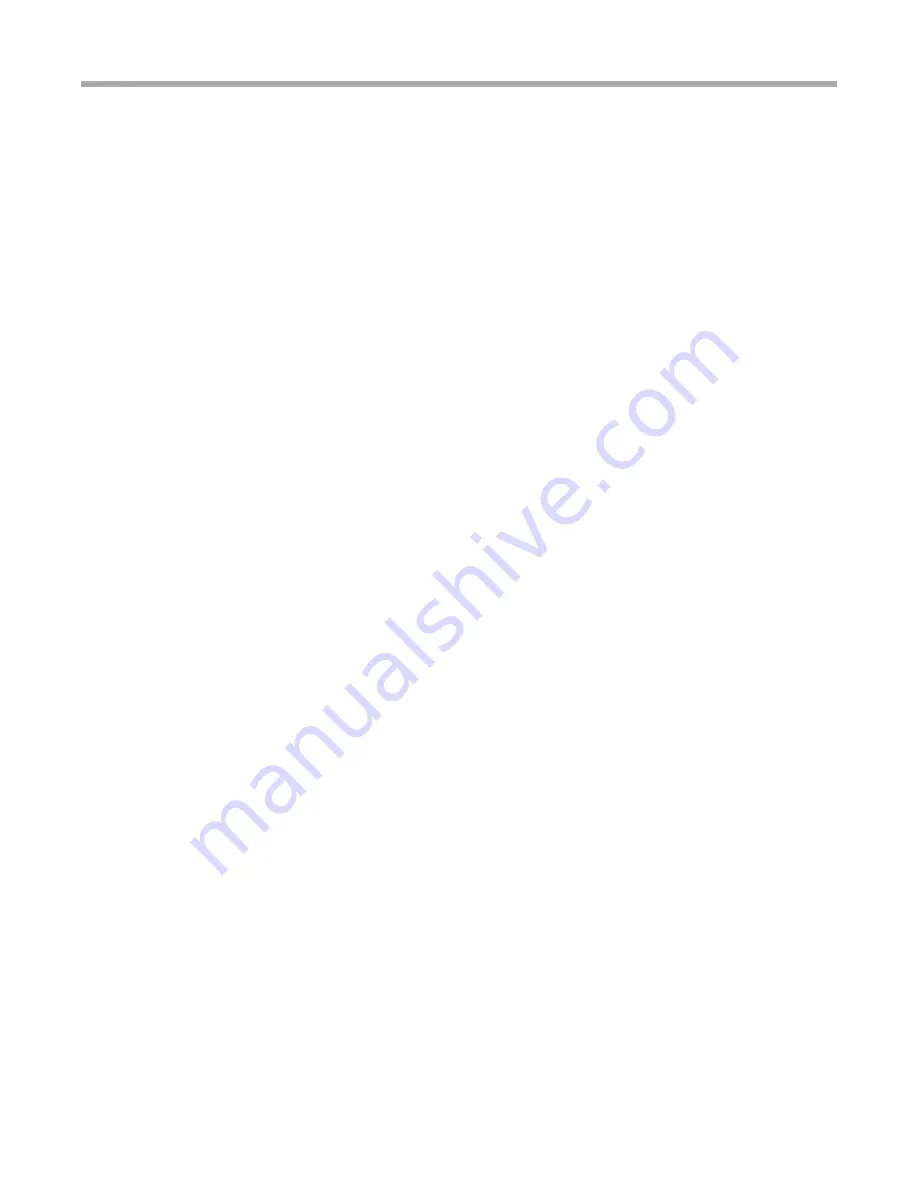
9
R e s i d e n t i a l S p l i t - 6 0 H z R 2 2 & R 4 1 0 A
R e v. : 5 J u n e , 2 0 0 8
C a r r i e r : Tu r n t o t h e E x p e r t s
Installation
NOTICE!
Failure to remove shipping brackets from spring-
mounted compressors will cause excessive noise, and could
cause component failure due to added vibration.
