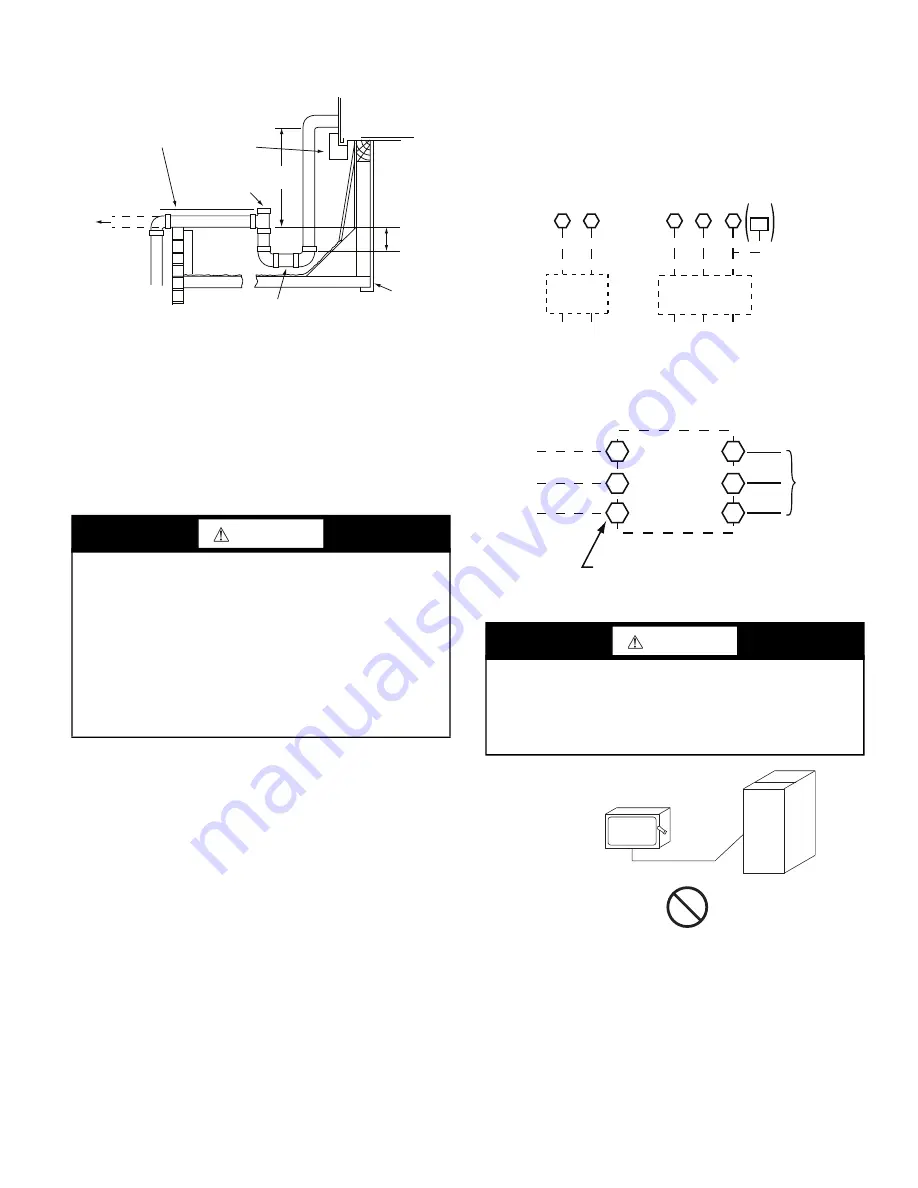
15
The piping for the condensate drain and external trap can be com
-
pleted after the unit is in place. See Fig. 20.
Fig. 20 — Condensate Drain Piping Details
All units must have an external trap for condensate drainage. In
-
stall a trap at least 4-in. (102 mm) deep and protect against
freeze-up. If drain line is installed downstream from the external
trap, pitch the line away from the unit at 1-in. per 10 ft (25 mm in
3 m) of run. Do not use a pipe size smaller than the unit connec
-
tion (
3
/
4
-in.).
Step 11 — Make Electrical Connections
NOTE: Field-supplied wiring shall conform with the limitations
of minimum 63°F (33°C) rise.
FIELD POWER SUPPLY
If equipped with optional Powered Convenience Outlet: The pow
-
er source leads to the convenience outlet’s transformer primary are
not factory-connected. Installer must connect these leads accord
-
ing to required operation of the convenience outlet. If an always-
energized convenience outlet operation is desired, connect the
source leads to the line side of the unit-mounted disconnect.
