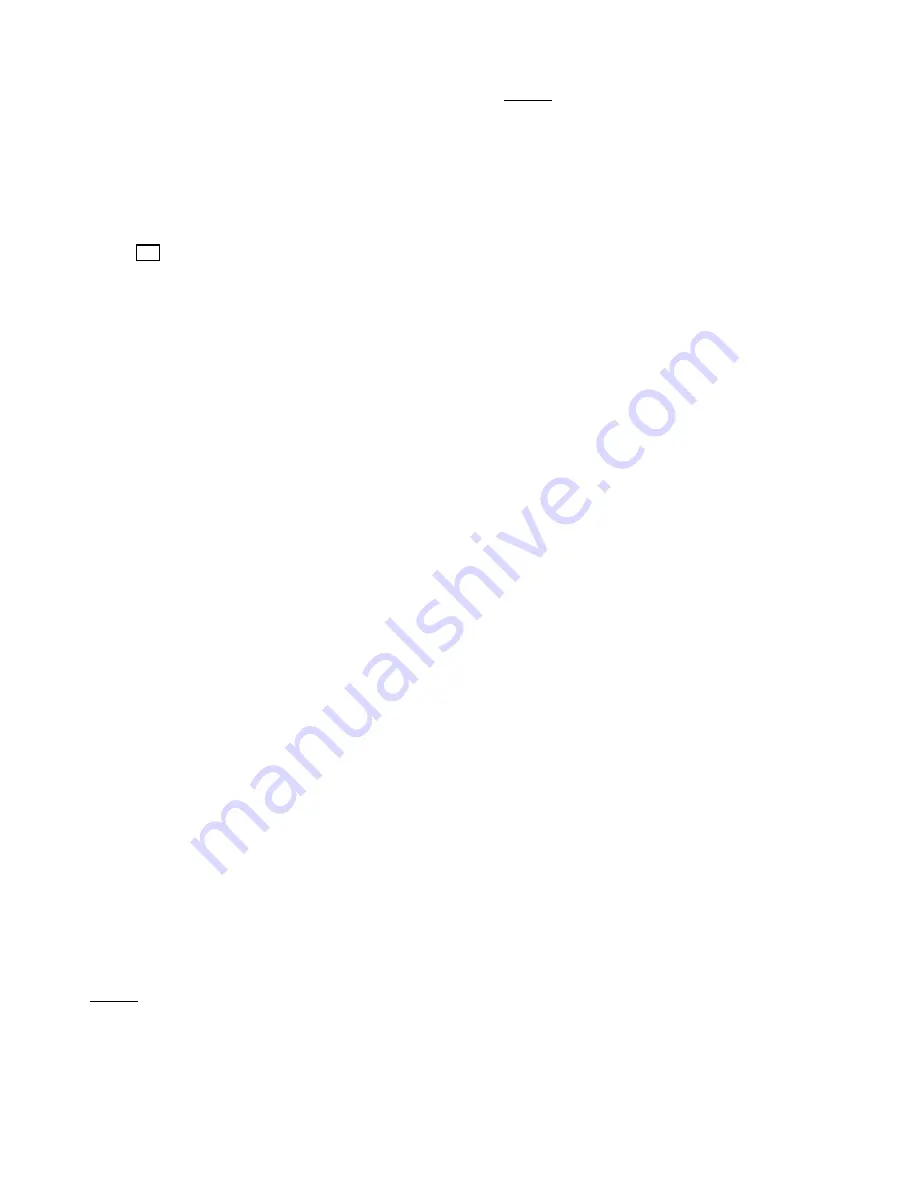
17
supply disconnect and check the crankcase oil level. Add oil
only if necessary to bring the oil into view in the sight glass. If
oil is added, run the system for an additional 10 minutes, then
stop and check oil level. If the level remains low, check the
piping system for proper design for oil return; also check the
system for leaks.
If the initial check shows too much oil (too high in the sight
glass) remove oil to proper level. See Preliminary Oil Charge,
page 16, for proper procedure for adding and removing oil.
When the above checks are complete, repeat the procedure
with the unit operating at minimum load conditions. Unload
the compressor by disconnecting the field-control circuit lead
at TB2
.
Reconnect the field-control circuit lead when checks are
complete.
Final Checks —
Ensure all safety controls are operating,
control panel covers are on, and the service panels are in place.
Sequence of Operation
HEATING — Place thermostat selector at HEAT and set tem-
perature selector above room ambient.
COOLING — Place thermostat selector at COOL and set tem-
perature selector below room ambient.
When thermostat calls for unit operation (either heating or
cooling), the indoor-fan motor starts immediately. The
outdoor-fan motors and compressor start within 3 seconds to
5 minutes depending on when unit was last shut off by thermo-
stat, because unit contains a compressor time delay circuit.
When first-stage cooling is required, thermostat (TC1) closes,
causing the heat pump to start with an unloaded compressor.
When TC2 closes, demanding additional cooling, the compres-
sor loads to full load operation.
