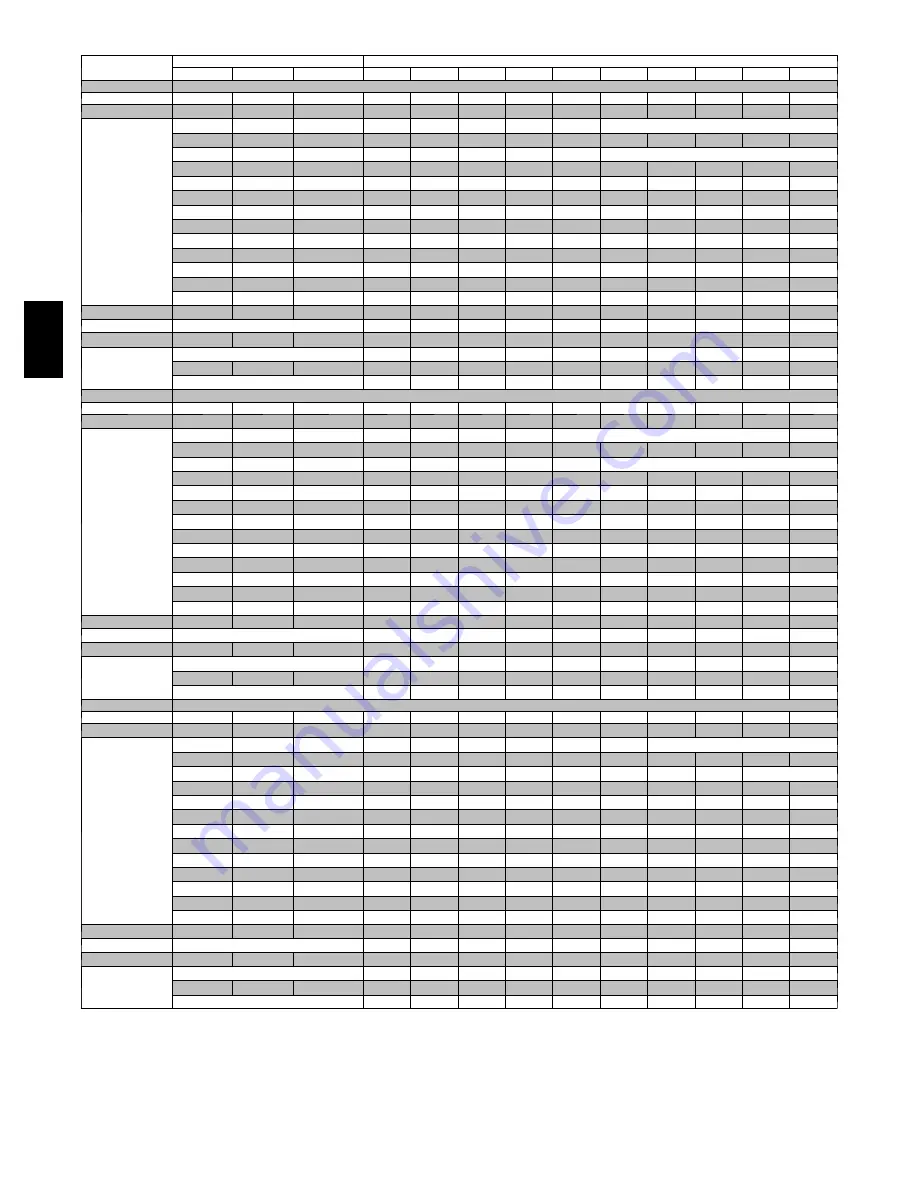
32
Table 9
---
Cooling
4
and Heating Air Delivery -- CFM (Bottom Return
5
with Filter) (Con’t)
Unit Size
Cooling Switch Settings
External Static Pressure (ESP)
SW2-8
SW2-7
SW2-6
0.1
0.2
0.3
0.4
0.5
0.6
0.7
0.8
0.9
1.0
060---14
Clg Default:
OFF
OFF
OFF
1330
1295
1260
1220
1190
1150
1110
1075
1045
1005
Cooling (SW2)
OFF
OFF
ON
725
660
600
520
435
See note 4
OFF
ON
OFF
780
725
660
615
540
See note 4
OFF
ON
ON
975
925
875
835
785
750
690
655
610
570
ON
OFF
OFF
1160
1120
1090
1045
1010
970
920
885
840
800
ON
OFF
ON
1330
1295
1260
1220
1190
1150
1110
1075
1045
1005
ON
ON
OFF
1705
1650
1595
1545
1475
1415
1340
1275
1200
1105
ON
ON
ON
1705
1650
1595
1545
1475
1415
1340
1275
1200
1105
Clg SW2:
Maximum Clg Airflow
2
1705
1650
1595
1545
1475
1415
1340
1275
1200
1105
Heating
(SW1)
High Heat Airflow
3
1145
1105
1075
1030
995
955
905
870
825
785
Low Heat Airflow
3
870
820
760
720
655
620
560
525
470
435
080---16
Clg Default:
OFF
OFF
OFF
1805
1765
1720
1665
1610
1540
1475
1400
1315
1235
Cooling (SW2)
OFF
OFF
ON
775
635
455
230
See note 8
OFF
ON
OFF
840
740
675
625
555
See note 4
OFF
ON
ON
995
955
910
860
815
770
720
660
620
585
ON
OFF
OFF
1175
1140
1090
1060
1025
980
940
905
855
815
ON
OFF
ON
1325
1280
1245
1210
1180
1140
1105
1070
1025
990
ON
ON
OFF
1545
1515
1480
1445
1410
1380
1350
1315
1245
1175
ON
ON
ON
1805
1765
1720
1665
1610
1540
1475
1400
1315
1235
Clg SW2:
Maximum Clg Airflow
2
1805
1765
1720
1665
1610
1540
1475
1400
1315
1235
Heating
(SW1)
High Heat Airflow
3
1520
1490
1455
1420
1385
1355
1320
1285
1220
1155
Low Heat Airflow
3
1180
1145
1095
1065
1030
985
945
910
860
820
080--20
Clg Default:
OFF
OFF
OFF
1905
1870
1825
1785
1750
1700
1665
1625
1560
1460
Cooling (SW2)
OFF
OFF
ON
950
770
620
515
440
365
See note 4
OFF
ON
OFF
1015
935
880
825
765
690
625
580
See note 4
OFF
ON
ON
1155
1105
1040
990
920
875
815
755
710
645
ON
OFF
OFF
1335
1290
1245
1190
1145
1085
1040
990
930
890
ON
OFF
ON
1520
1485
1435
1390
1340
1300
1255
1200
1160
1115
ON
ON
OFF
1905
1870
1825
1785
1750
1700
1665
1625
1560
1460
ON
ON
ON
2290
2230
2160
2085
2005
1915
1820
1730
1640
1525
Clg SW2:
Maximum Clg Airflow
2
2290
2230
2160
2085
2005
1915
1820
1730
1640
1525
Heating
(SW1)
High Heat Airflow
3
1575
1535
1485
1445
1400
1350
1310
1260
1215
1170
Low Heat Airflow
3
1230
1170
1125
1065
1015
955
900
855
795
755
NOTE
: See notes at end of table.
59TP6A