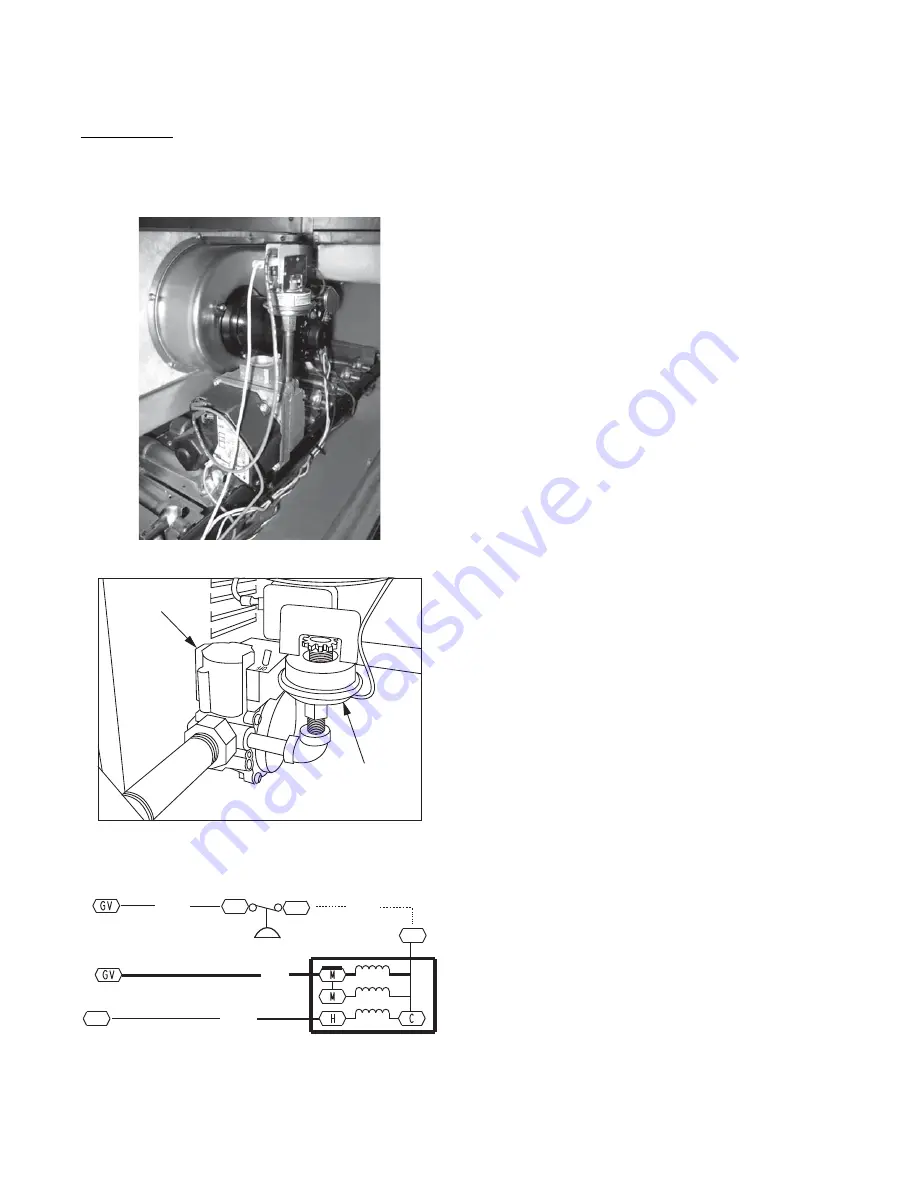
41
Ignition Fault (5 flashes) lockout. Reset of the low
pressure switch is automatic on rise in supply line
pressure. Reset of the IGC requires a recycle of unit
power after the low pressure switch has closed.
Limit Switch
Remove the blower access panel. The Limit Switch is
located on the fan deck for sideshot units and on the
vestibule plate for downshot units. SeeFig 49.
