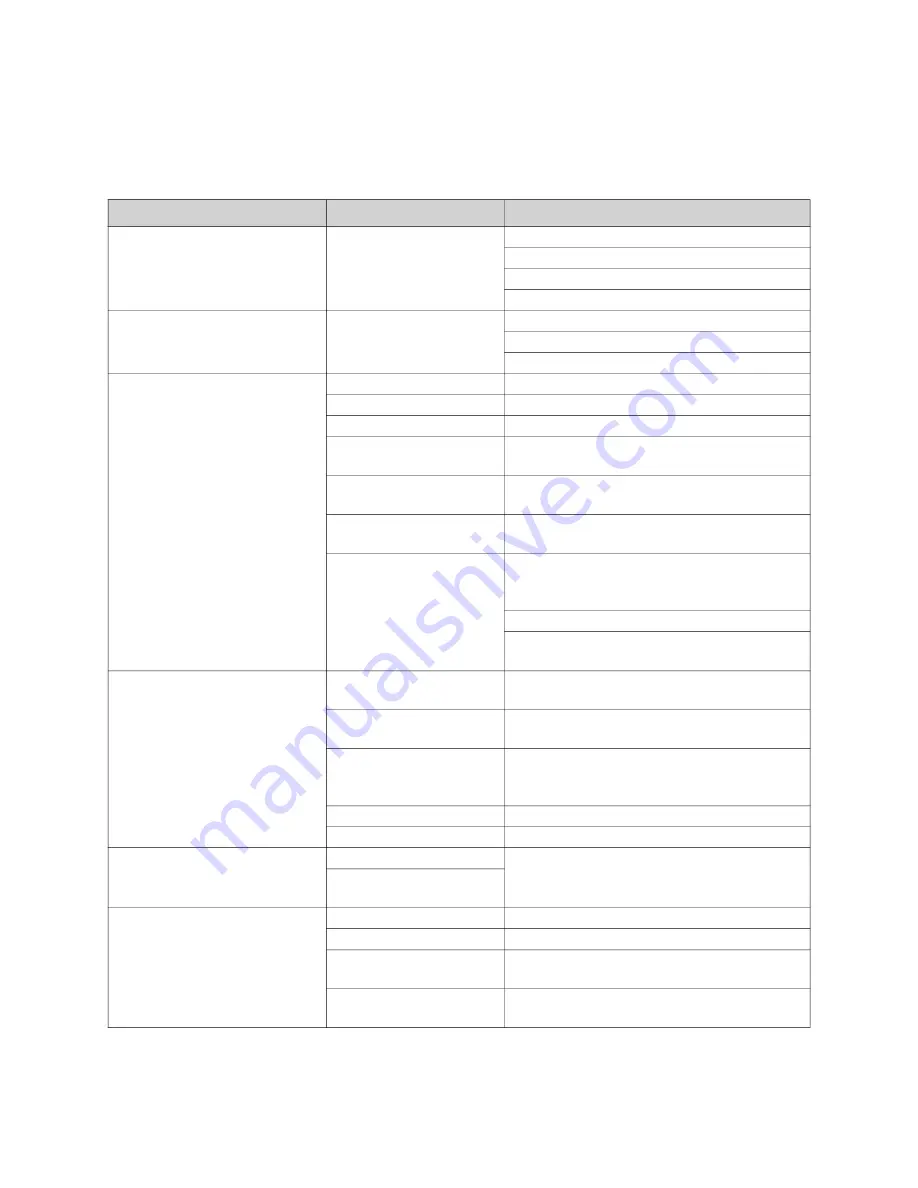
108
Troubleshooting
The following tables and information list possible causes and corrective actions for possible problems.
Review this section prior to consulting technical support.
System Troubleshooting Chart
Problem
Potential Cause
Corrective Action
Unit will not start
Power failure
Check voltage to the unit.
Check the disconnect switch.
Check the circuit breaker.
Check the hot, neutral, and ground wiring.
Unit On - HMI Off
Power Issue
Check connector J13 is properly connected.
Check wiring from HMI to connector J13.
Verify the circuit breaker (CB-01) is On.
System operates continuously -
poor cooling/heating
(heat pump mode)
Shortage of refrigerant
Test for leaks. Add refrigerant.
Restricted discharge line Repair or replace as required.
Dirty or clogged filters
Inspect filters. Clean or replace.
Dirty indoor coil
Inspect coil. Clean the coil, refer to
Cleaning Procedure” on page 132
.
Low airflow across indoor
coil
Check blower speed, duct static pressure,
filters.
Compressor
Verify compressor modulates between Min to
Max frequency.
Electronic Expansion
Valve (EEV)
Verify EEV position is 0% when not in
heating or cooling under Refridge Diag. See
“Monitoring the A/C System” on page 103.
Check the correct EEV is installed.
Refer to
.
System operates – blows cold
air in heat pump mode
Compressor
Verify compressor modulates between Min to
Max frequency.
Incorrect refrigerant
Non-condensable in
system
Recover the charge, evacuate the system.
.
Faulty reversing valve
Test reversing valve.
Defrost control
Test defrost control.
System operates - blows cold
air in gas heat mode
Gas supply issue
Refer to
“Furnace Troubleshooting Chart”
.
Faulty gas train
components.
System runs – blows cold air in
electric heat mode
Improper wiring
Check electrical wiring.
Electric disconnect switch Check electric heater disconnect switch
Fuse in electric heater
panel
Check fuses, replace is required.
Airflow Switch
Check airflow switch and tubing at the MUA
board.