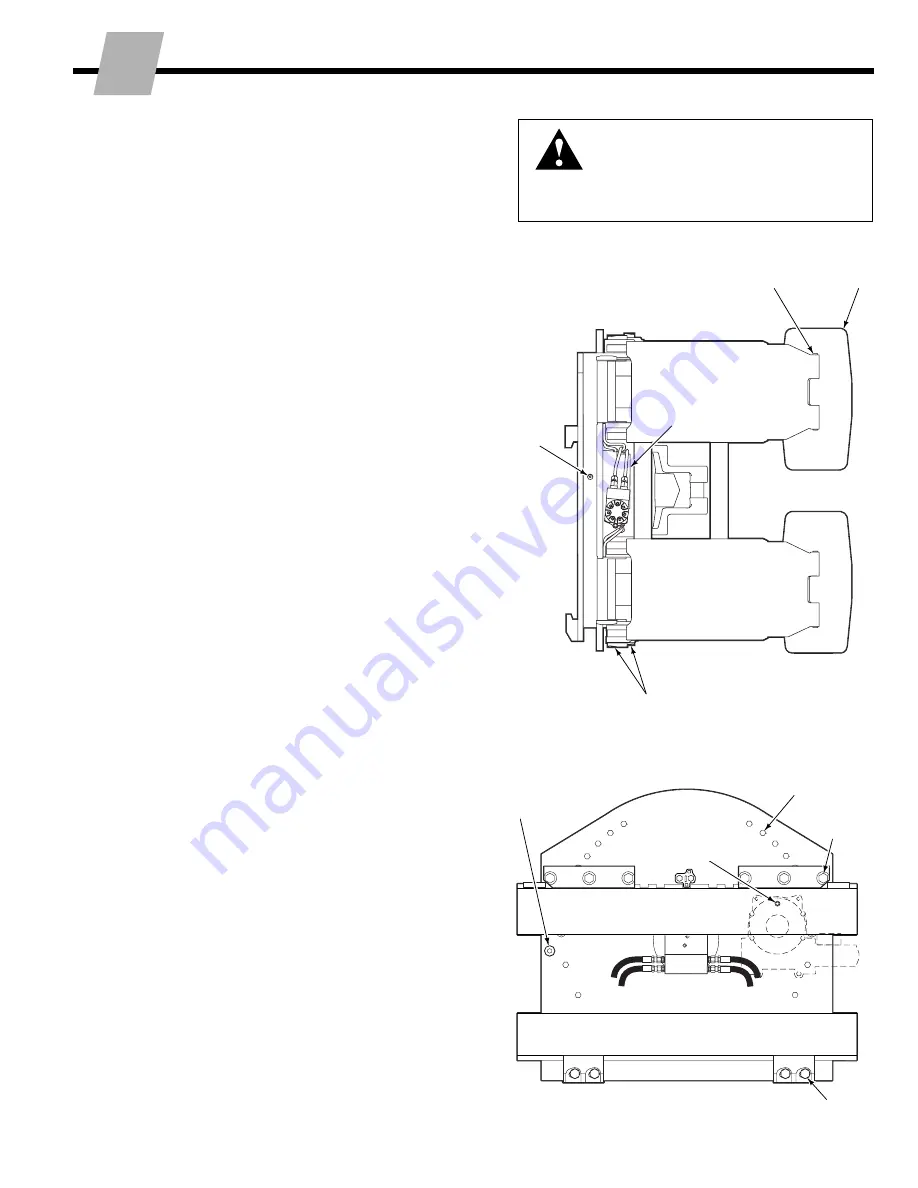
6028021 Rev. 1
11
ERIODIC MAINTENANCE
P
100-Hour
Maintenance
Every time the lift truck is serviced or every 100 hours of
truck operation, whichever comes first, complete the
following maintenance procedures:
• Check for loose or missing bolts, worn or damaged
hoses and hydraulic leaks.
• Check edges of contact pads for wear or sharp nicks
that could damage or tear paper rolls. Grind edges
smooth.
• Check contact pad pivot joints for wear and replace
or repair if necessary (see Service Manual).
• Check that load holding hydraulic system is function-
ing properly. Clamp Force Indicators 831887, 830141
and 832442 are available for this test.
• Check decals and nameplate for legibility.
500-Hour
Maintenance
After each 500 hours of truck operation, in addition to the
100-hour maintenance, perform the following proce-
dures:
• Tighten baseplate-to-bearing assembly capscrews to
75 ft.-lbs. (95 Nm).
• Tighten faceplate-to-bearing assembly capscrews to
75 ft.-lbs. (95 Nm).
NOTE:
Access capscrews
through plug in baseplate (see illustration).
• Lubricate rotator bearing assembly with wheel bearing
grease. Rotate clamp in 90-degree increments and
grease in each position.
• Tighten all mounting hook capscrews to 260 ft.-lbs.
(350 Nm).
• Check rotator drive gearcase lubricant level. Rotate
clamp so rotator drive is upright and remove small hex
socket plug from top of front cover. Lubricant should
run out of hole. If necessary, rotate Clamp 90
degrees and fill with Cascade Rotator Drive Lubricant,
Part No. 656300, or SAE 90 wt. gear lube (AGMA
'mild' 6 EP Gear Oil).
CAUTION:
Replace check plug using Loctite 271.
• Inspect all arm and cylinder pivot bushings for wear
and replace if necessary (see Service Manual
674512).
• Inspect all load-bearing structural welds on arms,
swing frame pivots, arm pivots and cylinder pivot
areas for visual cracks. Replace components as
required.
2000-Hour
Maintenance
After each 2000 hours of truck operation, in addition to
the 100 and 500-hour maintenance, perform the following
procedures:
• Inspect all arm and cylinder pivot pins for wear and
replace if necessary (see Service Manual 6028021).
WARNING:
After completing any service
procedure, always test the Clamp
through five complete cycles. First test
empty, then test with a load to make sure
the Clamp operates correctly before
returning it to the job.
Arm, Cylinder Pivot Pins, Bushings
RC0957.ill
Rotator
Bearing
Assembly
Grease
Fitting
RC0929.ill
Contact
Pad Edges
Rotator Drive
Contact Pad
Pivot Joints
Long Arm Side
Lower Hook
Capscrews
Baseplate-to-Bearing
Assembly Capscrews
Upper Hook
Capscrews
FX-Series Back (Driver's) View
Rotator Drive
Lubricant Level
Check Plug
(front side)
Access Plug for
Faceplate-to-Bearing
Assembly Capscrews