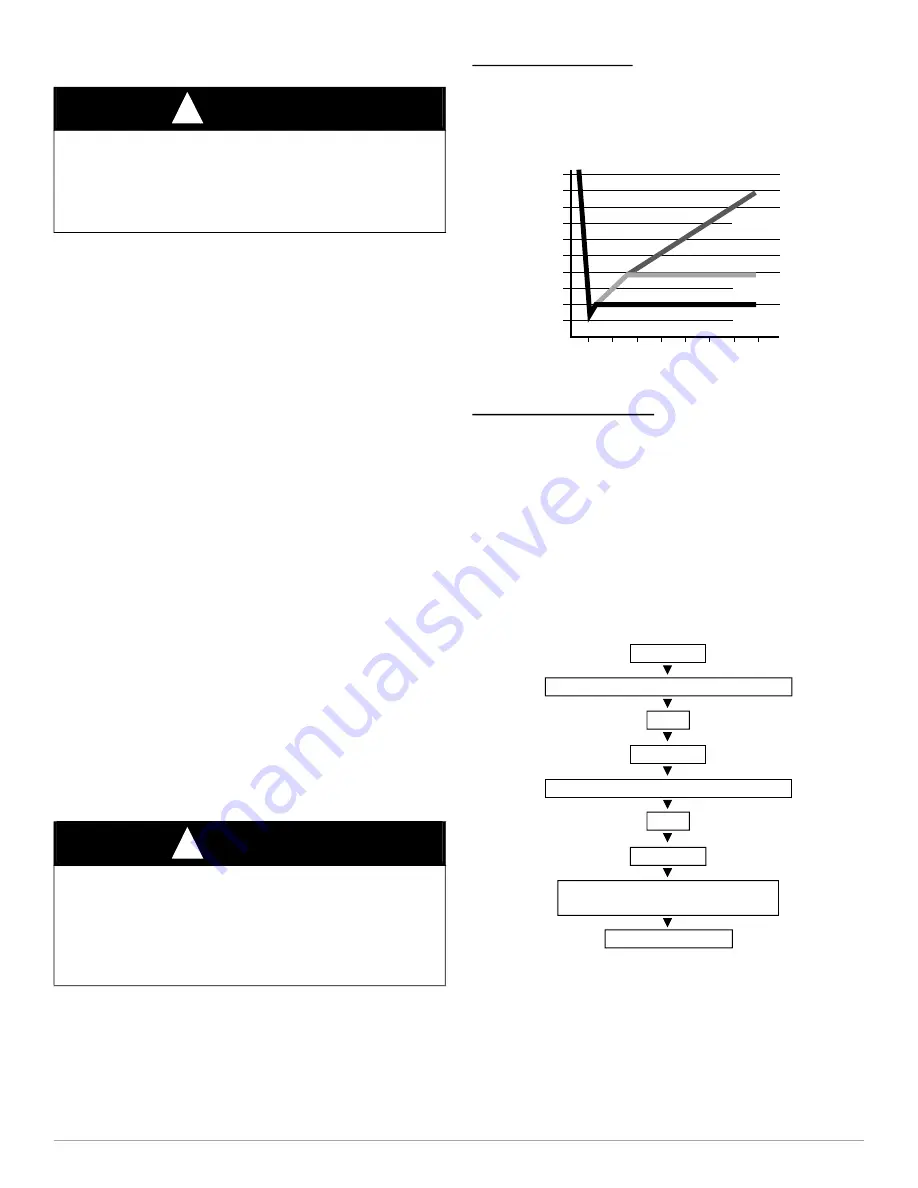
: Service Manual
Manufacturer reserves the right to change, at any time, specifications and designs without notice and without obligations.
25
8. Replace filter drier, evacuate system, recharge, and check for
normal system operation.
System Clean-Up After Burnout
Some compressor electrical failures can cause motor to burn. When this
occurs, by-products of burn, which include sludge, carbon, and acids,
contaminate system. Test the oil for acidity using POE oil acid test to
determine burnout severity. If burnout is severe enough, system must be
cleaned before replacement compressor is installed. The 2 types of
motor burnout are classified as mild or severe.