48TC*D08 only
C08238
LP LOW PRESSURE
SWITCH
GAS VALVE
C08238A
Fig. 49
−
LP Low Pressure Switch (Installed)
PNK
W2
TSTAT
GRA
BRN
IGC
J2-12
IGC
J2-11
BRN
C
NO
MGV
C
LP LPS
C08285
Fig. 50
−
LP Supply Line Low Pressure Switch Wiring
This switch also prevents operation when the propane tank
level is low which can result in gas with a high
concentration of impurities, additives, and residues that
have settled to the bottom of the tank. Operation under
these conditions can cause harm to the heat exchanger
system. Contact your fuel supplier if this condition is
suspected.
Flue Gas Passageways
To inspect the flue collector box and upper areas of the
heat exchanger:
1. Remove the combustion blower wheel and motor as-
sembly according to directions in the Combustion
−
Air Blower section. See Fig. 51.
2. Remove the flue cover to inspect the heat exchanger.
3. Clean all surfaces as required using a wire brush.
Combustion
−
Air Blower
Clean periodically to assure proper airflow and heating
efficiency. Inspect the blower wheel every fall and
periodically during the heating season. For the first
heating season, inspect the blower wheel bi
−
monthly to
determine proper cleaning frequency.
To access the burner section, open the heater access door
below the indoor fan panel.
To inspect the blower wheel, shine a flashlight into the
draft hood opening. If cleaning is required, remove the
motor and wheel as follows:
1. Remove the seven screws attaching the induced
−
draft
motor housing to the vestibule plate. See Fig. 51.
2. The blower wheel can be cleaned at this point. If ad-
ditional cleaning is required, continue with Steps 3
through 5.
3. Remove the blower from the motor shaft by loosening
two setscrews.
4. Remove the motor by removing the four screws that
hold the motor to the mounting plate. Remove the
motor cooling fan by removing one setscrew.
5. Remove the nuts that hold the motor to the mounting
plate.
6. To reinstall, reverse the procedure outlined above.
Содержание 48TC 17 Series
Страница 39: ...39 C10818 Fig 45 RTU OPEN Control Module ...
Страница 82: ...82 APPENDIX IV WIRING DIAGRAMS cont C12615 Fig 73 48TC D17 D28 Control Diagram 208 230 3 60 460 575 3 60 ...
Страница 83: ...83 APPENDIX IV WIRING DIAGRAMS cont C12616 Fig 74 48TC D17 D28 Power Diagram 208 230 3 60 ...
Страница 84: ...84 APPENDIX IV WIRING DIAGRAMS cont C12266 Fig 75 48TC D17 D28 Power Diagram 460 3 60 ...
Страница 85: ...85 APPENDIX IV WIRING DIAGRAMS cont C12618 Fig 76 48TC D17 D28 Power Diagram 575 3 60 ...
Страница 86: ...86 APPENDIX IV WIRING DIAGRAMS cont C14061 Fig 77 48TC D17 D28 Control Diagram with Humidi MiZer ...
Страница 87: ...87 APPENDIX IV WIRING DIAGRAMS cont C12620 Fig 78 48TC D17 D28 Power Diagram 208 230 3 60 with Humidi MiZer ...
Страница 88: ...88 APPENDIX IV WIRING DIAGRAMS cont C12621 Fig 79 48TC D17 D28 Power Diagram 460 3 60 with Humidi MiZer ...
Страница 89: ...89 APPENDIX IV WIRING DIAGRAMS cont C12622 Fig 80 48TC D17 D28 Power Diagram 575 3 60 with Humidi MiZer ...
Страница 91: ...91 APPENDIX IV WIRING DIAGRAMS cont C13766 Fig 82 PremierLinkt System Control Wiring Diagram with Humidi MiZer ...
Страница 92: ...92 APPENDIX IV WIRING DIAGRAMS cont C13767 Fig 83 RTU OPEN Wiring Diagram ...
Страница 93: ...93 APPENDIX IV WIRING DIAGRAMS cont C13768 Fig 84 RTU OPEN Wiring Diagram with Humidi MiZer ...