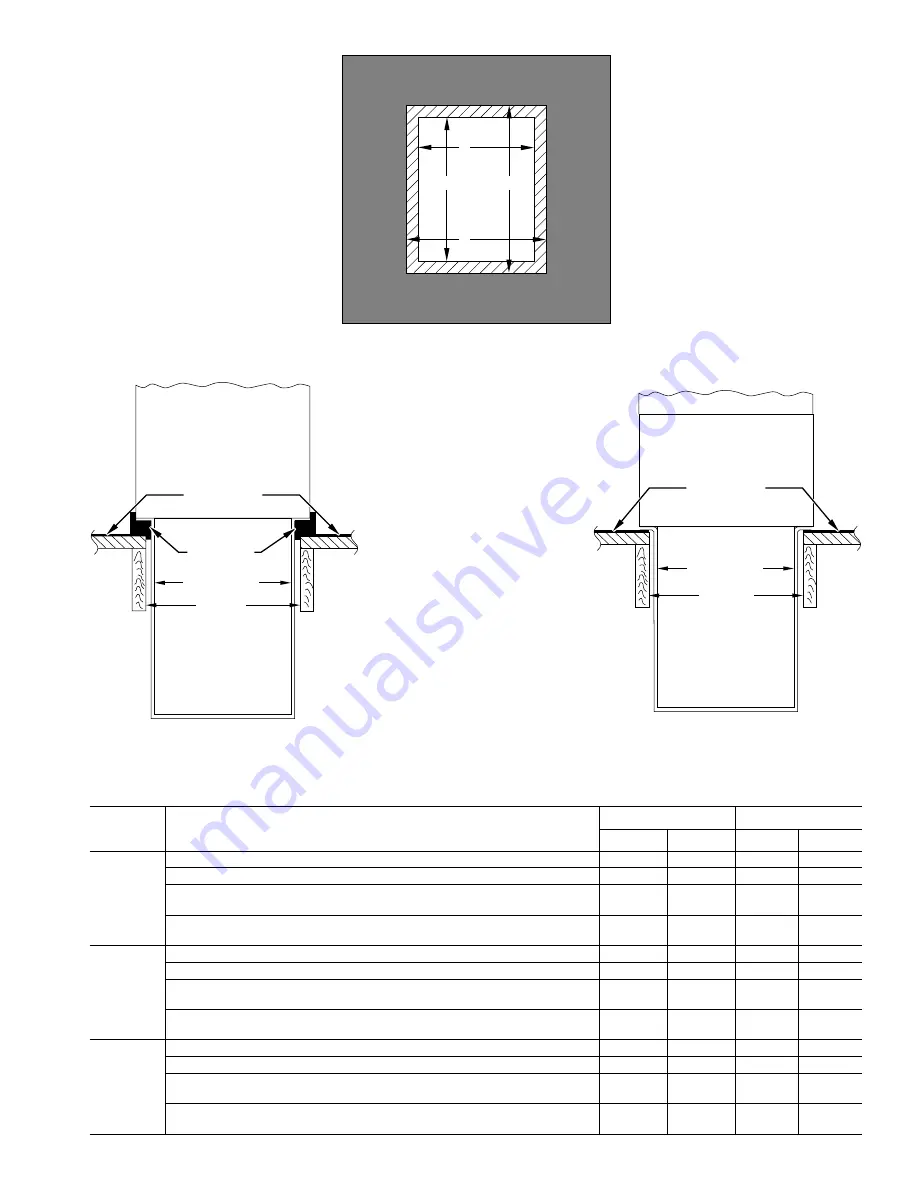
Table 1—Opening Dimensions (In.)
FURNACE
CASING
WIDTH
APPLICATION
PLENUM OPENING
FLOOR OPENING
A
B
C
D
17-1/2
Upflow Applications
16
24-1/8
16-5/8
24-3/4
Downflow Applications on Non-Combustible Flooring
15-7/8
19
16-1/2
19-5/8
Downflow Applications on Combustible Flooring Using KGASB Subbase
Furnace with or without CD5 or CK5 Coil Assembly or KCAKC Coil Box
15-1/8
19
16-3/4
20-3/8
Downflow Applications on Combustible Flooring NOT Using KGASB Subbase
Furnace with CD5 or CK5 Coil Assembly or KCAKC Coil Box
15-1/2
19
16-1/2
20
21
Upflow Applications
19-1/2
24-1/8
20-1/8
24-3/4
Downflow Applications on Non-Combustible Flooring
19-3/8
19
20
19-5/8
Downflow Applications on Combustible Flooring Using KGASB Subbase
Furnace with or without CD5 or CK5 Coil Assembly or KCAKC Coil Box
18-5/8
19
20-1/4
20-3/8
Downflow Applications on Combustible Flooring NOT Using KGASB Subbase
Furnace with CD5 or CK5 Coil Assembly or KCAKC Coil Box
19
19
20
20
24-1/2
Upflow Applications
23
24-1/8
23-5/8
24-3/4
Downflow Applications on Non-Combustible Flooring
22-7/8
19
23-1/2
19-5/8
Downflow Applications on Combustible Flooring Using KGASB Subbase
Furnace with or without CD5 or CK5 Coil Assembly or KCAKC Coil Box
22-1/8
19
23-3/4
20-3/8
Downflow Applications on Combustible Flooring NOT Using KGASB Subbase
Furnace with CD5 or CK5 Coil Assembly or KCAKC Coil Box
22-1/2
19
23-1/2
20
Fig. 14—Furnace, Plenum, and Subbase
Installed on a Combustible Floor
A96285
DOWNFLOW
SUBBASE
SHEET METAL
PLENUM
FLOOR
OPENING
FURNACE
(OR COIL CASING
WHEN USED)
COMBUSTIBLE
FLOORING
Fig. 13—Floor and Plenum Opening Dimensions
A96283
PLENUM
OPENING
C
A
B
D
FLOOR
OPENING
Fig. 15—Furnace, Plenum, and Coil
Assembly or Coil Box Installed
on a Combustible Floor
A96284
CD5 OR CK5
COIL ASSEMBLY
OR KCAKC
COIL BOX
FURNACE
SHEET METAL
PLENUM
FLOOR
OPENING
COMBUSTIBLE
FLOORING
15