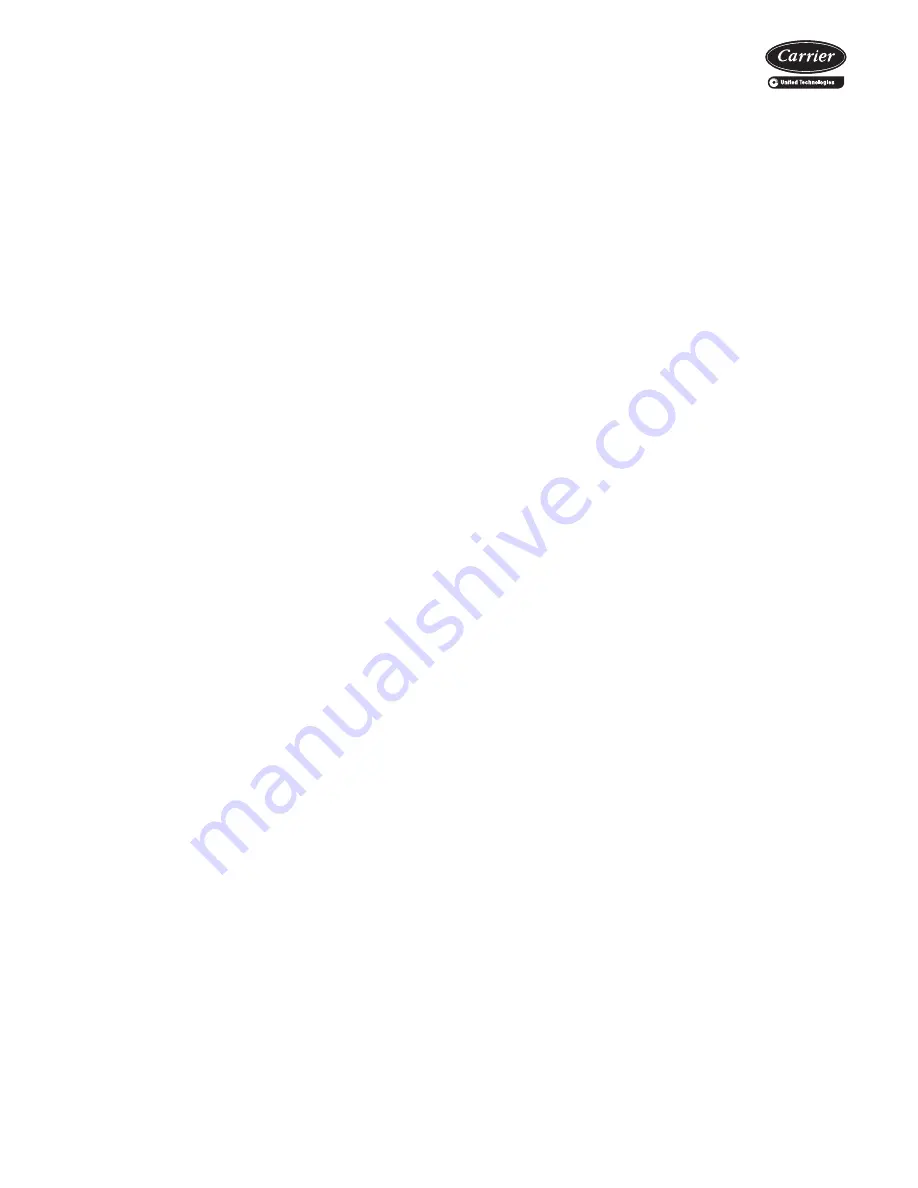
18
Vertical Packaged Terminal Air Conditioners
HVAC Guide Specifications — 52V
Size Range:
9,000 to 24,000 Nominal Btuh
Carrier Model Numbers:
52VCR (Cooling Only with R-410A Refrigerant)
52VER (Cooling with Electric Heat and
R-410A Refrigerant)
52VQR (Heat Pump with R-410A Refrigerant)
52VWR (Cooling with Hot Water Heat and
R-410A Refrigerant)
Part 1 — General
1.01 SYSTEM DESCRIPTION
Packaged, self-contained, vertical through-the-wall
air-cooled terminal heat pump with electric heat,
straight cool with electric heat, or straight cool with
hot water heat unit. Available with wall sleeve, room
cabinet, electric refrigeration system, electric heat-
ing, outside-air grille. Fully charged with R-410A
refrigerant and filled with oil.
