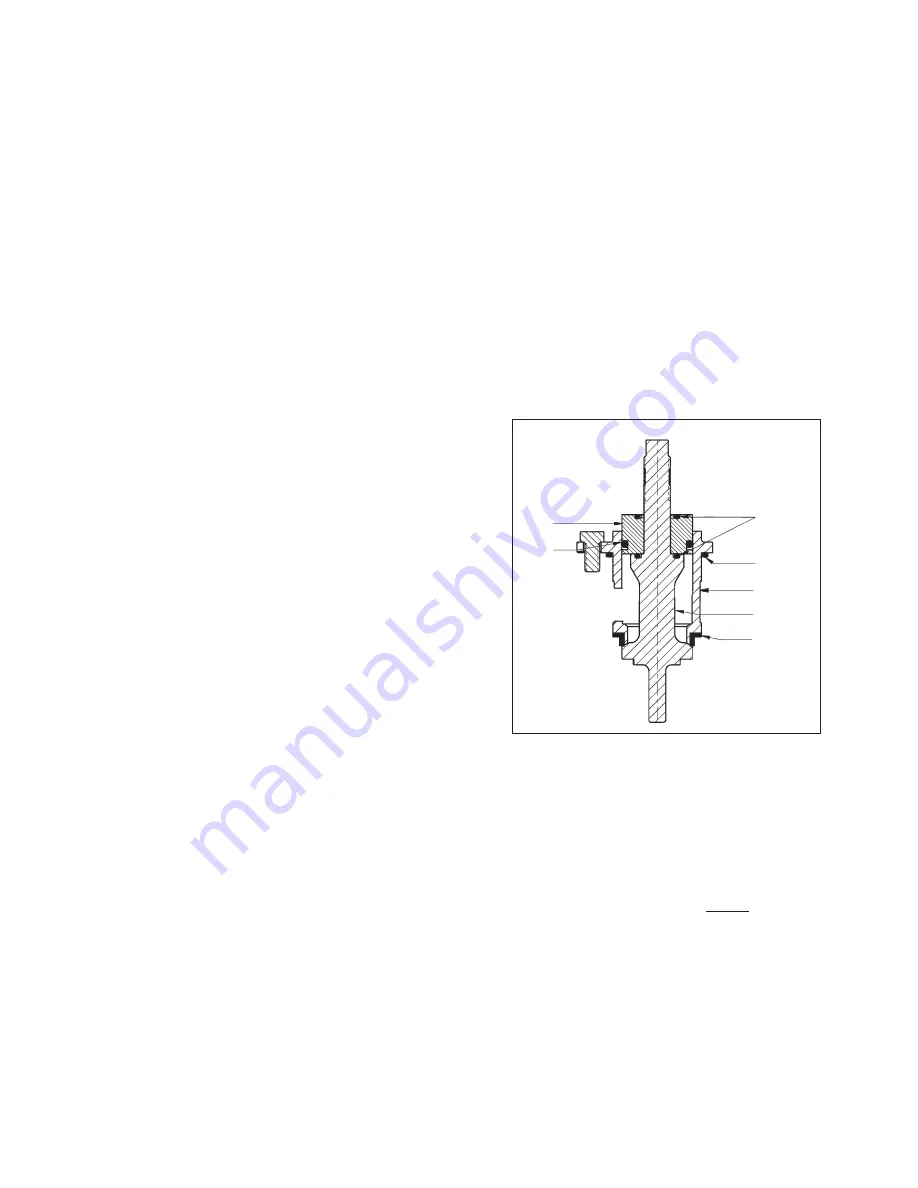
IOM-PGR-1
4
mine if sig nif i cant leakage was oc cur ring.
If the dy nam ic side seal shows signs of
sig nif i cant leakage, de ter mine if op er at-
ing con di tions are ex ceed ing pres sure,
pres sure drop, or tem per a ture limits.
Remove dynamic side seal com po nents.
Special care should be taken when us-
ing “tools” to remove the components to
ensure that no scratches are imparted
to any portion of the guide bearing (9)
groove.
e. Remove o-ring lower stem seal (13) from
plug (5).
f. Remove seat (10); examine for signs of
leakage. If seat ring shows signs of sig-
nificant leakage, determine if op er at ing
con di tions of pressure, pressure drop, or
temperature are ex ceed ing limits.
8. Place matchmarks on body (1) and cover
dome (2) flanges. Remove cover dome.
9. With wrench grasp and hold the milled “flats”
on top of the valve plug (5) stationary. Rotate
di a phragm nut (11) CCW and remove .
10. Remove upper diaphragm plate (7).
11. Remove diaphragm (6) and o-ring upper stem
seal (13). Examine diaphragm to determine
whether failed; determine if op er at ing condi-
tions are ex ceed ing pressure, pressure drop
or temperature limits.
12. Re
move lower diaphragm pusher plate (8).
13. Rotate the cage bolts (22) CCW evenly in single
revolution increments. Regulator con tains a
lower return spring (18); the ITA should rise
up as the cage cap screws are evenly backed
out. A down wards holding force should be
ap plied to the top of the guide bearing (9) to
pre vent the ITA from pop ping up as the last
threads of the cage bolts are backed out.
14. Remove the ITA by pulling up on the valve
plug (5). Set ITA aside.
15. Remove the lower return spring (18) from
within the body (1) cavity.
16. Remove cage o-ring seal (14). It may have
been removed when the ITA was lifted out of
the body.
17. Remove internal sensing drilled plug (19) us-
ing 5/32" (4 mm) allen wrench.
18. Remove body (1) from vise. Clean all re us able
metal parts according to owner's pro ce dures.
C. Disassembly of the ITA:
1. See Figure 1 for details:
a. While holding the cage (4) pull the valve
plug (5) down wards and through of the
guide bear ing (9) and out the bottom of
the cage.
b. Remove the guide bearing (9) from the
upper end of the cage (4).
c. Remove o-ring middle stem seal (13) from
guide bearing (9).
d. Examine the com po nent(s) (15 or 15.1,
15.2) of the dy nam ic side seal to de ter-
Figure 1:
Assembled ITA,
D. Inspection of Parts:
1. After inspection remove from the work area
and dis card the old “soft goods” parts (i.e. o-
rings, di a phragms, seals, gaskets, etc.) after
in spec tion. These parts MUST be re placed
with fac to ry supplied new parts.
2. Inspect the metal parts that will be reused. The
parts should be free of surface con tam i nants,
burrs, oxides, and scale. Rework and clean
parts as necessary. Surface con di tions that
affect the regulator performance are stated
below; replace parts that can not be re worked
or cleaned.
10
4
14
15
9
13
5