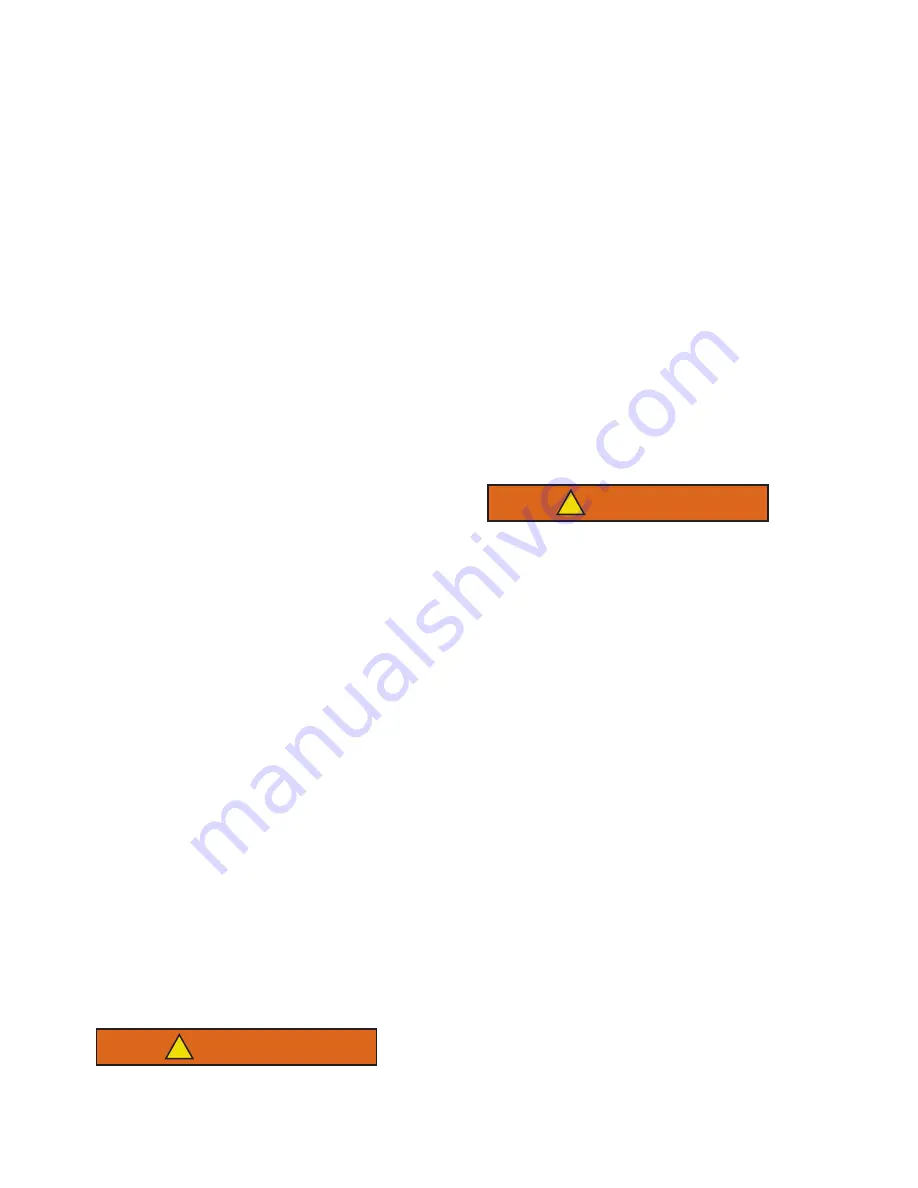
62-11637
8–28
8.8
COMPRESSOR AND UNLOADER SERVICE
8.8.1
Repair or Replacement Determination
Certain operating conditions or refrigeration system
components may be misdiagnosed and subsequently
lead to the determination that the compressor requires
replacement. These conditions or components should
be checked prior to replacing a compressor and after a
replacement compressor is installed to prevent replace-
ment compressor damage. To determine if compressor
replacement or repair is required, do the following:
1. If the compressor is operational, check the
refrigerant charge, refer to
.
