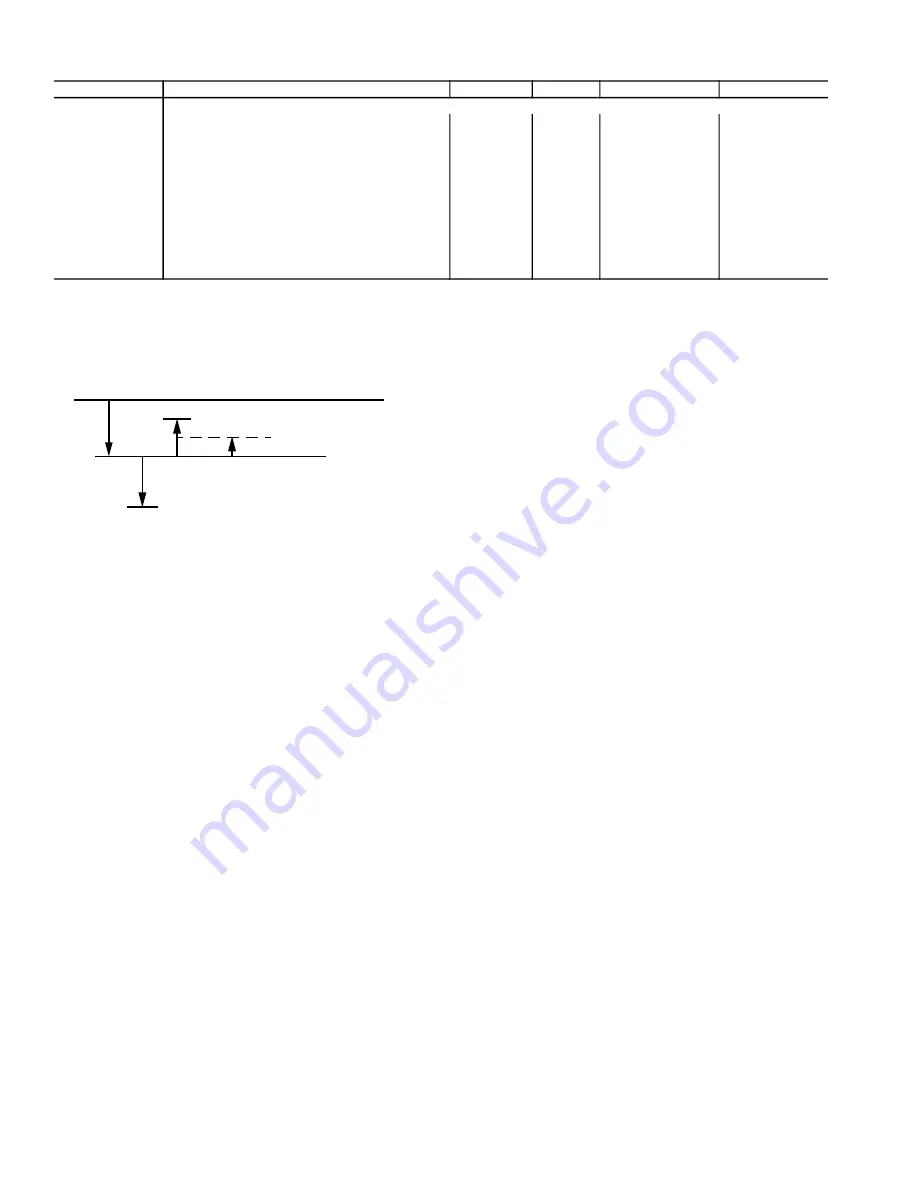
62
Table 35 —
Heat/Cool Set Point Offsets
The control will call out a low or high heat mode by comparing
the controlling temperature to the heating set point and the
heating set point offset. The set point offsets are used as addi
-
tional help in customizing and tweaking comfort into the build
-
ing space. See Fig. 9 for an example of offsets.
Fig. 9 —
Heating Offsets
Demand Level Low Heat on Offset (L.H.ON)
This is the heating set point offset below the heating set point
at which point Low Heat starts.
Demand Level High Heat on Offset (H.H.ON)
This is the heating set point offset below [the heating set point
minus
L.H.ON
] at which point high heat starts.
Demand Level Low Heat Off Offset (L.H.OF)
This is the heating set point offset above [the heating set point
minus
L.H.ON
] at which point the Low Heat mode ends.
To enter into a LOW HEAT mode, if the controlling tempera
-
ture falls below [the heating set point minus
L.H.ON
], then
HVAC mode = LOW HEAT.
To enter into a HIGH HEAT mode, if the controlling tempera
-
ture falls below [the heating set point minus
L.H.ON
minus
H.H.ON
], then HVAC mode = HIGH HEAT.
To get out of a LOW HEAT mode, the controlling temperature
must rise above [the heating set point minus
L.H.ON
plus
L.H.OF
].
To get out of a HIGH HEAT mode, the controlling temperature
must rise above [the heating set point minus
L.H.ON
plus
L.H.OF
/2].
The Run Status table in the local display allows the user to see
the exact trip points for both the heating and cooling modes
without doing the calculations.
Heat Trend Demand Level (H.T.LV)
This is the change in demand that must be seen within the time
period specified by
H.T.TM
in order to hold off a HIGH HEAT
mode regardless of demand. This is not applicable to VAV con
-
trol types (
C.TYP
=1 and 2) in the occupied period. This tech
-
nique has been referred to as “Comfort Trending.” As long as a
LOW HEAT mode is making progress in warming the space, the
control will hold off on a HIGH HEAT mode. This is relevant for
the space sensor machine control types (
C.TYP
= 4) because the
unit may transition into the occupied mode and see an immediate
and large heating demand when the set points change.
