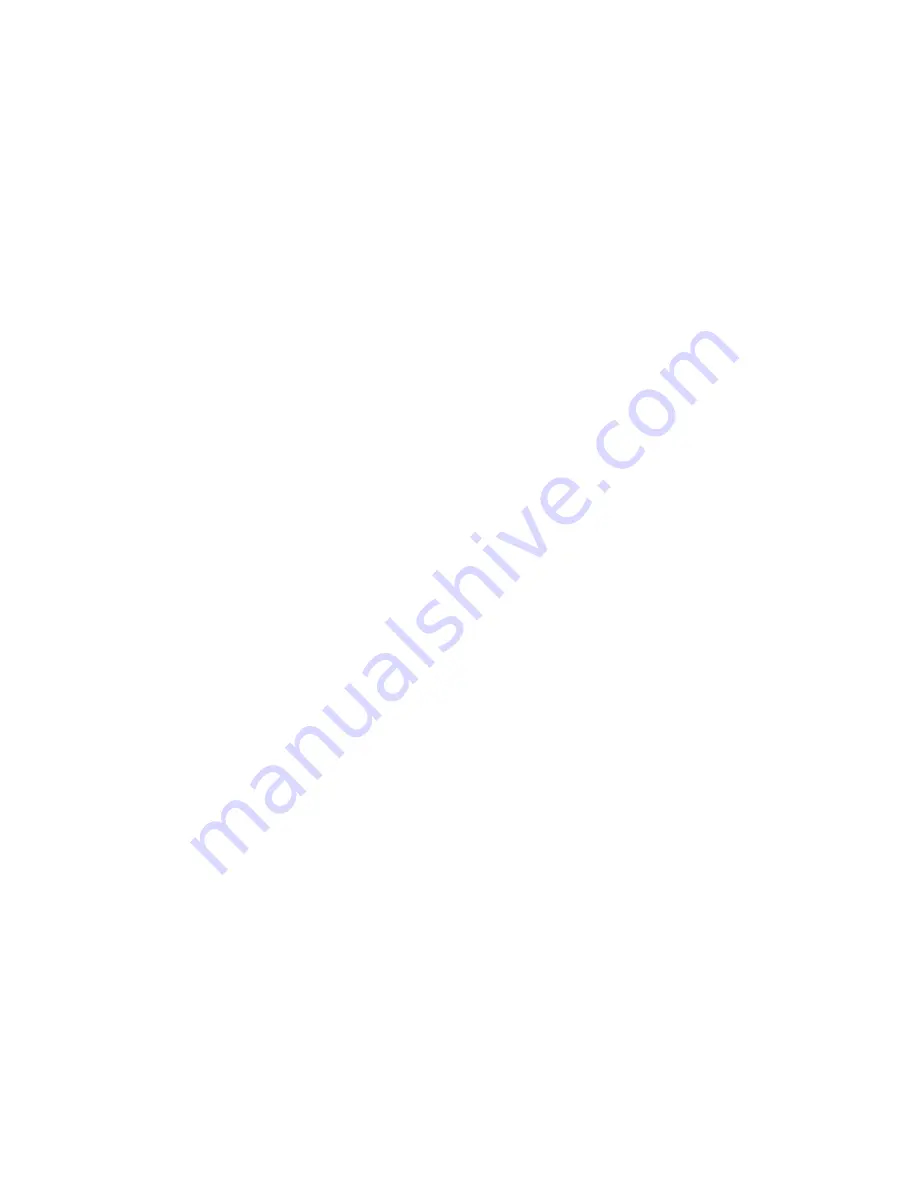
47
capacity reduction. This ramped reduction is only imposed on
a decrease in digital scroll capacity. An increase in capacity
will continue to follow the values defined by
Configuration
DS.AP
and
Configuration
DS.AD
.
Dig Scroll Max Only OAT (DS.MO)
This configuration defines the outdoor-air temperature above
which the digital scroll will not be allowed to modulate. The
digital scroll will be locked at 100% above this outdoor-air
temperature.
Min Load Valve Enable (MLV)
This configuration instructs the control as to whether a mini
-
mum load (hot gas bypass) valve has been installed and will be
controlled by the compressor staging routine.
High SST Alert Delay Time (H.SST)
This option allows the low saturated suction temperature alert
timing delay to be adjusted.
Reverse Rotation Verified? (RR.VF)
This configuration is used to enable or disable the compressor
reverse rotation detection algorithm. This algorithm performs a
check for correct compressor rotation upon power up of the
unit. The method for detecting correct rotation is based on the
assumption that there will be a drop in suction pressure upon a
compressor start if it is rotating in the correct direction.
A test is made once, on power up, for suction pressure change
on the first compressor of the first circuit to start.
Reverse rotation is determined by measuring suction pressure
at 3 points in time:
• 5 seconds prior to compressor start.
• At the instant the compressor starts.
• 5 seconds after the compressor starts.
The rate of suction pressure change from 5 seconds prior to
compressor start to compressor start (rate prior) is compared to
the rate of suction pressure change from compressor start to
5 seconds after compressor start (rate after). If (rate after) is
less than (rate prior minus 1.25), alarm A140 is generated. This
alarm will disable mechanical cooling and will require a manu
-
al reset. It is important to note that in Service Test mode, re
-
verse rotation is checked on every compressor start.