During heating, compressor is always fully loaded. When
TH1 demands first-stage heating, the heat pump starts within
3 seconds to 5 minutes depending on when unit was last shut
off by thermostat, because unit contains a compressor time
delay circuit. (The defrost board has speed terminals to shorten
this cycle.) When TH2 of the thermostat closes, auxiliary heat
supply (electric strip heat) is energized in 1 or 2 stages depend-
ing on number of stages available and whether outdoor thermo-
stats are closed.
Defrost is achieved by reversal from heating to cooling cy-
cle and deenergization of outdoor-fan motors, allowing hot re-
frigerant gas to defrost outdoor coil. Defrost is achieved with a
timer set to initiate defrost every 30, 50, or 90 minutes (factory
set at 30 minutes).
Defrost is initiated when refrigerant temperature leaving the
outdoor coil is measured below 27 F (2.8 C), (typically when
the outdoor ambient temperature is below 45 F [7.2] C as
sensed by the defrost thermostat [DFT]).
Defrost is terminated when: The refrigerant temperature
rises to 65 F (18.3 C) (80 F [26.7 C] for 38AQS016) at the DFT
location on the liquid line; or the refrigerant pressure rises to
280 psig (1931 kPag) at the HPS2 location on the liquid line; or
the defrost timer completes the 10-minute cycle.
DUPLEX 38AQS012 OR 016 OUTDOOR UNITS WITH
40RMQ024 OR 40RMQ028 — The sequence of operation is
similar to the description above with the following exceptions:
Cooling — The control system may be configured in two differ-
ent ways: for face split coil operation or for full face active system.
Face Split Coil Operation — When TC-1 closes, condensing
unit A will start fully loaded. When TC-2 closes, condensing
unit B will start fully loaded.
Full Face Active Operation — When TC-1 closes, condensing
unit A and condensing unit B will start with unloaded
compressors. When TC-2 closes, the compressors in both con-
densing units will load.
Heating — When TH-1 closes, both condensing unit A and
condensing unit B will start in the Heating mode. When TH-2
closes, the auxiliary heat (electric resistance) heat will be
energized.
SAFETIES — The high-pressure switch, loss-of-charge
switch, oil pressure safety switch, and compressor overtemper-
ature safety are located in a Signal-LOC™ circuit that prevents
heat pump operation if these safety devices are activated. A
light at the thermostat energizes when Signal-LOC circuit is
affected. The lockout system can be reset by adjusting the ther-
mostat to open the contacts (down for Heating mode, up for
Cooling mode), deenergizing the Signal-LOC circuitry. Com-
pressor overcurrent protection is achieved with a circuit
breaker which requires manual resetting at the outdoor unit
control box.
The unit is equipped with an oil pressure safety switch that
protects the compressor if oil pressure does not develop on
start-up or is lost during operation. The oil pressure switch is of
the manual reset type and therefore must be reset at the outdoor
unit. DO NOT RESET MORE THAN ONCE.
If oil pressure switch trips, determine cause and correct. DO
NOT JUMPER OIL PRESSURE SAFETY SWITCH.
To reset the oil pressure switch:
1. Disconnect power to the unit.
2. Press the RESET button on the oil pressure switch.
3. Reconnect power to the unit.
Unit is equipped with a no-dump reversing valve circuit.
When unit is in Cooling mode, reversing valve remains in cool-
ing position until a call for heating is requested by thermostat.
When unit is in Heating mode, reversing valve remains in heat-
ing position until there is a call for cooling.
The crankcase heater is in a lockout circuit. If crankcase
heater is defective, compressor is locked off. Heat pump re-
mains off until corrective action is taken. The lockout circuit
cannot be reactivated by adjusting the thermostat. To reset the
crankcase heater lockout, disconnect and then reconnect power
to unit.
LIQUID LINE SOLENOID — To minimize refrigerant
migration to the compressor during the heat pump OFF cycle,
the unit features a bi-flow liquid line solenoid valve. The valve
opens when the compressor is energized, and closes when the
compressor is deenergized. This feature reduces compressor
flooded starts, significantly increasing compressor life.
ACCUMULATOR — The unit accumulator controls the rate
of liquid refrigerant to the compressor during heat pump opera-
tion. The accumulator features a unique method for returning
oil to the compressor. The oil return mechanism is external to
the accumulator. The mixture of oil and refrigerant is metered
to the compressor by a brass orifice which is removable and
cleanable. The oil return mechanism also contains a solenoid
valve that opens when the compressor is ON and closes when
the compressor is OFF. This keeps the liquid refrigerant stored
in the accumulator from draining to the compressor during the
heat pump OFF cycle, which further protects the compressor
against flooded starts.
OIL CHARGE (Tables 1A and 1B) — Allow unit to run for
about 20 minutes. Stop unit and check compressor oil level.
Add oil only if necessary to bring oil into view in sight glass.
Refer to Preliminary Oil Charge section on page 16. Use only
Carrier-approved compressor oil.
CHECK OPERATION — Ensure operation of all safety con-
trols. Replace all service panels. Be sure that control panel
cover is closed tightly.
Y2