2. If the compressor is operational, check opera-
tion of the unloaders, refer to
.
3. If the compressor is operational, check the sys-
tem components as follows:
a. Install gauges to allow reading of receiver, suc-
tion and discharge pressure. See
b. Start the unit in cooling so that compressor
operates.
c. Frontseat liquid line service valve. shutdown unit
when suction pressure drops to 2 psig (0.2 bar).
d. Monitor the gauges. If receiver pressure drops
rapidly and the suction and discharge pressures
rise rapidly the liquid line service valve or
bypass check valve require replacement before
the compressor can be further tested.
e. Backseat the liquid line service valve and restart
the unit. Slowly frontseat the suction service
valve. shutdown the unit when the suction pres-
sure drops to 2 psig (0.2 bar).
f. Monitor the gauges. If the suction and discharge
pressures do not equalize rapidly, the compres-
sor is not at fault.
4. Check condition of and repair cylinder heads
8.8.2
Removal and Replacement of Compressor
1. Pumpdown the compressor or remove charge,
refer to
2. Ensure unit will not start automatically by dis-
abling any two way communication and placing
the STOP/RUN-OFF switch in the OFF position.
3. Disconnect negative battery connection.
Remove battery if required.
4. Remove any interfering equipment attached to
the end flange (see
).
WARNING
!
Do not unscrew service valve mounting
capscrews all the way before breaking seal.
Entrapped pressure could result in injury.
5. Loosen the suction and discharge service valve
mounting bolts. Tap the valve bodies to break
the seal and then remove bolts.
6. Disconnect all low voltage connectors (UL1,
UL2, CDT, CDP & HPS).
7. Loosen lower belt idler and remove belt from
gearbox, Belt may be removed with, and rein-
stalled with, the compressor.
8. Block up the engine and remove compressor
shockmount bolts.
9. Remove the 12 end flange bolts and lock wash-
ers. Attach a sling or other device to compressor
(refer to
for weight of compressor).
Slide compressor sufficient to disengage com-
pressor drive gear from nylon drive gear.
Remove compressor.
10. Inspect nylon drive gear for wear or sharp
edges. Replace if required.
11. Remove oil from compressor for shipping. Test
for acidity If acid is present a system cleanup
may be necessary.
WARNING
!
Do not unscrew replacement compressor
lifting eyelet/blankoff plate mounting cap-
screws all the way before breaking seal.
Entrapped pressure could result in injury.
12. Loosen the suction and discharge lifting eyelet/
blankoff plate mounting bolts. Tap the center of
the blankoff plates to break the seal and then
remove bolts, plates and gaskets.
13. If required add oil to the replacement compres-
sor. Add only 5.0 pints (2.4 liters) of oil when first
adding oil to the compressor. This procedure is
designed to compensate for excess oil that may
have migrated with refrigerant to other parts of
the system during unit operation.
14. Exchange all external compressor components
such as: the unloader coils; discharge and suc-
tion strainers; switches, transducers, tempera-
ture sensors, fittings and compressor drive gear.
15. Install blankoff plates and plugs in original com-
pressor for shipment.
16. Remove any remaining old gasket material from
the discharge and suction service valve sealing
surfaces.
17. Ensure belt is in end plate opening and around
drive gear. Ensure correct alignment of com-
pressor drive gear & nylon gear as compressor
is installed in unit. Use new lock nuts when
replacing compressor shockmounts. See
for mounting bolt torque information.
18. Reconnect all wiring per wiring schematic.
Содержание Transicold X4 7300
Страница 21: ...62 11637 1 6 1 3 SAFETY DECALS ...
Страница 22: ...1 7 62 11637 62 03958 ...
Страница 23: ...62 11637 1 8 ...
Страница 24: ...1 9 62 11637 ...
Страница 119: ...62 11637 SECTION 6 MESSAGECENTER PARAGRAPH NUMBER Page 6 1 MESSAGECENTER MESSAGES 6 1 ...
Страница 278: ......