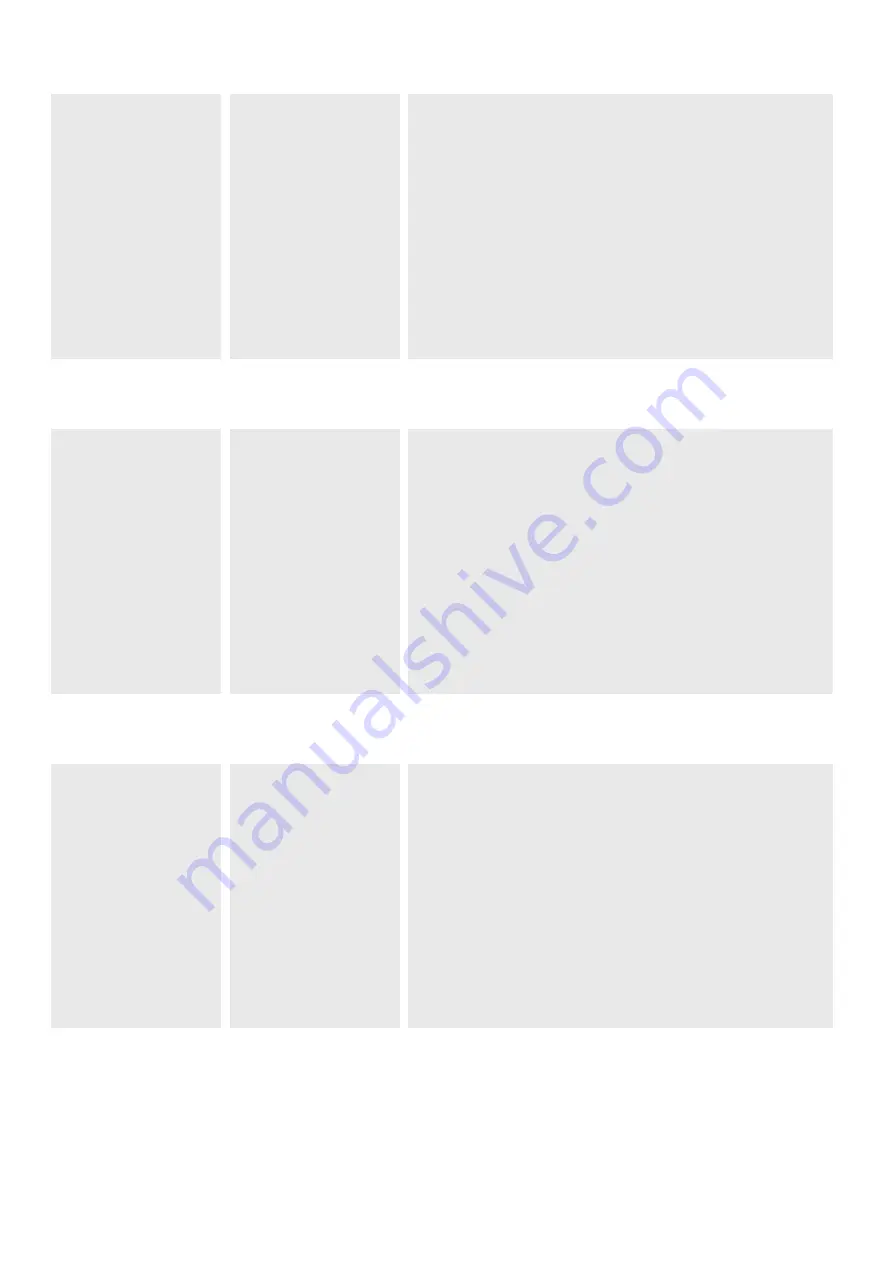
P
age
24
- Manual
FA01383-EN
- 04/2021 - © C
AME S.p.A. - The contents of this manual may be changed at any time and without notice. - T
ranslation of the o
riginal instructions
CX input
Associate a function with the CX input.
F2
CX input
OFF (Default)
C1 = Reopen while closing (photocells)
C4 = Obstacle standby (photocells)
C5 = Immediate closure at the travel end during opening
C7 = Reopen while closing (sensitive edges)
C9 = Immediate closure at the travel end during opening with obstacle standby during
closure
C10 = Immediate closure during opening with obstacle standby during closure (NO
contact)
C11 = Immediate closure during opening with obstacle standby during closure (NC
contact)
C13 = Reopening during closure with immediate stop once the obstacle has been
removed, even with boom not in movement
r7 = Reopen while closing (sensitive edges with 8K2 resistor)
CY input
Associate a function with the CY input.
F3
CY input
OFF (Default)
C1 = Reopen while closing (photocells)
C4 = Obstacle standby (photocells)
C5 = Immediate closure at the travel end during opening
C7 = Reopen while closing (sensitive edges)
C9 = Immediate closure at the travel end during opening with obstacle standby during
closure
C10 = Immediate closure during opening with obstacle standby during closure (NO
contact)
C11 = Immediate closure during opening with obstacle standby during closure (NC
contact)
C13 = Reopening during closure with immediate stop once the obstacle has been
removed, even with boom not in movement
r7 = Reopen while closing (sensitive edges with 8K2 resistor)
CZ input
Associate a function with the CZ input.
F4
CZ input
OFF (Default)
C1 = Reopen while closing (photocells)
C4 = Obstacle standby (photocells)
C5 = Immediate closure at the travel end during opening
C7 = Reopen while closing (sensitive edges)
C9 = Immediate closure at the travel end during opening with obstacle standby during
closure
C10 = Immediate closure during opening with obstacle standby during closure (NO
contact)
C11 = Immediate closure during opening with obstacle standby during closure (NC
contact)
C13 = Reopening during closure with immediate stop once the obstacle has been
removed, even with boom not in movement
r7 = Reopen while closing (sensitive edges with 8K2 resistor)