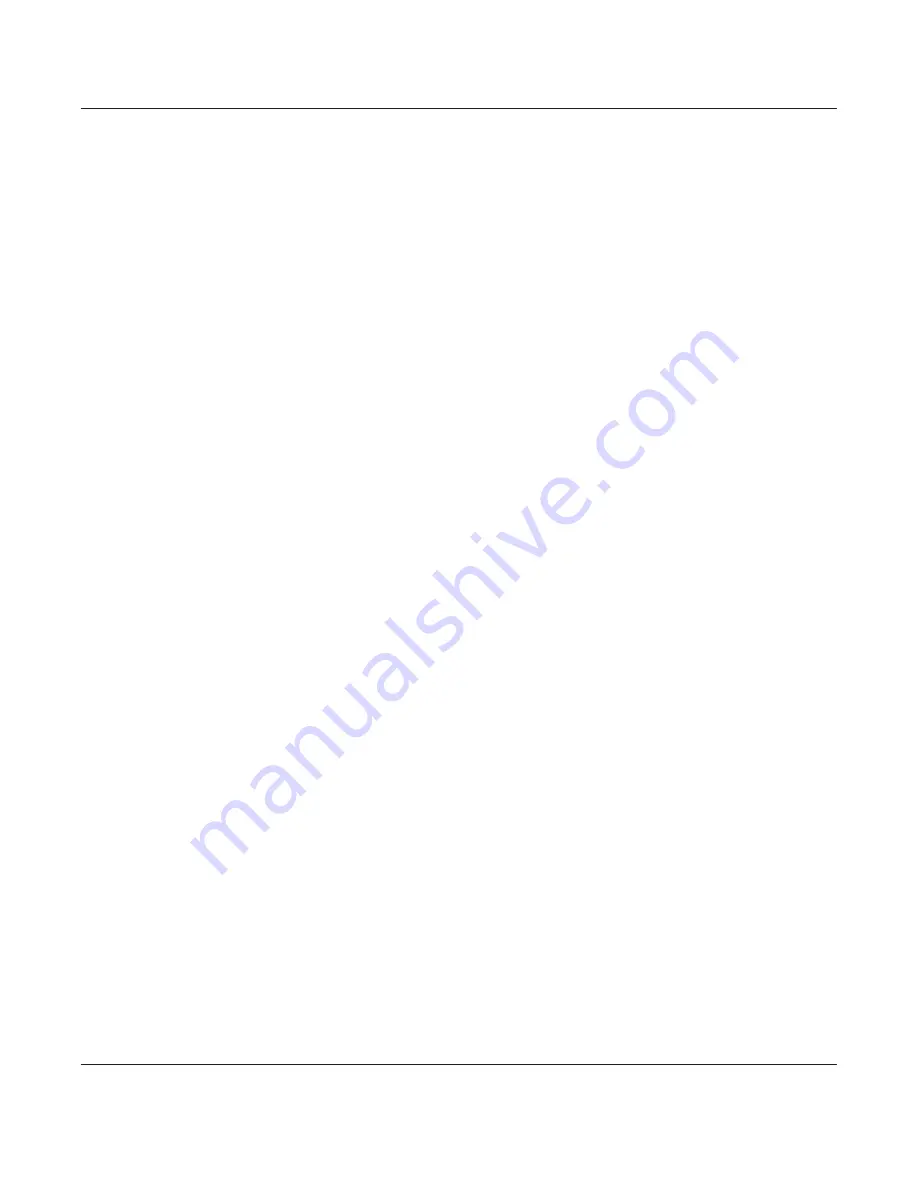
4.4
LOGIC BOARD ASSEMBLY
The Logic Board receives its power from the
8V
supply on the PC Unit via the
IUI
connector. The Logic Board contains
DC
-to-
DC
converters to convert the
+8V
supply to
+3.3V
,
+5V
, and
+15V
supplies
,
and a
variable voltage supply to the motor. The
Logic Board also contains an inverting
circuit to produce a -
5V
supply. The field-
programmable gate array (
FPGA)
on the
Logic Board controls the supply voltages
(
5V
,
3.3V
) to the digital and analog sensors.