Once it has been verified that power to the unit and compres
-
sors has been applied correctly and the compressors start up
normally, this configuration can be set to YES to disable the re
-
verse rotation check.
Use CSBs for HPS detect? (CS.HP)
On units with multiple compressors running on a circuit, the
Current Sensor Boards are used to help detect a High Pressure
Switch trip. Setting this configuration to NO disables this addi
-
tional High Pressure switch trip detection.
The parameters in the next 3 subsets, EXV Circuit Configs
(
EXV.C
). EXV PID Configs (
E.PID
) and DP Override Configs
(
DP.OC
) all deal with the EXC control parameters. These con
-
figurations should not be adjusted in the field. Adjustment
could cause unstable EXV control resulting in head pressure
trips, and /or compressor flooding.
Enab Cir Shtdwn w/ flood (EN.SC)
This configuration enables circuit shutdown when flooding is
detected.
Comp. Cir. Exv. Min Pos% (EX.MN)
This configuration sets the allowable commanded EXV mini
-
mum position. Factory default is 20%. Normal adjustment
range is 10 to 20%. Adjustment below this range could cause
excessive head pressure alerts/alarms. Adjustment above this
range could cause excessive flooding alerts and circuit shut
-
downs. See Troubleshooting section for more information.
NOTE: The actual value for EXV MIN POS% used during
runtime is
C.XMP
. In most cases
C.XMP
=
EX.MN
. If OAT <
LOWOAT,
C.XMP
=
EX.MN
/2. This allows the EXV to close
more at lower outdoor temperatures.
Flooding Detect Time (FL.TM)
This configuration sets the amount of time that the superheat
must be below the flooding control set point (
C.FLS
), while
the EXV is within 1% of the minimum position (
EX.MN
) be
-
fore a flooding alert is logged and the circuit is restarted if
EN.SC
=YES. Flooding shall be detected as follows:
1. If the EXV is being commanded by the PID.
2. Superheat is less than
C.FLS
for
FL.TM
consecutive
seconds.
3. EXV position is within 1% of the minimum position
(
EX.MN
).
The control shall monitor the superheat of each EXV and log
an alert if flooding is detected.
If
EN.SC
=NO, after logging the flooding alert, the circuit shall
continue to run. The alert shall be automatically cleared when:
1. The EXV is being commanded by the PID.
2. Superheat is greater than
C.FLS
for
FL.TM
consecutive
seconds.
If
EN.SC
=YES, after logging the flooding alert, the circuit
shall be marked as failed, forcing a circuit shutdown and recal
-
ibration of the shutdown circuit EXVs. The alert shall be auto
-
matically cleared
FL.TM
after being set. After clearing the
alert, the circuit shall be immediately marked as usable.
Shutdown due to a flooding alert will not shut down both cir
-
cuits at the same time. A second circuit waits for the alert to
automatically clear on the first circuit before shutting down.
The unit will not automatically restart the compressors after the
detection of flooding with a circuit reset, while in Service Test
mode the operator has to manually restart any compressors.
COOL MODE SELECTION PROCESS
The N Series
Comfort
Link controls offer 3 distinct methods by
which they may select a cooling mode.
1. Thermostat (
C.TYP
=3): The thermostat does not depend
upon the state of occupancy or temperature and the modes
are called out directly by the discrete inputs
(
Inputs
STAT
Y1
and
Y2
).
2. VAV cooling types (
C.TYP
=1 and 2) are called out in the
occupied period (
Operating Modes
MODE
OCC
=ON).
3. VAV cooling types (
C.TYP
=1 and 2) are called out in the
unoccupied period (
Operating Modes
MODE
OCC
=
OFF). They are also used for space sensor control types
(
C.TYP
=4) in both the occupied and unoccupied periods.
This section is devoted to the process of cooling mode determi
-
nation for the 3 types outlined above. See Tables 28 and 29.
Содержание WeatherExpert 48N2
Страница 135: ...135 Fig 18 48 50N Typical Power Schematic Nominal 075 Ton Unit Shown ...
Страница 136: ...136 Fig 19 48 50N Typical Power Schematic Nominal Ton 90 150 Units Shown ...
Страница 137: ...137 Fig 20 48 50N Main Base Board Input Output Connections ...
Страница 138: ...138 Fig 21 48 50N RXB EXB CEM Input Output Connections a48 9307 ...
Страница 139: ...139 Fig 22 48 50N EXV SCB Input Output Connections a48 9308 ...
Страница 140: ...140 Fig 23 48N Typical Modulating Gas Heat Unit Control Wiring ...
Страница 141: ...141 Fig 24 50N Typical Electric Heat Unit Control Wiring ...
Страница 144: ...144 Fig 27 48N Typical Gas Heat Section Wiring Nominal Ton 120 to 150 Units ...
Страница 145: ...145 Fig 28 48 50N Typical Power Component Control Wiring 460 v ...
Страница 146: ...146 Fig 29 48 50N Component Control Wiring 575 v Nominal Ton 075 to 150 Units ...
Страница 147: ...147 Fig 30 48 50N Component Arrangement Power Box ...
Страница 148: ...148 Fig 31 48 50N Component Arrangement Control Box ...
Страница 168: ...168 Fig 47 Sensor and Ignition Position Fig 48 Combustion Blower Details SENSOR DETAILS IGNITION DETAILS ...
Страница 240: ...240 APPENDIX D VFD INFORMATION CONT Fig G VFD Bypass Wiring Diagram WHEN USED ...