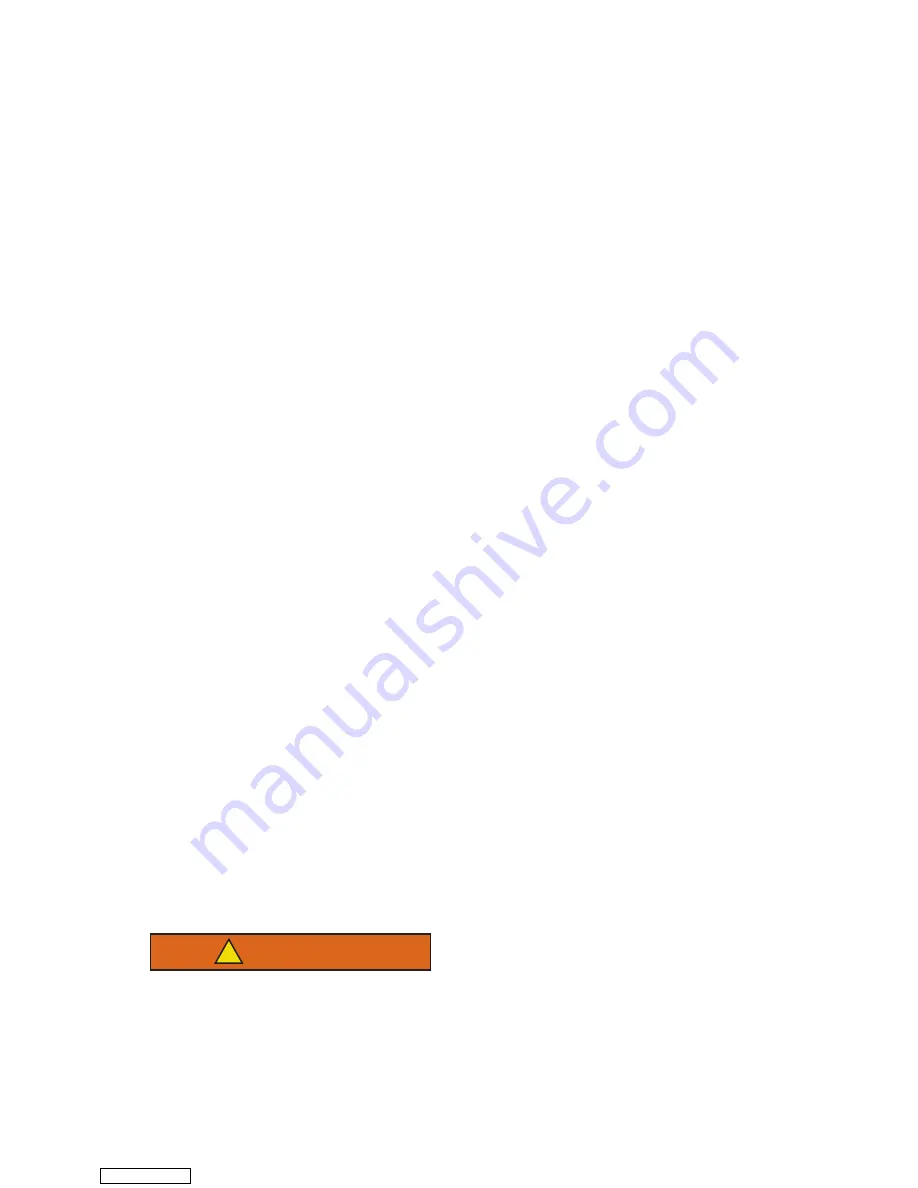
7–3
T-368
Removing the Manifold Gauge Set:
a. While the compressor is still ON, backseat the
high side service valve.
b. Midseat both hand valves on the manifold
gauge set and allow the pressure in the mani-
fold gauge set to be drawn down to suction
pressure. This returns any liquid that may be in
the high side hose to the system.
c. Backseat the suction service valve. Backseat
both field service couplings and frontseat both
manifold set valves. Remove the couplings from
the service ports.
d. Install both service valve stem caps and service
port caps (finger-tight only).