The Logic Board monitors the supply
voltages and analog sensor signals, and
sets up the nominal power level for any
particular pumping rate. Incoming analog
sensor signals (from the pressure sensor,
force sensor, syringe sizer, and plunger
position sensor) are filtered and buffered,
and then fed to the
ADC
as inputs.
The Logic Board includes a processor, a
1M
x
8
flash
ROM
,
512K
x
8
static
RAM,
and
a watchdog timer circuit. The watchdog
timer circuit has a
1.6
–second timeout that
can put the Syringe or PCA Module into a
safe state if the Logic Board main processor
fails.
The Logic Board reads and writes to the
FPGA
via
I
/
O
address space. The
FPGA
contains the digital logic for generating
control signals for
ADC
,
DAC
, sensors, motor
feedback circuitry, module detection and
identification circuit interface, and
10
-phase
step signals for the motor drive circuitry.
The
FPGA
also generates a master
RESET
signal for the module.
The Logic Board’s main processor
communicates with the Display Board’s
microcontroller via a serial channel. The
Logic Board provides the Power-On Reset
signal to the Display Board. Upon keypad
input to the Display Board, the Logic Board
receives a Channel Off signal to stop the
motor.
The Logic Board contains
IUI
interface
circuitry that allows it to communicate with
the PC Unit.
The digital sensor interface on the Logic
Board contains current sense circuitry,
which reads output signals from the
photointerrupters on the lever detect sensor,
nut engaged sensor, and flange sensor. On
the Syringe Module only, the Logic Board
also reads signals from the
SET IN
sensor
(pressure sensor).
The motor drive circuitry on the Logic Board
uses a variable voltage supply to drive a
5
-
phase stepper motor and save power,
depending on the torque loading. A
combination of software settings and motor
feedback loop circuitry adjusts the motor
supply voltage in response to detected
motor loading. The motor feedback loop
starts with a nominal voltage based on
pumping rate, and adjusts motor voltage as
needed to maintain constant peak motor
current levels, independent of torque load.
The motor feedback loop keeps the voltage
range constant for any given pumping rate.
4.5
DRIVETRAIN ASSEMBLY
The drivetrain is a linear positioning device.
The geared stepper motor powers the
drivetrain, and the linear motion of the
drivetrain controls the drive head to push
the syringe plunger accurately and with
enough force to deliver medication from
many different syringes. Because system
positioning is open loop, the mechanical
parts and assembly must maintain a high
degree of accuracy.
PRINCIPLES OF OPERATION
4-3
Alaris
®
Syringe Module (8110 Series)
Alaris
®
PCA Module (8120 Series)
Technical Service Manual
Содержание Alaris 8110 series
Страница 9: ...1 GENERAL INFORMATION...
Страница 10: ......
Страница 15: ...2 CHECKOUT CONFIGURATION...
Страница 16: ......
Страница 27: ...3 PREVENTIVE MAINTENANCE...
Страница 28: ......
Страница 31: ...4 PRINCIPLES OF OPERATION...
Страница 32: ......
Страница 41: ...5A CORRECTIVE MAINTENANCE SYRINGE MODULE...
Страница 42: ......
Страница 71: ...5B CORRECTIVE MAINTENANCE PCA MODULE...
Страница 72: ......
Страница 105: ...6 TROUBLESHOOTING...
Страница 106: ......
Страница 115: ...7A ILLUSTRATED PARTS BREAKDOWN SYRINGE MODULE...
Страница 116: ......
Страница 143: ...7B ILLUSTRATED PARTS BREAKDOWN PCA MODULE...
Страница 144: ......
Страница 171: ......