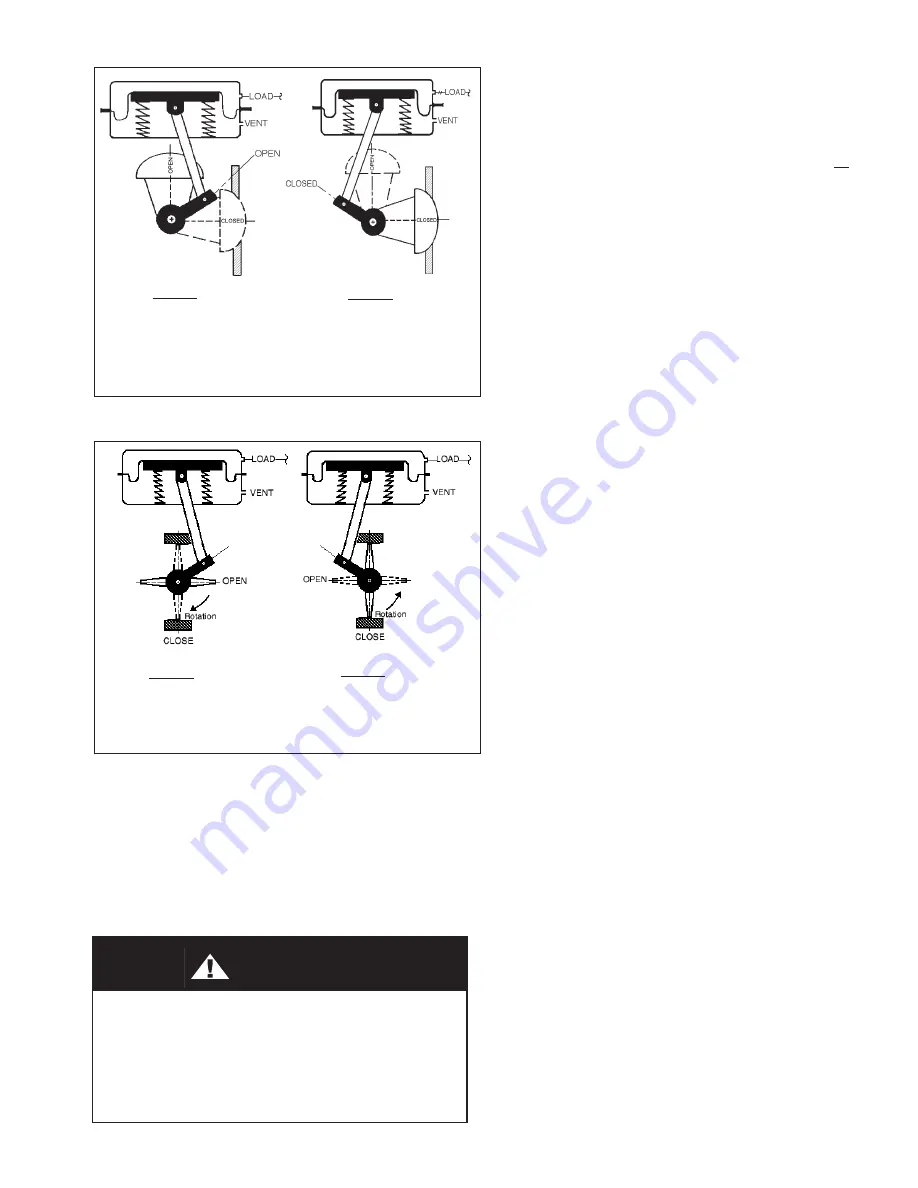
IOM-48
11
3. Ensure that manual handwheel (58) operator
is fully rotated upwards by loosening locking
lever (59) and ro tat ing CCW (viewed from top
side) as far as possible.
4. Place a matchmark between actuator casings
(1) (2).
SPRING UNDER COMPRESSION. Prior to re mov ing
fl
ange bolting (27, 28, 41, 42) re lieve range spring
(11) compression by rotating the handwheel or
adjusting screw assembly (58) CCW (viewed from
above handwheel (58) until all spring com pres sion
is re lieved. Fail ure to do so may result in
fl
ying
parts that could cause personal injury.
CCW-TO-OPEN
ATC-FO
(DIRECT)
Push Down-to-Close
CCW-TO-OPEN
ATO-FC
(REVERSE)
Push Down-to-Open
CCW-TO-OPEN
ATC-FO
(DIRECT)
Push Down-to-Close
CCW-TO-OPEN
ATO-FC
(REVERSE)
Push Down-to-Open
Figure 10
Ranger Plug vs. Lever Arm vs. Actuator Ori en ta tion
Figure 11
Premier Plug vs. Lever Arm vs. Actuator Ori en ta tion
NOTE: To switch “action” requires locating actuator stem
to opposite side of valve stem.
NOTE: To switch “action” requires locating actuator stem
to opposite side of valve stem.
5. Loosen all casing (1,2)
fl
ange bolting (27, 28,
41, 42) two revolutions. Pry apart the casings
(1,2) if “stuck” together.
6. In one revolution increments loosen all op-
pos ing nuts (41, 42) until the short bolting
(27, 41) disengages and can be removed.
Con tin ue loosening extension nuts (42) in
the alternating, one revolution pattern ensur-
ing that the cas ings (1, 2) are being “pushed
apart”, until the extension bolting (28, 42) is
disengaged and removed.
7. Lift the upper casing (1) upwards and away
from the lower casing (2). Set upper casing
(1) aside.
8. Remove pivot screw (25) by rotating CCW
(viewed from above), and seal (56).
9. Pry diaphragm washer (52) loose. Clean
wash er (52) of any rubberized sealant.
10. Prior to diaphragm (6) removal, inspect to see
where a diaphragm (6) leak may have been
caused by wearing against the upper case (1)
at any point. Inspect the upper case (1).
NOTE:
The diaphragm (6) is a rolling di a phragm and
should NOT touch the upper case (1) at any
point of the piston’s (3) up wards/downwards
travel. If there is side move ment of the piston
(3), further dis as sem bly for inspection of range
springs (11) is man da to ry. If there is topside
wear, uptravel stop washer (54) is not prop er ly
adjusted.
11. Remove diaphragm (6) and discard.
12. Clean surface of piston (3) of any foreign
material that could cause a premature failure
of diaphragm (6) if cov ered. Turn diaphragm
(6) “inside-out”. Place diaphragm (6) onto
piston (3) centered over the center bolt hole
in piston (3); ensure that the smooth black
sur face of di a phragm (6) is on the “pressur-
ized air-side”.
13. Place silicone sealant, Dow-Corning “Silastic”
#732 RTV or equal, around the diaphragm’s
(6) center bolt hole opening. Lay diaphragm
washer (52) onto sealant and centered over
bolt hole. Replace seal (56) on top of washer
(52).
14. Place a tool around the skirt circumference
of the piston (3) to secure during tightening;
use tape or similar material to prevent this tool
from leaving sharp edges that could damage
WARNING