Heat Trend Time (H.T.TM)
This is the time period upon which the heat trend demand level
(
H.T.LV
) operates and may work to hold off staging or a HIGH
HEAT mode. This is not applicable to VAV control types
(
C.TYP
=1 and 2) in the occupied period. See “Heat Trend De
-
mand Level” section for more details.
HEAT MODE DIAGNOSTIC HELP
To quickly determine the current trip points for the low and
high heat modes, there is a menu in the local display which lets
the user quickly view the state of the system. This menu also
contains the cool trip points as well. See Table 31 at the local
display under
Run
Status
TRIP
.
The controlling temperature is “
TEMP
” and is in the middle of
the table for easy reference. Also, the “HVAC” mode can be
viewed at the bottom of the table.
TWO-STAGE GAS AND ELECTRIC HEAT CONTROL
(
HT.CF
= 1,2
)
If the HVAC mode is LOW HEAT:
• If electric heat is configured, then the control will request
the supply fan ON
• If gas heat is configured, then the IGC and IFO (IGC fan
output) controls the supply fan request
• The control will turn on Heat Relay 1 (
HS1
)
• If evaporator discharge temperature is less than 50°F, then
the control will turn on Heat Relay 2 (
HS2
)
NOTE: The logic for this “low heat” override is that one stage
of heating will not be able to raise the temperature of the sup
-
ply airstream sufficient to heat the space.
If the HVAC mode is HIGH HEAT:
• If electric heat is configured, then the control will request
the supply fan ON
• If gas heat is configured, then the IGC and IFO output con
-
trols the supply fan request
• The control will turn on Heat Relay 1 (
HS1
)
• The control will turn on Heat Relay 2 (
HS2
)
HYDRONIC HEATING CONTROL (
HT.CF
= 4
)
Hydronic heating in N Series units refers to a hot water or
steam coil controlled by an actuator. These actuators are com
-
municating actuators and may be field supplied. When
Config
-
uration
HEAT
HT.CF
=4, there is a thermistor array called
Temperatures
AIR.T
CCT
that is connected to the RXB,
which serves as the evaporator discharge temperature (EDT).
The leaving-air temperature (LAT) is assigned the thermistor
that is normally assigned to EDT and is located at the supply
fan housing (
Temperatures
AIR.T
SAT
).
The configurations for hydronic heating are located at the local
displays under
Configuration
HEAT
HH.CF
. See Table 36.
ITEM
EXPANSION
RANGE
UNITS
CCN POINT
DEFAULT
D.LV.T
COOL/HEAT SETPT. OFFSETS
L.H.ON
Dmd Level Lo Heat On
0 to 2
^F
DMDLHON
1.5
H.H.ON
Dmd Level(+) Hi Heat On
0.5 to 20
^F
DMDHHON
0.5
L.H.OF
Dmd Level(-) Lo Heat Off
0.5 to 2
^F
DMDLHOFF
1
L.C.ON
Dmd Level Lo Cool On
0 to 2
^F
DMDLCON
1.5
H.C.ON
Dmd Level(+) Hi Cool On
0.5 to 20
^F
DMDHCON
0.5
L.C.OF
Dmd Level(-) Lo Cool Off
0.5 to 2
^F
DMDLCOFF
1
C.T.LV
Cool Trend Demand Level
0.1 to 5
^F
CTRENDLV
0.1
H.T.LV
Heat Trend Demand Level
0.1 to 5
^F
HTRENDLV
0.1
C.T.TM
Cool Trend Time
30 to 600
sec
CTRENDTM
120
H.T.TM
Heat Trend Time
30 to 600
sec
HTRENDTM
120
HEATING SET POINT
L.H.ON
L.H.OF
L.H.OF/2
H.H.ON
68.0°F
67.5°F
66.5°F
66.0°F
Содержание WeatherExpert 48N2
Страница 135: ...135 Fig 18 48 50N Typical Power Schematic Nominal 075 Ton Unit Shown ...
Страница 136: ...136 Fig 19 48 50N Typical Power Schematic Nominal Ton 90 150 Units Shown ...
Страница 137: ...137 Fig 20 48 50N Main Base Board Input Output Connections ...
Страница 138: ...138 Fig 21 48 50N RXB EXB CEM Input Output Connections a48 9307 ...
Страница 139: ...139 Fig 22 48 50N EXV SCB Input Output Connections a48 9308 ...
Страница 140: ...140 Fig 23 48N Typical Modulating Gas Heat Unit Control Wiring ...
Страница 141: ...141 Fig 24 50N Typical Electric Heat Unit Control Wiring ...
Страница 144: ...144 Fig 27 48N Typical Gas Heat Section Wiring Nominal Ton 120 to 150 Units ...
Страница 145: ...145 Fig 28 48 50N Typical Power Component Control Wiring 460 v ...
Страница 146: ...146 Fig 29 48 50N Component Control Wiring 575 v Nominal Ton 075 to 150 Units ...
Страница 147: ...147 Fig 30 48 50N Component Arrangement Power Box ...
Страница 148: ...148 Fig 31 48 50N Component Arrangement Control Box ...
Страница 168: ...168 Fig 47 Sensor and Ignition Position Fig 48 Combustion Blower Details SENSOR DETAILS IGNITION DETAILS ...
Страница 240: ...240 APPENDIX D VFD INFORMATION CONT Fig G VFD Bypass Wiring Diagram WHEN USED ...