(Check with local codes to ensure this method is acceptable in
your area.) If a de-energize via unit disconnect switch operation of
the convenience outlet is desired, connect the source leads to the
load side of the unit disconnect. On a unit without a unit-mounted
disconnect, connect the source leads to compressor contactor C
and indoor fan terminal block (IFTB) pressure lugs with unit field
power leads.
Refer to Fig. 27 for power transformer connections and the dis
-
cussion on connecting the convenience outlet on page 16. Field
power wires are connected to the unit at line-side pressure lugs
on compressor contactor C and indoor fan contactor IFC (see
wiring diagram label for control box component arrangement) or
at factory-installed option non-fused disconnect switch. Max
wire size is #2 AWG (copper only, see Fig. 22). See Fig. 21 and
unit label diagram for field power wiring connections.
NOTE: TEST LEADS — Unit may be equipped with short leads
(pigtails) on the field line connection points on contactor C or op
-
tional disconnect switch. These leads are for factory run-test pur
-
poses only; remove and discard before connecting field power
wires to unit connection points. Make field power connections di
-
rectly to line connection pressure lugs only.
Fig. 21 — Power Wiring Connections
Fig. 22 — Disconnect Switch and Unit
UNITS WITH FACTORY-INSTALLED NON-FUSED DIS
-
CONNECT
The factory-installed option non-fused disconnect (NFD) switch is
located in a weatherproof enclosure located under the main con
-
trol box. The manual switch handle and shaft are shipped in the
disconnect enclosure. Assemble the shaft and handle to the switch
at this point. Discard the factory test leads (see Fig. 21).
Connect field power supply conductors to LINE side terminals
when the switch enclosure cover is removed to attach the handle.
WARNING
ELECTRIC SHOCK HAZARD
Failure to follow this warning could result in personal injury or
death.
Unit cabinet must have an uninterrupted, unbroken electrical
ground to minimize the possibility of personal injury if an
electrical fault should occur. This ground may consist of elec
-
trical wire connected to unit ground lug in control compart
-
ment, or conduit approved for electrical ground when installed
in accordance with NEC; ANSI/NFPA 70, latest edition (in
Canada, Canadian Electrical Code CSA [Canadian Standards
Association] C22.1), and local electrical codes.
NOTE: Trap should be deep enough to offset maximum unit static
difference. A 4-in. (102 mm) trap is recommended.
MINIMUM PITCH
1˝ (25 mm) PER
1
0´
(
3
m) OF LINE
BA
S
E RAIL
OPEN
VENT
TO ROOF
DRAIN
DRAIN PLUG
ROOF
CURB
S
EE NOTE
3
˝ (76 mm)
MIN
WARNING
FIRE HAZARD
Failure to follow this warning could result in personal injury,
death, or property damage.
Do not connect aluminum wire between disconnect switch and
unit. Use only copper wire.
Disconnect
per
NEC
Disconnect
per
NEC
20
8
/2
3
0-1-60
11
1
3
11
1
3
1
3
L1
L2
L
3
TB
C
C
IFC
or
(1-ph
IFM)
20
8
/2
3
0-
3
-60
460-
3
-60
575-
3
-60
Units Without Non-Fused Disconnect Option
Units With Non-Fused Disconnect Option
2
4
6
1
3
5
L1
L2
L
3
Optional
Disconnect
S
witch
Disconnect factory test leads; discard.
Factory
Wiring
COPPER
WIRE ONLY
ELECTRIC
DI
S
CONNECT
S
WITCH
ALUMINUM
WIRE
Содержание 50KC04
Страница 4: ...4 Fig 2 Unit Dimensional Drawing of Units Built On and After 4 15 19...
Страница 5: ...5 Fig 3 Unit Dimensional Drawing of Units Built on and Prior to 4 15 19...
Страница 6: ...6 Fig 4 Unit Corner Weights and Clearances...
Страница 7: ...7 Fig 5 Base Rail Details...
Страница 8: ...8 Fig 6 Thru the Base Charts...
Страница 35: ...35 Fig 49 Electro Mechanical Control Wiring Diagram...
Страница 36: ...36 Fig 50 Electro Mechanical Control Wiring Diagram with Humidi MiZer System...
Страница 37: ...37 Fig 51 Electro Mechanical Power Wiring...
Страница 38: ...38 Fig 52 PremierLink Wiring Schematic...
Страница 39: ...39 Fig 53 PremierLink Wiring Schematic with Humidi MiZer System...
Страница 40: ...40 Fig 54 RTU Open System Control Wiring Diagram...
Страница 41: ...41 Fig 55 RTU Open System Control Wiring Diagram with Humidi MiZer System...
Страница 47: ...47 Fig 63 TXV Metering Device Position in Reheat Coil Typical Diagram for Sizes 04 06 TXV...
Страница 48: ......
Страница 49: ......