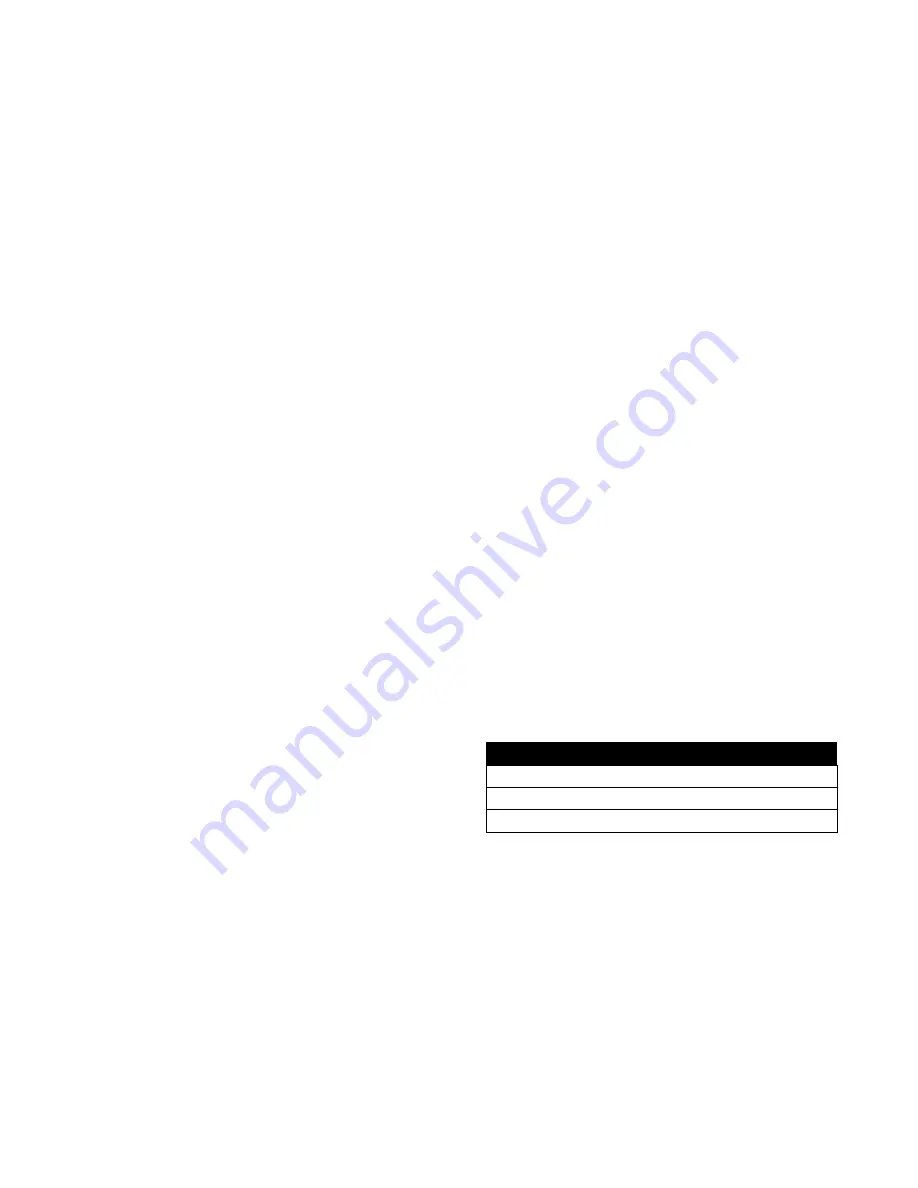
4
1.4
– Sequence of Operation
1. Power is supplied as per Section 4.2
2. The appliance is filled with water (or a water-glycol
mixture) in all pipes and the heat exchanger.
3.
The power switch is placed in the “ON” position.
120 VAC power is supplied to the control and
actuator transformers. 120 VAC is also applied to
the actuator.
4. The circulator installed on the DHW side starts
running.