7.4
PUMP THE UNIT DOWN
To service the filter-drier, moisture-liquid indicator,
expansion valve, suction modulation valve, quench
valve, or evaporator coil, pump the refrigerant into the
high side as follows:
a. Attach manifold gauge set to compressor ser-
vice valves (refer to
b. Start the unit and run in a cooling mode for 10 to
15 minutes. Frontseat the liquid line service
valve. Place start-stop switch in the OFF posi-
tion when the suction reaches a positive pres-
sure of 0.1kg/cm
2
(1.0psig).
c. Frontseat the suction service valve. The refriger-
ant will be trapped between the compressor
suction service valve and the liquid line valve.
d. Before opening up any part of the system, a slight
positive pressure should be indicated on the pres-
sure gauge. If a vacuum is indicated, emit refrig-
erant by cracking the liquid line valve momentarily
to build up a slight positive pressure.
e. When opening up the refrigerant system, certain
parts may frost. Allow the part to warm to ambient
temperature before dismantling. This avoids internal
condensation, which puts moisture in the system.
f. After repairs have been made, be sure to per-
form a refrigerant leak check (refer to
), and evacuate and dehydrate the low side
(refer to
).
g. Check refrigerant charge (refer to
).
7.5
REFRIGERANT LEAK CHECKING
WARNING
!
EXPLOSION HAZARD: Failure to follow
this WARNING can result in death, serious
personal injury and / or property damage.
Never use air or gas mixtures containing
oxygen (O
2
) for leak testing or operating
the product.
Charge Only With R
−
134a: Refrigerant
must conform to AHRI Standard 700
specification.
a. The recommended procedure for finding leaks
in a system is with a R-134a electronic leak
detector. Testing joints with soapsuds is satis-
factory only for locating large leaks.
b. If the system is without refrigerant, charge the
system with refrigerant 134a to build up pres-
sure between 2.1 to 3.5kg/cm
2
(30 to 50psig).
Remove refrigerant cylinder and leak-check all
connections.
NOTE
Only refrigerant 134a should be used to pres-
surize the system. Any other gas or vapor will
contaminate the system, which will require addi-
tional purging and evacuation of the system.
c. If required, remove refrigerant using a refriger-
ant recovery system and repair any leaks.
d. Evacuate and dehydrate the unit (refer to
).
7.6
EVACUATION AND DEHYDRATION
7.6.1
General
Moisture is the deadly enemy of refrigeration systems.
The presence of moisture in a refrigeration system can
have many undesirable effects. The most common are
copper plating, acid sludge formation, “freezing-up” of
metering devices by free water, and formation of acids,
resulting in metal corrosion.
7.6.2
Preparation
a. Evacuate and dehydrate only after pressure
leak test (refer to
b. Essential tools to properly evacuate and dehy-
drate any system include a vacuum pump (8m-/
hr = 5cfm volume displacement) and an elec-
tronic vacuum gauge. The pump is available
from Carrier Transicold, P/N 07-00176-11. The
micron gauge is P/N 07
−
00414
−
00.
c. If possible, keep the ambient temperature above
15.6°C (60°F) to speed evaporation of moisture. If
the ambient temperature is lower than 15.6°C
(60°F), ice might form before moisture removal is
complete. Heat lamps or alternate sources of heat
may be used to raise the system temperature.
d. Additional time may be saved during a complete
system pump down by replacing the filter-drier
with a section of copper tubing and the appropri-
ate fittings. Installation of a new drier may be
performed during the charging procedure.
Downloaded from
Содержание 69NT40-541-505
Страница 2: ...Downloaded from ManualsNet com search engine...
Страница 4: ...Downloaded from ManualsNet com search engine...
Страница 10: ...Downloaded from ManualsNet com search engine...
Страница 14: ...Downloaded from ManualsNet com search engine...
Страница 18: ...Downloaded from ManualsNet com search engine...
Страница 80: ...Downloaded from ManualsNet com search engine...
Страница 86: ...Downloaded from ManualsNet com search engine...
Страница 92: ...Downloaded from ManualsNet com search engine...
Страница 124: ...Downloaded from ManualsNet com search engine...
Страница 125: ...Downloaded from ManualsNet com search engine...
Страница 126: ...Downloaded from ManualsNet com search engine...
Страница 142: ...Downloaded from ManualsNet com search engine...