The installation of water source heat pump units and all
associated components, parts and accessories which make
up the installation shall be in accordance with the regulations
of ALL authorities having jurisdiction and MUST conform to
all applicable codes. It is the responsibility of the installing
contractor to determine and comply with ALL applicable
codes and regulations.
Removing Existing Condensing Unit (Where Applicable)
1. Pump down condensing unit. Close the liquid line
service valve of existing condensing unit and start
compressor to pump refrigerant back into compressor
section. Then, close suction service valve while
compressor is still running to trap refrigerant in outdoor
section. Immediately kill power to the condensing unit.
2. Disconnect power and low voltage and remove old
condensing unit. Cut or unbraze line set from unit.
Remove condensing unit.
3. If condensing unit is not operational or will not pump
down, refrigerant should be recovered using appropriate
equipment.
4. Replace line set, especially if upgrading system from R-
22 to R-410A refrigerant. If line set cannot be replaced,
it must be thoroughly
fl
ushed before installing new
compressor section. R-410A compressors use POE
oil instead of mineral oil (R-22 systems). Mineral oil is
not compatible with POE oil, and could cause system
damage if not completely
fl
ushed from the line set.
“Indoor” Compressor Section Location
Both “indoor” and “outdoor” versions of the geothermal split
system compressor section are available. “Indoor” version
is not designed for outdoor installation. Locate the unit
in an INDOOR area that allows enough space for service
personnel to perform typical maintenance or repairs without
removing unit. Units are typically installed in a mechanical
room or closet. Never install units in areas subject to freezing
or where humidity levels could cause cabinet condensation
(such as unconditioned spaces subject to 100% outside air).
Consideration should be given to access for easy removal
of service access panels. Provide suf
fi
cient room to make
water, electrical, and line set connections.
Any access panel screws that would be dif
fi
cult to remove
after the unit is installed should be removed prior to setting
the unit. Refer to Figure 2 for an illustration of a typical
installation. Refer to “Physical Dimensions” section for
dimensional data. Conform to the following guidelines when
selecting unit location:
1. Install the unit on a piece of rubber, neoprene or other
mounting pad material for sound isolation. The pad should
be at least 3/8” [10mm] to 1/2” [13mm] in thickness.
Extend the pad beyond all four edges of the unit.
2. Provide adequate clearance for maintenance and
service. Do not block access panels with piping, conduit
or other materials.
3. Provide access for servicing the compressor and coils
without removing the unit.
4. Provide an unobstructed path to the unit within the
closet or mechanical room. Space should be suf
fi
cient to
allow removal of the unit, if necessary.
5. In limited side access installations, pre-removal of the
control box side mounting screws will allow control box
removal for future servicing (R22 units only).
6. Provide access to water valves and
fi
ttings and
screwdriver access to the unit side panels and all
electrical connections.
“Outdoor” Compressor Section Loacation
Locate the unit in an outdoor area that allows easy loop
and lineset access and also has enough space for service
personnel to perform typical maintenance or repairs. The
“outdoor” compressor section is usually installed on a
condensor pad directly outside the lineset access into the
building. The service valve side can be located toward
the building, keeping the loop access end away from the
building. Conform to the following guidelines when selecting
unit location:
1. Provide adequate access for loop trench excavation.
2. Locate unit directly outside lineset penetration if possible.
Utilize existing condensor pad where possible.
3. Provide access for servicing and maintenance.
“Outdoor” compressor section may be mounted on a
vibration isolation pad with loop access hole as shown in
Figure 3. When mounting on an existing concrete condenser
pad, 3” [76mm] holes should be bored through the pad to
accomodate the pipe (1-1/4” - 32mm) and insulation (1/2”
[13mm] wall thickness). Figure 3 illustrates location and
dimensions of the holes required.
Air Handler Installation
This manual speci
fi
cally addresses the compressor section
of the system. Air handler location and installation should
be according to the instructions provided with the air
handling unit.
Содержание GT-GS Indoor Split Series
Страница 2: ......
Страница 49: ...49 Residential Split 60Hz R22 R 410A Rev 5 June 2 0 0 8 Carrier Turn to the Experts...