5. The touch-screen digital display mounted on the
DynaFLO turns ON.
6. The built-in PID integrated in the control keeps
monitoring the DHW outlet temperature and
calculates the difference in value between the
DHW outlet temperature and the user selected set
point. It continuously attempts to achieve a
difference of 0 by modulating the electro-hydraulic
actuator thereby regulating the amount of heat
exchanged in the heat exchanger.
Please refer to Part 5 for more details about operation and
configuration of the control.
1.5
– Codes
The equipment shall be installed in accordance with
those installation regulations in force in the local area
where the installation is to be made.
These shall be
carefully followed in all cases. Authorities having jurisdiction
shall be consulted before installations are made. All
electrical wiring must be done in accordance with the
requirements of the authority having jurisdiction or, in the
absence of such requirements, with National Electrical
Code, ANSI/NFPA70 and/or the Canadian Electrical Code
part 1 CSA C22.1. Where required by the authority having
jurisdiction, the installation must conform to American
Society of Mechanical Engineers Safety Code for Controls
and Safety Devices for Automatically Fired Boilers, ASME
CSD-1.
1.6
– Warranty
Factory warranty (shipped with unit) does not
apply to units improperly installed or improperly
operated.
Factory warranty shall apply only when the
appliance is installed in accordance with local
plumbing and building codes, ordinances and
regulations, the printed instructions provided with
it and industry best practices.
Excessive
water hardness
causing a scale
buildup in the stainless steel heat exchanger or
pipes is not a fault of the appliance and is not
covered by warranty. Consult the factory for usage
recommendations in hard water areas.
Using or storing
corrosive chemicals
in the
vicinity of this appliance can rapidly attack the
stainless steel tubes and coils and voids warranty.
Damage caused by
freezing or dry firing
voids
warranty.
The manufacturer shall
NOT
be held liable for any
personal injury or property damage due to
condensation of any exterior part of the appliance
including pipes.
Part 2
– Installation
2.1
– Checking the Equipment
Check for signs of shipping damage upon receiving
equipment. Pay particular attention to parts accompanying
the appliance, which may show signs of being hit or
otherwise being mishandled. Verify total number of pieces
shown on packing slip with those actually received. In case
there is damage or a shortage, immediately notify carrier.
2.2
– Mechanical Environment
Install this appliance in a clean, dry location with adequate
air supply.
The mechanical room MUST NOT be used to store
corrosive or flammable chemicals, such as gasoline or paint
thinner. Such chemicals must not be stored in the vicinity of
this appliance. Chillers or other equipment utilizing
refrigerant should also not be installed in the same
mechanical room as fuel burning appliances.
2.3
– Locating the Equipment
The appliance should be located close to a floor drain in an
area where leakage from the appliance or connections will
not result in damage to the adjacent area or to lower floors
in the structure. Under no circumstances is the
manufacturer to be held responsible for water damage in
connection with this unit, or any of its components.
2.4
– Clearances
This appliance is suitable for installation with minimum
clearances to combustibles as follows:
Table 1: Clearances From Combustibles
Clearances, All Models
Top
12" (30cm)
Sides
12" (30cm)
Rear
12" (30cm)
Part 3
– Heat Exchanger
3.1
– Overview
The heat exchanger installed in the DynaFLO is a very
compact assembly composed of stainless steel plate packs
sealed together by means of brazing metal (Copper) along
the border of the units. This eliminates the need for
traditional gaskets or external pressure retaining parts. All
of the heat exchangers used in DynaFLO models are ASME
certified, have CRN and are NSF 372 certified. The plate
packs making up the heat exchanger have special
corrugation patterns that promote turbulent flow which in
turn dramatically increases rate of heat transfer. Regular
maintenance and cleaning of the heat exchangers are
required. The manufacturer is not responsible for damages
Содержание DynaFLO DOWB-1
Страница 2: ......
Страница 25: ...22 Appendix B Electrical Schematics DynaFLO ...
Страница 27: ...24 ...