In mild burnout, there is little or no detectable odor. Compressor oil is
clear or slightly discolored. An acid test of compressor oil will be
negative. This type of failure is treated the same as mechanical failure.
Liquid-line strainer should be removed and liquid-line filter drier
replaced.
In a severe burnout, there is a strong, pungent, rotten egg odor.
Compressor oil is very dark. Evidence of burning may be present in
tubing connected to compressor. An acid test of compressor oil will be
positive. Follow these additional steps:
1. TXV must be cleaned or replaced.
2. Drain any trapped oil from accumulator if used.
3. Remove and discard liquid-line strainer and filter drier.
4. After system is reassembled, install liquid and suction-line R-410A
filter driers.
NOTE:
On heat pumps, install suction line drier between compressor
and accumulator.
5. Operate system for 10 hr. Monitor pressure drop across drier. If
pressure drop exceeds 3 psig replace suction-line and liquid-line
filter driers. Be sure to purge system with dry nitrogen when
replacing filter driers. If suction line driers must be replaced, retest
pressure drop after additional 10 hours (run time). Continue to
monitor pressure drop across suction line filter drier. After 10 hr of
run time, remove suction-line filter drier and replace liquid-line
filter drier. Never leave suction-line filter drier in system longer
than 72 hr (actual time).
6. Charge system. (See unit information plate.)
Evacuation
Proper evacuation of the system will remove non-condensibles and
assure a tight, dry system before charging. The 2 methods used to
evacuate a system are the deep vacuum method and the triple evacuation
method.
Deep Vacuum Method
The deep vacuum method requires a vacuum pump capable of pulling a
vacuum of 500 microns and a vacuum gauge capable of accurately
measuring this vacuum depth. The deep vacuum method is the most
positive way of assuring a system is free of air and moisture. (See
.)
A95424
Fig. 27 – Deep Vacuum Graph
Triple Evacuation Method
The triple evacuation method should be used when vacuum pump is only
capable of pumping down to 28 in. of mercury vacuum and system does
not contain any liquid water. Refer to
and proceed as follows:
7. Pump system down to 28 in. of mercury and allow pump to
continue operating for an additional 15 minutes.
8. Shut off vacuum pump.
9. Connect a nitrogen cylinder and regulator to system and open until
system pressure is 2 psig.
10. Allow system to stand for 1 hr. During this time, dry nitrogen will
be able to diffuse throughout the system absorbing moisture.
11. Repeat this procedure as indicated in
. System will then be
free of any contaminants and water vapor.
A95425
Fig. 28 – Triple Evacuation Method
Check Charge
.)
Factory charge amount and desired subcooling are shown on unit rating
plate. Charging method is shown on information plate inside unit. To
properly check or adjust charge, conditions must be favorable for
subcooling charging. Favorable conditions exist when the outdoor
temperature is between 70°F and 100°F (21.11°C and 37.78°C), and the
CAUTION
!
UNIT DAMAGE HAZARD
Failure to follow this caution may result in equipment damage or
improper operation.
Do not leave system open to atmosphere. Compressor oil is highly
susceptible to moisture absorption.
CAUTION
!
UNIT DAMAGE HAZARD
Failure to follow this caution may result in equipment damage or
improper operation.
Only suction line filter driers should be used for refrigerant and oil
clean up. Use of non-approved products could limit system life and
void unit warranty.
500
MINUTES
0
1
2
3
4
5
6
7
1000
1500
LEAK IN
SYSTEM
VACUUM TIGHT
TOO WET
TIGHT
DRY SYSTEM
2000
MICRONS
2500
3000
3500
4000
4500
5000
CHECK FOR TIGHT, DRY SYSTEM
(IF IT HOLDS DEEP VACUUM)
EVACUATE
BREAK VACUUM WITH DRY NITROGEN
WAIT
EVACUATE
CHARGE SYSTEM
BREAK VACUUM WITH DRY NITROGEN
EVACUATE
WAIT