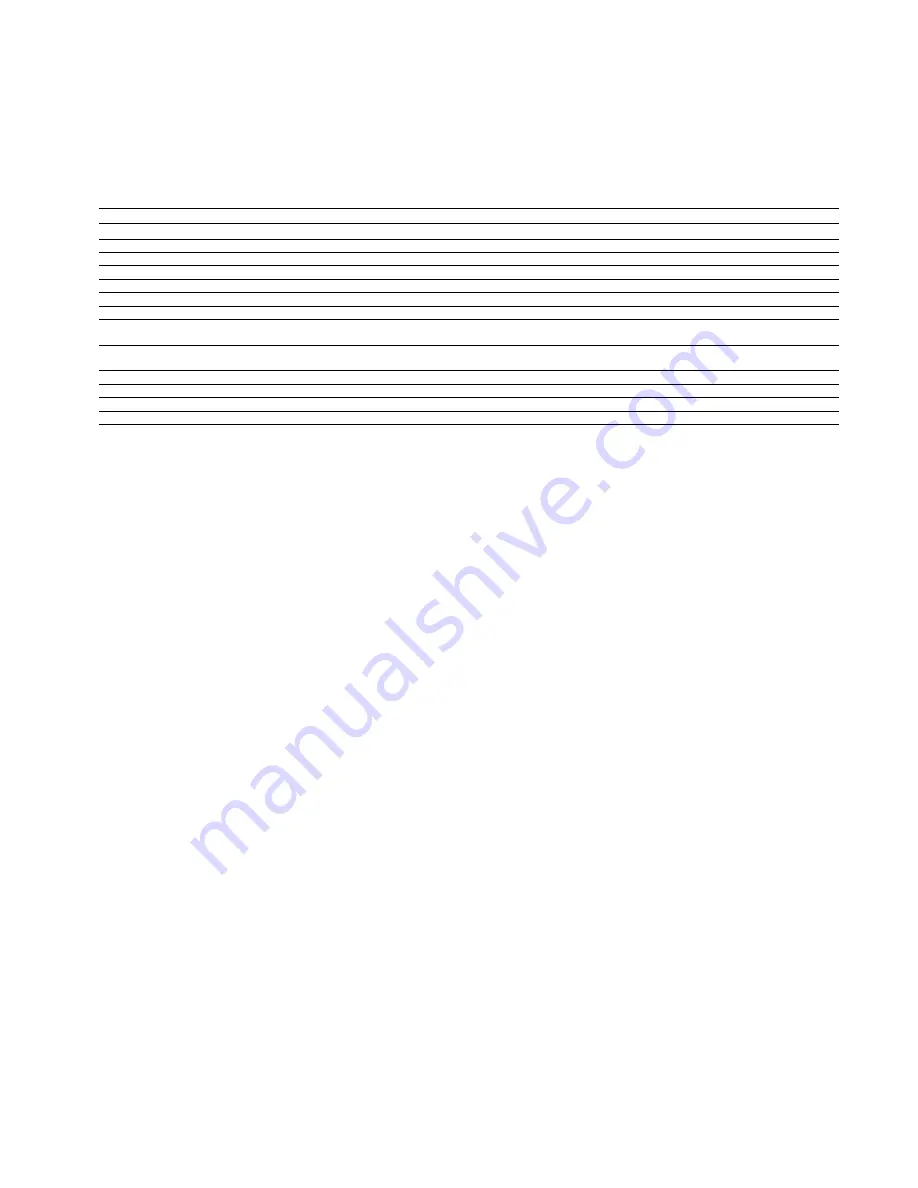
27
6.14 - Refrigerant gas leak detection (option 159)
The control permits refrigerant leak detection. Two
additional sensors that detect the refrigerant concentration
in the air must be installed on the unit. If one of these
sensors detects an abnormal refrigerant level for more
than one hour, the alarm will be triggered, but the unit
will continue to operate.
6.15 - Low noise (option 257)
The low noise option is used to reduce the noise level by
limiting the speed of the fans to 750 RPM.
6.16 - BACnet (option 149)
The BACnet/IP communication protocol is used by the
building management system or the programmable
controllers to communicate with the Touch Pilot control.
NOTE: BACnet option can be installed only by Carrier
service.
Energy management option – board connections
Description
Type
Channel
Remarks
Space temperature for reset control
Analogue input
Ch 02
Active setpoint reset via space temperature control
Setpoint reset control
Analogue input
Ch 05
Used for setpoint reset control
Capacity limit control
Analogue input
Ch 06
Used for capacity limit control
Chiller capacity running output
Analogue output
Ch 07
0 to 10 V output
Occupancy override switch
Digital input
Ch 08
If the contact is closed in Remote mode, the unit goes into the occupied mode
Capacity limit switch input 2
Digital input
Ch 09
If the contact is closed, the second capacity limit switch is active
Customer interlock
Digital input
Ch 10
Permits immediate unit shutdown (Remote mode only)
If the contact is closed, the unit is not allowed to start.
Ice done contact
Digital input
Ch 11a
Ch 11b
If the contact is closed, the unit enters the ice storage mode
Compressor A running status
Digital output
Ch 16
Output active if compressor A is operating (the contact is closed)
Compressor B running status
Digital output
Ch 17
Output active if compressor B is operating (the contact is closed)
Chiller shutdown
Digital output
Ch 24
Used to indicate the unit shutdown (the contact is closed)
Chiller alert
Digital output
Ch 25
Used to indicate the unit alert condition (the contact is closed)
6.12 - Energy management module (option 156)
The energy management module is used to control the
level of energy consumption, providing users with
information such as current unit status, compressors
operating status, etc.
This option requires the installation of NRCP2 board.
6.17 - Hydronic kit (option 116X)
The hydronic kit option allows for continuous monitoring
of the water flow rate.
Hydronic kit option provides the following parameters:
•
Inlet and outlet water pressure (PUMPSTAT in the
Main menu)
•
Evaporator flow rate
•
Evaporator capacity
The water flow rate is based on pump inlet and evaporator
outlet pressures, the evaporator and piping pressure drops
curves and the pump head curve.
The evaporator capacity is calculated according to the flow
rate, the water constant, and the difference between the
entering and leaving evaporator water temperature.
This option requires the installation of an additional
AUX1 board.
Flow rate and evaporator capacity are displayed for
information only. Pressure instability and evaporator dirt
can highly impact the calculation.
6.18 - Variable water flow control (option 299)
The control can be configured in three different modes:
•
Evaporator delta temperature
: Difference between
entering and leaving temperature.
•
Evaporator output water pressure
: Controlling a
constant water pressure output.
•
Schedule
: Two different 0-10V thresholds can be applied
depending on whether the chiller is running or not.
6.13 - Evaporator heater (option 41)
The evaporator heater protects the evaporator against
freezing when the unit is stopped at low ambient air
temperature.The heater is activated when the unit is
stopped manually or shut down due to an alarm.
This option requires the installation of an additional
AUX1 board.