1.02 QUALITY ASSURANCE
System shall be approved and certified by UL. Chas-
sis capacity and efficiency performance shall be
rated in accordance with AHRI Standard 390, latest
edition.
Part 2 — Products
2.01 EQUIPMENT
A. Electrical Characteristics:
1. Refer to schedule on drawings for electrical
characteristics.
2. Disconnect switch shall be factory-installed on
equipment.
B. Cabinet:
Cabinet shall be constructed of 20 gage galvanized
steel, with removable front and side panels. Shall be
fully insulated for sound attenuation and reduced air
infiltration. Adjustable fresh air shall be available to
meet code requirements for fresh air introduction.
Removable front panels shall be provided for access
to controls and unit.
C. Refrigeration System:
1. Direct expansion refrigeration cooling coil shall
have
3
/
8
-in. OD high-efficiency rifled copper
tubes mechanically bonded to high-efficiency
aluminum fins. All coils shall be factory leak
tested at 350 psig.
2. Hermetically sealed compressor with internal
spring isolation, external isolation, permanent
split capacitor motor and overload protection.
3. Accumulator (heat pump only).
4. Condenser coil and fan.
D. Air System:
Air system shall have centrifugal forward-curved
evaporator fans with three-speed permanent split
capacitor motor, optional filter grille.
E. Heating Coil:
1. Electric heating coil shall be 2 to 10 kW
electric.
2. Hot water heating coil shall have
3
/
8
-in. OD
high-efficiency rifled copper tubes mechanically
bonded to high-efficiency aluminum fins. All
coils shall be factory leak tested at 350 psig.
F. Condensate Drain:
Condensate drain shall be connected to a common
drain riser. Should the main drain become plugged,
the wall sleeve design shall divert the water to the
outside of the building.
G. Condenser Fan:
Condenser fan shall be a propeller type with sepa-
rate split capacitor motor.
H. Adjustable Fresh Air:
Outside air intake shall be adjustable to meet code
requirements for fresh air introduction.
I. Wall Sleeves:
Wall sleeves shall be constructed of 20 gage galva-
nized steel to provide weathertight seal with dispos-
able weather guard for installation and baked
enamel finish inside and outside. Sleeve shall allow
water to overflow front edge of sleeve if the primary
drain becomes clogged.
J. Grille:
Grille shall be anodized corrosion-resistant alumi-
num, and custom painted.
K. Controls:
1. Control module shall be a remote thermostat
with heat anticipator, heat-off-cool switch, on-
auto fan switch.
2. Evaporator coil freeze protection shall be pro-
vided. During the cooling mode, should the
evaporator coil experience freezing conditions
that could result in ice build-up on the coil and
subsequent compressor damage, a tempera-
ture sensor attached to the coil shall deenergize
the compressor.
3. Low ambient lockout shall be provided to lock
out compressor at ambient temperatures below
40 F to extend compressor life.
4. Random restart shall be provided. When power
is turned on after a power outage, a built-in ran-
dom restart (3 to 4 minutes) shall prevent all
units from restarting simultaneously. Simultane-
ous restarting can damage electrical compo-
nents.
5. Compressor restart delay shall be provided. A
3-minute delay shall ensure that system pres-
sures are allowed to equalize before a compres-
sor restart.
6. Fan delay shall be provided. In the cooling
mode, the fan motor delay shall allow the fan to
continue to operate up to 45 seconds after
thermostat is satisfied.
Guide specifications