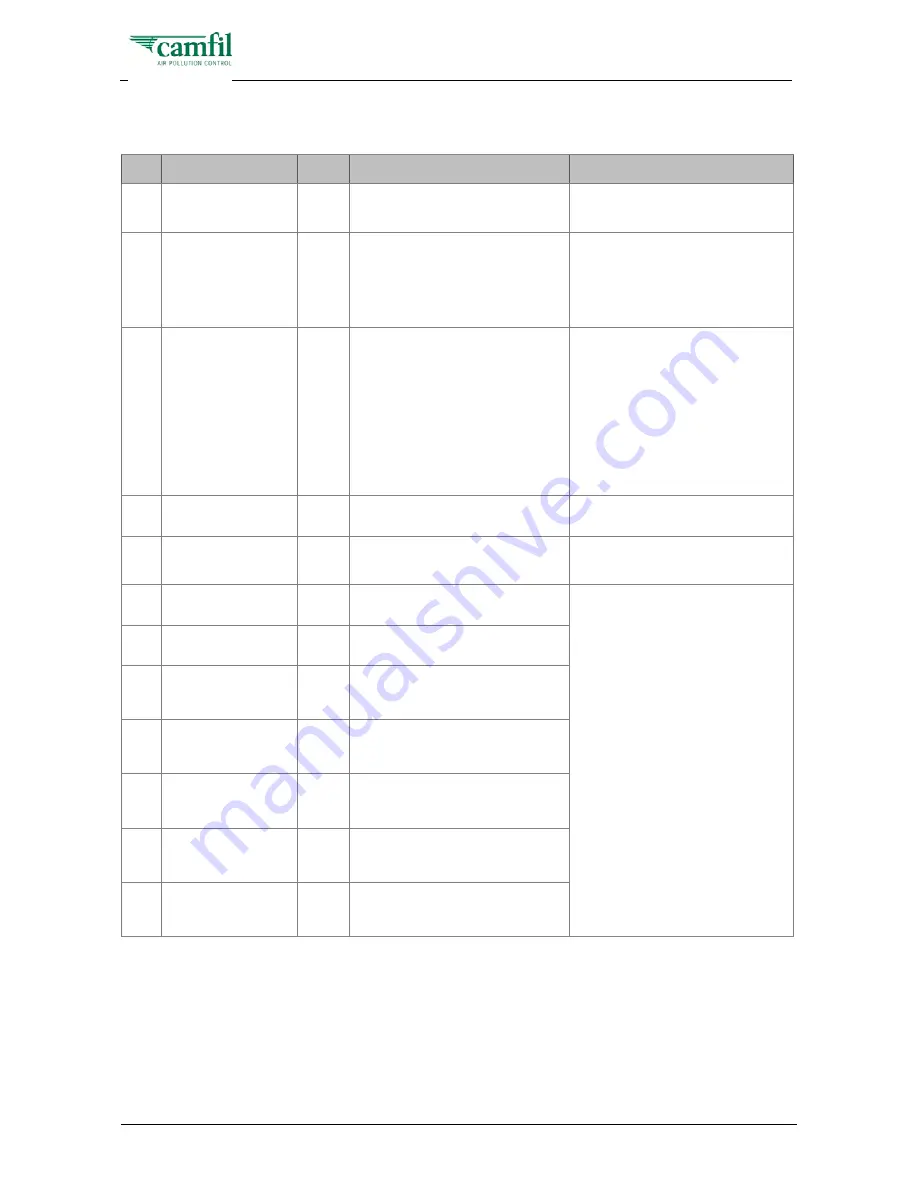
Intervals:
D
=
daily,
W
=
weekly,
M
=
monthly,
3M
=
every 3
months,
6M
=
every 6
months,
Y
=
yearly
Item
Maintenance
point
Interval
Type
of
check/maintenance
task
Comments
3
Water
tank
Drain
or
pump
out
the
contents
of
the
water
tank.
3.1
Sealing
band
W
CLEANING:
7.
Clean
the
sealing
faces
and
then
degrease
them
using
acid
‐
free
grease.
IF
NECESSARY:
8.
Replace
the
rubber
band
if
it
is
defective.
9.
If
necessary,
adjust
the
clamp
fastener.
3.2
Water
tank
D/W
CLEANING:
10.
Drain
or
pump
out
the
sludge/dirty
water.
11.
Shovel
out
any
remaining
sludge
and
clean
the
tank
with
a
high
‐
pressure
cleaner.
12.
Fill
with
clean
water.
IF
NECESSARY:
13.
Replace
the
rubber
band
if
it
is
defective.
14.
Retouch
the
paintwork.
Water
quality
Regularly
replace
the
scrubbing
wa
‐
ter.
Please
observe
the
instructions
in
our
brochure
on
water
as
an
oper
‐
ating
resource.
3.3
Drain
ball
valve
M
FUNCTIONAL
INSPECTION:
15.
Check
the
mobility
of
the
ball.
IF
NECESSARY:
1.
Replace
the
defective
ball
valve.
4
Level
regulation
equipment
4.1
Control
box
W
CLEANING:
2.
Clean
the
control
box.
Once
cleaning
has
been
completed
and
the
scrubber
has
been
filled
with
water
again,
the
level
regulator
setting
must
be
checked.
The
regu
‐
lator
must
be
adjusted
if
necessary.
4.2
Float
W
CLEANING:
3.
Clean
the
float.
4.3
Floater
rod
(mech.
LR)
W
FUNCTIONAL
INSPECTION:
4.
Check
the
mobility
of
the
float
‐
er
rod.
4.4
Magnetic
switch
W
FUNCTIONAL
INSPECTION:
5.
Check
the
switch
function
of
the
magnetic
switch.
4.5
Solenoid
valve
W
FUNCTIONAL
INSPECTION:
6.
Check
the
switch
function
of
the
solenoid
valve.
4.6
Valve
block
W
FUNCTIONAL
INSPECTION:
7.
Check
the
mobility
of
the
valves.
4.7
Surface
cleaner
(optional)
W
VISUAL
INSPECTION:
8.
Check
the
position
of
the
sliding
plate.